What is the Role of Aerospace and Defence Forgings in Enhancing Structural Integrity?
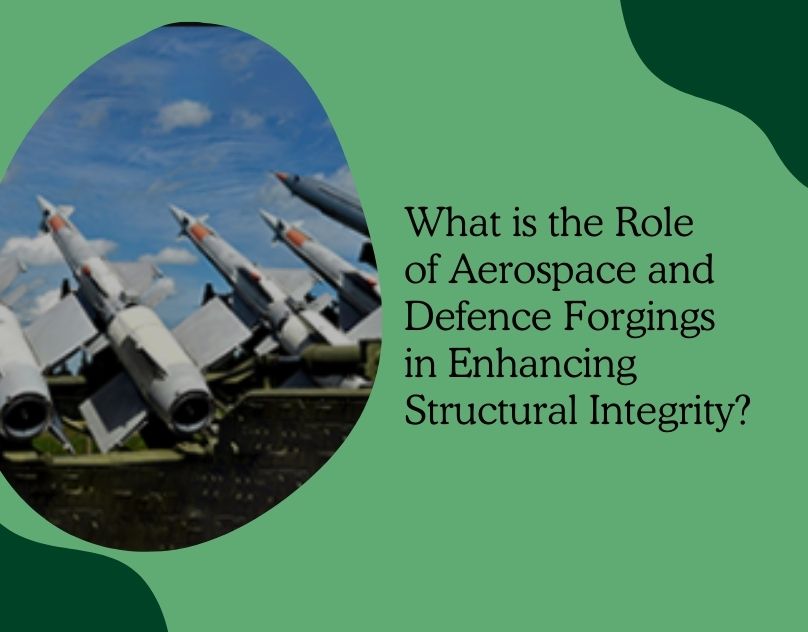
Structural integrity is of utmost importance in the aerospace and defense industries. Aircraft, spacecraft, and defense equipment are designed to endure extreme conditions and high-stress levels, thus ensuring safety for people aboard and success in the mission. Aerospace and defense forgings play a significant role in contributing to this integrity. Precision forgings and metal forging solutions help manufacturers get the parts that yield high strength, durability, and resilience. This blog explains how aerospace and defense forgings enhance structural integrity and why they are inevitable in those high-stakes industries.
Why Forging Matters in Aerospace and Defense
Forging is the process that includes shaping metal through extreme pressure and high temperatures, under which it creates a strong and uniform structure. In aerospace and defense, the structural requirements of components demand materials that can resist not only wear and fatigue but also impact, temperature fluctuations, and environmental factors. Forgings tend to improve the grain structure of metals, which can be very strong and reliable compared to components produced by other means, such as casting or machining. This enhanced strength-to-weight ratio is crucial in aerospace applications, where every gram counts, and structural failure is not an option.
Forging has been used for centuries, but modern advancements have taken this ancient technique to new heights, creating precision forgings and metal forging solutions specifically designed for the unique challenges of aerospace and defense applications.
How Aerospace and Defense Forgings End Structural Strength
1. Improved Material Strength and Toughness
Forging assures alignment of the grain structure of the metal for increased strength and toughness. Such grain flow often contours the shape of the component and helps make it more robust against fractures or other forms of failure. Aerospace and defence forgings create much tougher materials than those made through different methods. For example, forging titanium or aluminum alloy components contain good tensile strength and durability for many structural aircraft purposes, such as aircraft frames, engine parts, and structural supports.
The toughness provided by precision forgings ensures that components can absorb more energy upon impact, reducing the likelihood of catastrophic failures during high-stress events, such as take-offs, landings, and evasive maneuvers.
2. Resistance to Fatigue and Wear
Aerospace and defense equipment exposes the equipment to continuous vibration, varying temperatures, pressure change, etc. Periodic stress often leads to fatigue, a significant cause of failure. It strengthens metals at the microstructural level, resulting from forging and making components more resistant to fatigue and wear over time.
The engineered products for metal forging are anticipated to withstand challenging aerospace and defense conditions that allow components to survive the life cycle of an aircraft or vehicle. Fatigue resistance leads to fewer part replacements, lower maintenance costs, and excellent reliability.
3. Indirect improvement in accuracy and consistency
Tight specifications are needed for aerospace and defense, and hence precision forgings and metal forging solutions are in great demand. Forging techniques can achieve tight tolerances and consistent quality across high-production volumes, which is essential for critical components like turbine blades, landing gear, and structural brackets.
This precision ensures that each part operates in optimal conditions, thus lowering the likelihood of mechanical variations that can affect structural strength. For instance, in jet engines, alterations in part dimension may result in abnormalities within airflow that lower efficiency, and in support structures, tiny differences may cause structural weaknesses.
4. Excellent Resistance to High Temperature
Aerospace and defense parts typically operate under high temperatures, such as in a jet engine in the combustion chamber or a spacecraft heat shield. Forged materials show excellent thermal stability since they are not affected by such conditions of extreme temperatures from losing their properties. Of the alloys usually used for aerospace and defense forgings, titanium, nickel, and stainless steel are selected precisely for their ability to withstand heavy thermal loads.
Metals forging solutions provide materials that can resist high temperatures without losing strength or becoming brittle. Such heat resistance is crucially essential for the structural integrity of components exposed to extremely high temperatures for long periods, such as parts for an engine or missile casing.
5. Fewer Material Flaws
The forging process minimizes the presence of voids, inclusions, and other internal defects that otherwise degrade the integrity of a component. Forged metals have forces applied, compressing a part internally such that air pockets or impurities compress out and are not found as weak points under stress. Such defects in aerospace and defense components are unacceptable because they can cause part failure under load.
Having this part free of such internal defects due to the utilization of precision and aerospace and defense forgings will ensure higher quality consistency. This is crucial for mission-critical applications.
6. Weight Optimization
Aerospace applications demand to achieve a fine harmony between weight and strength. The foremost benefit of more lightly weighted material is fuel efficiency; hence, improving payload-carrying capability is essential for commercial aviation and defense applications. Forging processes allow manufacturers to leverage their opportunities to work with high-strength material in optimized, weight-efficient forms. Optimized weight is not at the cost of the component’s structural integrity; hence, forgings are very much suited for critical parts such as structural beams, engine casings, and wing spars.
Metal forging solutions directly impact the effectiveness and performance of aircraft and equipment that defend a country or nation. This provides an upper hand not only in commercial or business but also in defense.
Applications of Forged Components in Aerospace and Defense
Forged components are an essential part of numerous aerospace and defense systems:
Engines: Forged components, such as turbine blades, crankshafts, and connecting rods, are essential for engines’ performance and strength.
Landing Gear: Forging diverse landing gear components would withstand very high-impact landings and cyclic load.
Structural Components: From airframe structures to wing support, forgings ensure that aircraft can endure aerodynamic forces in their structures.
Defense Systems: In the military, forgings are involved in bomb casings, nose cones of the missiles, etc., requiring shock resistance and strength.
Conclusion
Aerospace and defense forgings play an essential role in enhancing structural integrity. Components stronger, lighter, and more resistant than through any other manufacturing process are produced by the aerospace and defense industries with precision forging and metal forging solutions. Every part ensures resistance to the rigorous demands of aerospace and defense applications, thereby enhancing the safety, reliability, and efficiency the forging process yields. Forging, as such, will continue to hold high importance, significantly, as technology rises and demands better quality in forgings; such components are incredibly resilient in power and efficient for parts of future aerospace and defense.
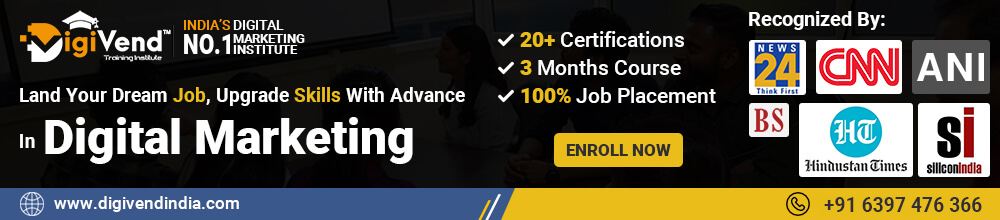