Using Welding Rod: Everything You Need to Know in 2024
Welding is a flexible and essential skill in various industries and 7018 welding rods play a vital role during the welding project. It doesn’t matter whether you are a beginner welder or an experienced welder you will need quality welding rods for your project.
7018 Welding rods are also known as welding electrodes and they are used to conduct current through the fuse of two pieces together to produce the current. The main function of the welding rod is to provide a filler material that melts and bonds with the base metal, creating a strong joint. We provide different types of 7018 welding rod sizes so that you are able to choose the electrode according to your needs.
There are different types of welding rods such as shielded metal arc-wielding electrodes.SMAW electrodes, Gas metal arc welding, Gas tungsten arc welding.
Choosing the appropriate welding rod is one of the most important things for getting high-quality welds.
Understanding welding tools
In 2024 a variety of welding rods will take special care of different welding needs. From shielded metal arc welding [SMAW] to Gas tungsten arc welding [GTAW]. Each cycle uses particular types of rods. Similar categories include rutile, basic, and cellulose electrodes, all of which offer different characteristics such as convenience, entrance, and slag formation. Exploring the traits of each type empowers welders to make the right decision based on project needs.
Selecting the right welding rod
Picking the right welding rod involves meticulous evaluation of factors such as metal composition, Joint setup, welding position, and desired weld characteristics. Different factors like electrode diameter, amperage range, and electrode polarity also influence selection. By leading careful evaluations and manufacturing guidelines. Welders can enhance their rod selection process for the best welding outcomes.
Preparation and Storage
Legitimate dealing and storage are basics for keeping welding rod integrity and performance. Pre-welding planning includes eliminating contaminants such as rust, oil, and moisture from the electrode surface to ensure optimal arc stability and weld quality. Putting away the electrodes in dry circumstances away from humidity and extreme temperatures, mitigates the risk of electrode degradation and ensures consistent performance throughout the welding process.
Techniques and best practices
Mastering the welding rod strategies includes precision, Control, and artfulness. Establishing the right length, electrode angle, and travel speed are essential elements for producing quality welds with minimum defects. Employing proper striking and restarting techniques as well as keeping a consistent hand and steady movement improves weld bead appearance and integrity. Taking on prescribed procedures, for ex, maintaining a clean working environment, utilizing suitable well-being measures, and cultivating proficiency and security in welding tasks.
Advancements and Innovations
In the powerful scene of welding, ceaseless headways, and advancements shape the eventual fate of the business. In 2024, state-of-the-art advancements in terminal innovation, for example, nanocomposite coatings and half-and-half anodes, guarantee improved execution, effectiveness, and natural supportability. Furthermore, mechanization and mechanical technology reform welding processes, offering expanded accuracy, efficiency, and well-being keeping up to date with arising patterns, and embracing mechanical developments positions welders for outcomes in a quickly advancing field.
Conclusions
As we explore the intricacies of present-day welding in 2024, dominating the utilization of welding bars stays a foundation of craftsmanship and capability. By grasping the essentials, choosing the right anodes, sharpening strategies, and embracing advancement, welders can open boundless potential outcomes in metal manufacture and development. Outfitted with information and expertise, the excursion to welding dominance proceeds, impelled by enthusiasm, devotion, and a guarantee of greatness.
All in all, the 7018 welding bar remains as a solid workhorse in the welding business, offering extraordinary flexibility, strength, and execution across a great many applications. Whether it’s developing high rises, manufacturing hardware, or fixing pipelines, this cathode assumes a fundamental part in molding our reality. By grasping its properties, applications, and best practices, welders can bridle the maximum capacity of the 7018 bar, making welds that are solid, but dependable.From agrarian hardware to car fixes, the 7018 welding bar finds adequate use in upkeep and fix assignments. Its convenience and excusing nature make it reasonable for welding many materials and thicknesses, making it a go-to decision for on-location fixes and support projects.Makers and fabricators across different enterprises depend on the 7018 bar for its flexibility and consistency.
For information click on the link:
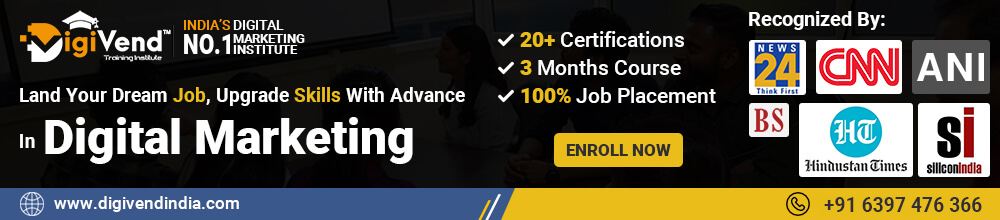