When Is the Best Time to Install or Replace PTFE Bellows?
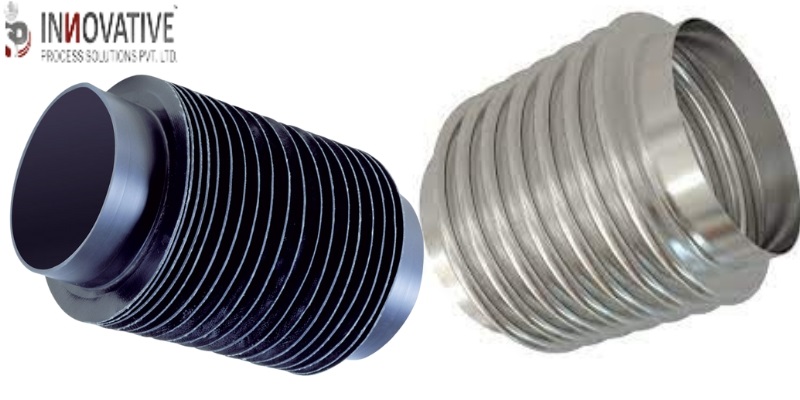
The robustness, chemical resistance, and flexibility of PTFE bellows make them essential to many industrial systems. Like any industrial component, they have a lifespan and optimal circumstances. System integrity and efficiency depend on knowing when to install or replace bellows. To keep your operations running smoothly, this detailed guide will cover PTFE bellow installation and replacement indicators and considerations.
Industrial system efficiency and integrity depend on PTFE bellow installation and replacement timing. Proactive monitoring and intervention before performance declines is ideal. Wear, including cracks or deformations, and performance difficulties like leakage or odd vibrations indicate replacement. Preventive maintenance with replacements helps reduce downtime.
Bellows may also need to be upgraded due to system changes or operating needs. Making sure replacements are available and scheduling installations during system downtimes can simplify the procedure. Strategically maintaining or upgrading PTFE bellows balances operational continuity with system component longevity and reliability.
Understanding the Lifespan of PTFE Bellows
PTFE bellows are praised for their longevity, but several factors can influence their lifespan:
- Operating Environment: Extreme temperatures, corrosion, and mechanical stress can shorten lifespan.
- Material and Manufacturing Quality: Bellows made to standards endure longer.
- Maintenance and Handling: PTFE bellows last longer with proper care.
- PTFE bellows are durable and resilient, making them important in harsh industrial applications. Polytetrafluoroethylene bellows resist chemicals and temperature fluctuations, extending their lifespan.
- The operational environment, frequency of usage, and exposure to harsh chemicals or mechanical stress can affect their lifespan. Maximum service life requires regular maintenance and monitoring.
- If corrected early, wear or performance issues can prevent sudden breakdowns, ensuring the bellows continue to function properly. Understanding how these variables affect bellows lifespan is essential for planning replacements and ensuring the systems they are part of run reliably
Indicators for Replacement
1. Visual Signs of Wear
- Seek apparent damage that could cause leaks or structural breakdown.
- Deformation: Bellows that change shape may not work.
- Visual evidence of wear indicate component health and require maintenance or replacement. In industrial settings, surface fractures, discoloration, and deformation may indicate material fatigue, chemical degradation, or mechanical stress. These signs can be seen regularly, allowing for prompt treatment.
- Early wear detection eliminates catastrophic breakdowns and maximizes machinery performance. Proactive maintenance requires monitoring visual wear signals to maintain industrial dependability and efficiency.
2. Performance Issues
- If fluid or gas leaks from the system, the bellows are not sealing properly.
- Noise or vibration: Unusual sounds or vibrations may indicate that the bellows are not correcting for movement.
- Machinery performance concerns might be subtle but affect operational efficiency. Unexpected noises, vibrations, or output drops indicate urgent issues. Wear and tear, misalignment, and component failure may cause these symptoms.
- Fixing these issues quickly saves future damage and maximizes system performance. Regular monitoring and performance evaluations can identify these issues early for maintenance or modifications. Proactively controlling performance concerns extends machinery life and protects productivity.
3. Material Degradation
- Chemical Wear: Bellows may degenerate if exposed to chemicals beyond their resistance capabilities, requiring replacement.
- Prolonged contact to temperatures outside the permitted range can deteriorate the material.
- Subtle material degradation in industrial components reduces functionality and longevity. Prolonged chemical exposure, severe temperatures, or mechanical stress can cause it. Brittleness, discoloration, and structural abnormalities indicate problems.
- This progressive degradation undermines component integrity and can cause system breakdowns. Understanding its causes and early diagnosis through inspections are crucial to minimizing its impacts. Rapidly addressing material deterioration assures operational safety, performance, and equipment life.
Timing the Installation of New Bellows
Planning Ahead
- System Downtime: Schedule the installation during planned downtime to minimize disruption to operations.
- Availability of Replacement Parts: Ensure that the right size and type of bellows are available to avoid extended system downtime.
Proactive Replacement
- Preventive Maintenance Schedule: Replace the bellows as part of a regular maintenance routine before critical wear occurs.
- After Significant System Changes: If the system has undergone significant changes, such as increased pressure or temperature ranges, consider installing bellows that match the new conditions.
Considerations for Successful Installation or Replacement
1. Compatibility with the System
- Size and Specification Matching: Ensure that the new bellows match the specifications of the system, including size, pressure rating, and chemical compatibility.
- Alignment with Adjacent Components: Proper alignment is crucial to prevent undue stress and ensure a seamless flow within the system.
2. Expert Installation
- Professional Handling: Utilize skilled technicians for the installation to ensure that the bellows are fitted correctly and functioning as intended.
- Adherence to Manufacturer Guidelines: Follow the manufacturer’s instructions for installation to avoid any preventable issues.
3. Post-Installation Inspection and Testing
- Leak Testing: Perform thorough testing for leaks or other performance issues after installation.
- Monitoring Initial Performance: Closely monitor the system’s performance in the initial period after installation to ensure everything is working optimally.
Long-Term Considerations
Predictive Maintenance
- Regular Inspections: Regularly inspect the bellows and adjoining components to catch potential issues early.
- Data-Driven Decisions: Use operational data and historical performance to predict when replacements might be needed in the future.
Continuous Improvement
- Feedback Loop: Use insights from previous replacements or installations to improve the selection and maintenance of PTFE bellows.
- Staying Informed: Keep up with advancements in material technology and manufacturing processes to choose the best options for your system.
PTFE bellows should be installed or replaced based on visual inspections, performance evaluations, and proactive maintenance. Understanding bellows operational demands and recognizing wear and performance concerns can prevent system breakdowns. Keep your operations running smoothly by carefully planning the installation or replacement procedure, confirming compatibility, and involving qualified specialists. PTFE bellows should be replaced before they fail to keep systems running smoothly.
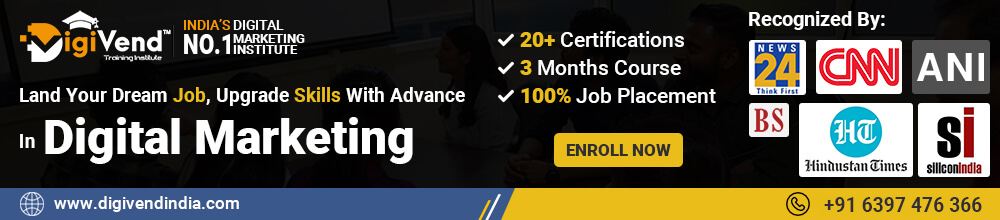