Understanding What Is Hydraulic Actuator, Types, Applications, Working

Actuators are essential to automatically move and operate machines in industries. Among them, hydraulic actuators are widely used due to their unique advantages, although they also have some disadvantages. In this article, we will explain what hydraulic actuator is, how they work, their advantages, and their potential drawbacks.
What is a hydraulic actuator?
A hydraulic actuator is a device that uses a pressurized fluid to create mechanical movement. Depending on the design of the actuator, this movement can be direct (linear) or rotary (rotary). These actuators are essential in many industrial applications because they can provide strong force and precise control.Types of hydraulic actuators
Hydraulic actuators come in many different types, each suited to different needs. The main types are:1. Linear Hydraulic Actuators (Cylinder)
Single-acting cylinder: uses hydraulic fluid to push a piston in one direction; A spring or external force returns it. Double-acting cylinder: Uses hydraulic fluid to move the piston in both directions, providing greater control.2. Rotary Hydraulic Actuators
Van-Type Actuators: Use a rotor with vanes that rotate within a cavity to create rotary motion. They are compact and efficient. Rack and Pinion Actuators: Convert the linear motion of the piston into rotary motion using gears. They are strong and handle high torque.3. Hydraulic Motors
Used for continuous rotary motion found in applications such as conveyor belts and mixers.How a hydraulic actuator works
Hydraulic actuators work on the principle of Pascal’s law, which states that pressure applied to a fluid is transmitted equally in all directions. Here’s a simplified version of how they work:- Hydraulic Power Source: A pump produces a pressurized fluid.
- Control Valve: Control the flow and direction of fluid.
- Actuator: Pressurized fluid enters the actuator, applying force to the piston or vane.
- Motion: The piston or vane moves, creating mechanical motion.
- Return mechanism: A single-acting cylinder uses a spring or external force to return the piston. Double-acting cylinders use hydraulic fluid for both directions.
Applications of Hydraulic Actuators
Hydraulic actuators are used in many industries because they can provide strong force and precise control. Some common applications include:- Industrial Machinery: Used in presses, clamps, and injection molding machines.
- Construction Equipment: Found in excavators, loaders, and cranes.
- Automotive Industry: Used in brake systems, suspension systems, and power steering.
- Aerospace: Employed in landing gear systems, flight controls, and cargo doors.
- Marine: Used in steering systems, winches, and deck machinery.
- Agriculture: Found in tractors, harvesters, and other heavy machinery.
Characteristics of hydraulic actuators
Hydraulic actuators have many advantages:- High Force Output: Can generate significant force, ideal for heavy-duty applications.
- Precise Control: Provide precise control over position, speed, and force.
- Durability: Built to withstand harsh environments and heavy loads.
- Compact design: Provide high power in a small size, save space.
- Versatility: Suitable for both linear and rotary motion.
Disadvantages of hydraulic actuators
However, they also have some drawbacks:- Complexity: Hydraulic systems can be complex to design, install, and maintain.
- Leakage: Hydraulic fluid can leak, leading to maintenance problems and environmental concerns.
- Temperature Sensitivity: Performance may be affected by temperature changes.
- Cost: Initial setup costs may be high due to the need for specialized components.
Key Points
- Hydraulic Actuators convert hydraulic energy into mechanical motion.
- Type includes linear (single and double-acting cylinder) and rotary (vane-type and rack and pinion actuators).
- Applications range from industrial machinery and construction equipment to automotive, aerospace, marine, and agriculture.
- Properties include high force output, precise control, durability, compact design, and versatility.
- Cons include complexity, potential leakage, temperature sensitivity, and high initial cost.
Conclusion
Hydraulic actuators are crucial in many industries due to their ability to provide strong force and precise control. Understanding the different types of actuators, how actuators work, where they are used, and their pros and cons helps select the right actuator for specific needs. While they offer many benefits, their complexity, leak potential, and temperature sensitivity must be considered for optimal performance and longevity.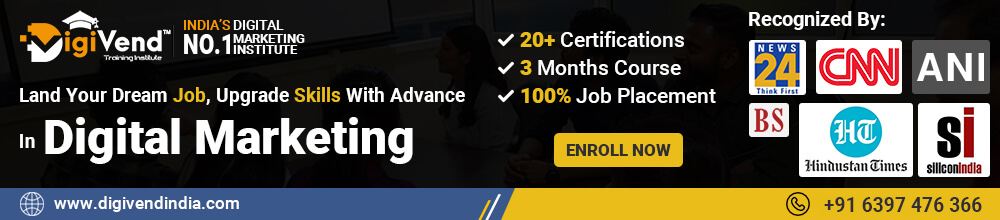