Unraveling Precision: The Art and Technology of Wire Straightening
Introduction:
In the intricate world of manufacturing, the precision and quality of wire components are paramount. Wire straightening, a fundamental process in the production of wires and wire-based components, plays a crucial role in ensuring the accuracy and reliability of the final product. In this comprehensive exploration, we will delve into the significance of wire straightening services, the technologies involved, its applications across industries, and the meticulous process that transforms raw wire into perfectly straight and uniform components.
The Significance of Wire Straightening:
Wire straightening is a foundational step in the manufacturing process, with its significance extending across various industries. The key factors that underscore the importance of wire straightening include:
- Enhanced Precision: Wire straightening ensures that raw wire materials are transformed into straight and uniform profiles. This precision is essential for subsequent manufacturing processes, where accurately shaped wire components are integral to the functionality of diverse end products.
- Improved Quality and Consistency: The straightening process contributes to the overall quality and consistency of wire-based components. By eliminating irregularities and deviations, wire straightening enhances the structural integrity and performance of the final products.
- Versatility in Applications: Wire straightening is not confined to a specific industry; rather, its applications span a multitude of sectors. From automotive and construction to electronics and medical devices, wire straightening is a crucial step in the production of various components used in these diverse fields.
- Efficiency in Subsequent Processes: Straightened wire serves as a stable and predictable starting point for subsequent manufacturing processes, such as bending, forming, or welding. This efficiency is vital for maintaining production timelines and ensuring the reliability of the final products.
Technologies Involved in Wire Straightening:
Several technologies are employed in the wire straightening process, each designed to address specific requirements and achieve varying levels of precision. The common wire straightening technologies include:
- Rotary Wire Straightening: In this method, the wire is fed through a series of rotating straightening rolls that gradually correct any bends or deviations. The rotation of the rolls imparts a straightened profile to the wire as it passes through the machine.
- Turks Head Straightening: Turks Head straightening involves the use of multiple pairs of rolls arranged in a Turks head configuration. The wire is directed through these rolls, and the angular adjustments of each pair work collectively to straighten the wire to the desired specifications.
- Draw Bench Straightening: In draw bench straightening, the wire is pulled through a die or series of dies with decreasing diameters. This process elongates and straightens the wire simultaneously, resulting in a straight and consistent profile.
- Traction Straightening: Traction straightening relies on the application of controlled tension to straighten the wire. The wire passes through a series of adjustable rollers that provide the necessary tension to remove any bends or kinks.
- Centerless Grinding: Centerless grinding is employed for the precision straightening of wires with tight tolerances. The process involves removing material from the wire’s surface, ensuring not only straightness but also achieving precise diameter control.
The Wire Straightening Process:
The wire straightening process involves a sequence of steps, each designed to progressively transform raw wire materials into straight and uniform profiles:
- Material Inspection: The process begins with a thorough inspection of the raw wire material. This step identifies any imperfections, deviations, or irregularities that need correction during the straightening process.
- Feeding into the Straightening Machine: The inspected wire is then fed into the wire straightening machine. The type of machine used depends on the desired straightness specifications and the technology chosen for the particular application.
- Straightening Mechanism: The chosen straightening technology comes into play at this stage. Whether through rotating rolls, turk head configurations, draw benches, or traction straightening, the mechanism corrects any bends or deviations present in the wire.
- Multiple Passes (if required): In some cases, the wire may undergo multiple passes through the straightening machine to achieve the desired level of straightness. This iterative process ensures precision and consistency.
- Final Inspection: Once the wire has undergone the straightening process, a final inspection is conducted. This step ensures that the wire meets the specified straightness requirements and quality standards.
Applications Across Industries:
Wire straightening finds applications across a multitude of industries, contributing to the production of various components used in diverse sectors:
- Automotive Industry: Wire Form Manufacturers are crucial for manufacturing components such as springs, fasteners, and wire forms used in vehicles. The precision achieved in wire straightening enhances the reliability and performance of automotive components.
- Construction and Infrastructure: In construction, straightened wire is used for reinforcing concrete structures. The uniformity achieved through wire straightening ensures the structural integrity of reinforced concrete elements.
- Electronics and Electrical Appliances: Precision straightened wire is essential in the production of components for electronics and electrical appliances. Connectors, terminals, and wire assemblies benefit from the uniformity provided by wire straightening.
- Medical Devices: Straightened wire plays a pivotal role in the manufacturing of components for medical devices, including guide wires, surgical instruments, and orthopedic implants. The precision of wire straightening is crucial for meeting stringent medical standards.
- Aerospace and Aviation: Wire straightening contributes to the production of components used in aircraft and spacecraft. The precision achieved is vital for ensuring the safety and reliability of aerospace systems.
Conclusion:
Wire straightening stands as an indispensable process in the realm of manufacturing, where precision and uniformity are non-negotiable. From enhancing the structural integrity of automotive components to ensuring the reliability of medical devices, wire straightening plays a pivotal role in shaping the modern world. As technology continues to evolve, the art and science of wire straightening will remain at the forefront of precision engineering, contributing to the creation of components that drive innovation and progress across industries.
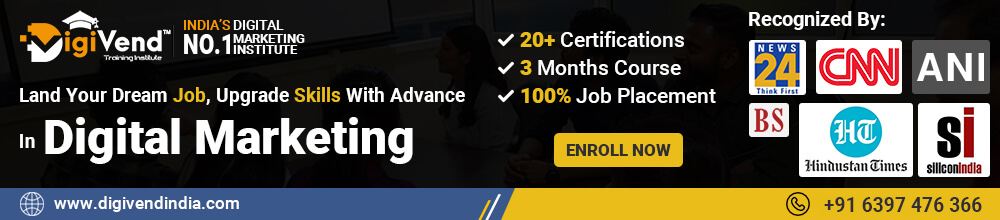