Top 10 Injection Molding Defects and How to Fix Them
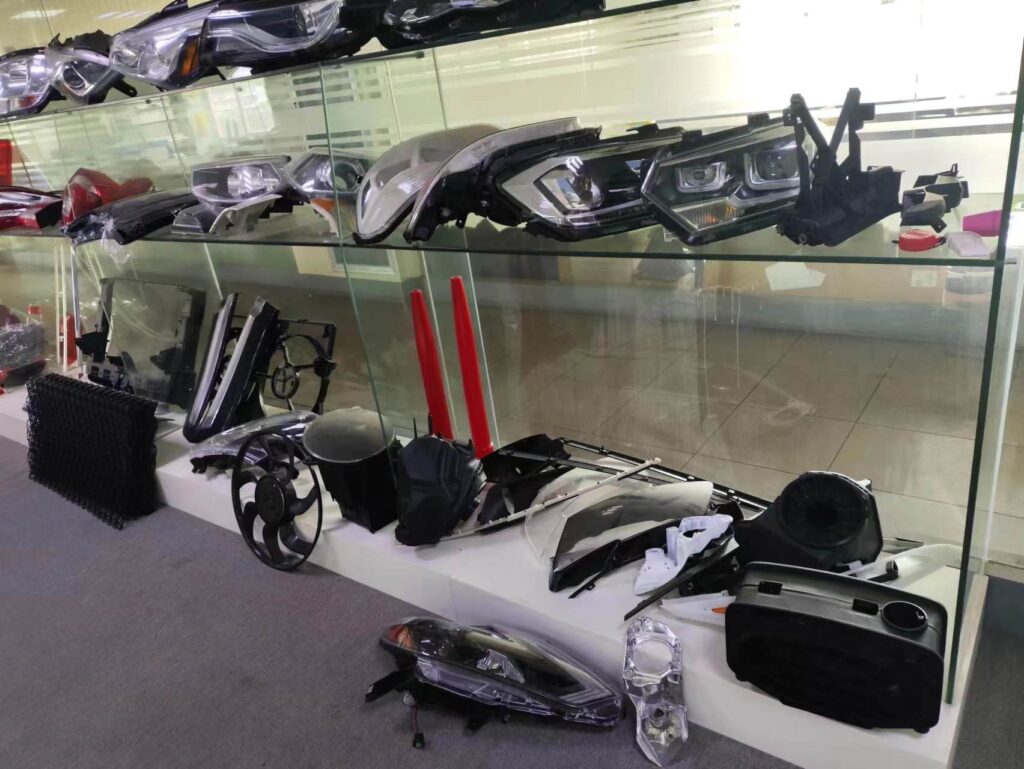
Top 10 Injection Molding Defects and How to Fix Them
Injection molding is a cornerstone of modern manufacturing, but even seasoned professionals encounter challenges. As someone who’s spent two decades in the trenches, I’ve seen my fair share of defects that can turn a production run into a nightmare. But fear not! I’m here to share the top 10 injection molding defects and, more importantly, how to fix them.
1. Sink Marks: The Telltale Dimples
Sink marks are depressions or dimples that appear on the surface of molded parts. They’re often the bane of cosmetic parts and can be a real headache for manufacturers aiming for perfection.
Causes:
- Insufficient cooling time
- Uneven wall thickness
- High melt temperature
Fixes:
- Increase cooling time to allow proper solidification
- Redesign part with more uniform wall thickness
- Lower melt temperature to reduce shrinkage
- Add ribs or gussets to support thicker sections
2. Flash: The Unwanted Excess
Flash, those thin layers of excess plastic that escape the mold cavity, can be a persistent problem. They not only affect part appearance but can also interfere with assembly and function.
Causes:
-
- – Insufficient clamping force
-
- – Worn or damaged mold
– Excessive injection pressure
Fixes:
- Increase clamping force to keep mold halves tightly closed. This simple adjustment can often solve minor flash issues.
- Inspect and repair mold surfaces and parting lines. Regular maintenance is key to preventing flash.
- Reduce injection pressure or speed. Sometimes, less force is more effective in preventing flash.
- Consider mold redesign to improve venting. This may be necessary for persistent flash problems.
3. Short Shots: Incomplete Parts
Short shots occur when the mold cavity isn’t completely filled, resulting in incomplete parts. This defect can range from minor to catastrophic, depending on the part’s function.
Causes:
-
- * Insufficient material flow
-
- * Low injection pressure
* Premature gate freeze-off
Fixes:
- Increase injection pressure and/or speed. This can help push material into all areas of the mold.
- Raise melt temperature to improve flow. Be cautious not to overheat the material.
- Optimize gate location or size. This may require consultation with a mold designer.
- Check for and remove any blockages in the mold. Regular cleaning and maintenance are crucial.
4. Warpage: The Twist in the Tale
Warpage is the unwanted deformation of parts after molding. It can lead to assembly issues and compromised functionality.
Causes:
-
- + Uneven cooling
-
- + Excessive molding pressure
-
- + Improper ejection
+ Material shrinkage
Fixes:
- Balance cooling channels in the mold. This may require mold redesign but can significantly reduce warpage.
- Adjust molding parameters (pressure, temperature, cooling time). Fine-tuning these variables can often mitigate warpage issues.
- Modify part design to reduce stress concentrations. Collaborate with designers to optimize part geometry.
- Consider alternative materials with lower shrinkage rates. This can be an effective solution for persistent warpage problems.
5. Burning: When Things Get Too Hot
Burn marks appear as discolored or degraded areas on the part surface. They’re not just unsightly; they can also weaken the material.
Causes:
-
- – Trapped air in the mold cavity
-
- – Excessive melt temperature
– Inadequate venting
Fixes:
- Improve mold venting. This often involves adding or enlarging vents in the mold.
- Lower melt temperature. Finding the right balance is crucial for preventing both burning and other defects.
- Reduce injection speed to allow air escape. This can be particularly effective for complex part geometries.
- Consider gas-assist injection molding for thick sections. This advanced technique can help prevent burning in challenging designs.
6. Jetting: The Unwanted Stream
Jetting occurs when a thin stream of molten plastic solidifies before the mold cavity is filled, resulting in a visible line or pattern on the part surface.
Causes:
-
- * High injection speed
-
- * Poor gate design or location
* Low melt temperature
Fixes:
- Reduce injection speed, especially at the start of fill. This allows for a more controlled flow front.
- Redesign or relocate gates for better flow distribution. Consult with a mold designer for optimal gate placement.
- Increase melt temperature to improve flow characteristics. Be cautious not to introduce other heat-related defects.
- Consider flow leaders or changes in wall thickness to guide material flow. These design modifications can significantly reduce jetting.
7. Vacuum Voids: The Hidden Hollows
Vacuum voids are internal cavities or bubbles within the molded part. They can significantly weaken the part and lead to failure under stress.
Causes:
-
- + Insufficient holding pressure
-
- + Premature gate freeze-off
+ Air entrapment
Fixes:
- Increase holding pressure and time. This helps pack more material into the mold cavity.
- Optimize gate size to prevent early freeze-off. Larger gates may be necessary for thick-walled parts.
- Improve venting to allow air escape. This may involve adding vents or increasing existing vent sizes.
- Consider mold design changes to reduce thick sections. Collaborating with designers can lead to more moldable part geometries.
8. Flow Lines: The Visible Path
Flow lines are visible patterns on the part surface that show the path of material flow during molding. While sometimes unavoidable, they can be minimized.
Causes:
-
- – Low melt temperature
-
- – Slow injection speed
– Poor gate location
Fixes:
- Increase melt temperature for better flow. This can help material flow more smoothly into the mold cavity.
- Adjust injection speed (usually faster). Finding the right balance is key to reducing flow lines without introducing other defects.
- Optimize gate location for more uniform filling. This may require mold modifications but can significantly improve part appearance.
- Consider texture or matte finish to mask flow lines. This can be an effective solution when flow lines can’t be completely eliminated.
9. Weld Lines: The Weak Seams
Weld lines form where two flow fronts meet during mold filling. They can create visible lines and structural weak points in the part.
Causes:
-
- * Multiple gates or obstacles in flow path
-
- * Low melt temperature
* Insufficient packing pressure
Fixes:
- Optimize gate locations to reduce flow front collisions. This may involve redesigning the mold or adjusting part geometry.
- Increase melt and mold temperatures. Higher temperatures can improve material bonding at weld lines.
- Boost packing pressure to improve material bonding. This helps push material together more forcefully at weld lines.
- Consider design changes to eliminate obstacles in flow path. Removing cores or changing part geometry can sometimes eliminate weld lines entirely.
10. Delamination: The Peeling Problem
Delamination occurs when layers of the molded part separate, often due to contamination or incompatible materials.
Causes:
-
- + Material contamination
-
- + Improper material drying
+ Excessive release agent use
Fixes:
- Ensure proper material handling and storage. This includes using sealed containers and following manufacturer guidelines.
- Thoroughly dry materials before molding. Invest in quality drying equipment and follow recommended drying times and temperatures.
- Minimize use of mold release agents. When necessary, apply them sparingly and evenly.
- Clean mold surfaces regularly to prevent buildup. Establish a routine cleaning schedule to maintain mold cleanliness.
Table: Common Injection Molding Defects and Their Primary Causes
Defect | Primary Cause |
---|---|
Sink Marks | Uneven cooling |
Flash | Insufficient clamping force |
Short Shots | Insufficient material flow |
Warpage | Uneven cooling |
Burning | Inadequate venting |
Jetting | High injection speed |
Vacuum Voids | Insufficient holding pressure |
Flow Lines | Low melt temperature |
Weld Lines | Multiple flow fronts meeting |
Delamination | Material contamination |
Mastering the Art of Defect-Free Molding
As we’ve seen, injection molding defects can arise from a complex interplay of factors. But with the right knowledge and approach, you can significantly reduce their occurrence. Remember, prevention is always better than cure in the world of injection molding.
Implementing a Proactive Approach
To stay ahead of defects, consider implementing these strategies:
- Regular mold maintenance and inspection. This can catch potential issues before they become major problems.
- Comprehensive operator training. Well-trained staff can identify and address issues quickly.
- Investing in advanced process monitoring systems. These can provide real-time data to optimize your molding process.
- Collaborating closely with material suppliers. They can provide valuable insights into material behavior and processing.
By taking a proactive stance, you’ll not only reduce defects but also improve overall production efficiency and part quality.
The Role of Design in Defect Prevention
It’s crucial to remember that many defects can be prevented at the design stage. Collaborating closely with experienced mold makers in China can help identify potential issues before they become costly problems on the production floor.
Key design considerations include:
- Uniform wall thickness. This promotes even cooling and reduces the risk of sink marks and warpage.
- Proper draft angles. These facilitate easy part ejection, reducing the risk of warpage and other ejection-related defects.
- Strategic rib placement. Well-designed ribs can provide strength without causing sink marks or other issues.
- Optimized gate locations. Proper gate placement can improve fill patterns and reduce defects like weld lines and jetting.
A well-designed part not only reduces defects but also improves moldability, cycle times, and overall part quality.
Leveraging Technology for Quality Improvement
In today’s fast-paced manufacturing environment, technology plays a crucial role in defect prevention and quality control. Consider these advanced solutions:
-
- – Simulation software for mold filling analysis. This can predict and prevent issues before the mold is even built.
-
- – In-mold sensors for real-time process monitoring. These provide valuable data to optimize your molding process on the fly.
-
- – Automated visual inspection systems. These can catch defects that might be missed by human inspectors.
– Statistical process control (SPC) software. This helps identify trends and potential issues before they become major problems.
By harnessing the power of these technologies, you can catch defects early and make data-driven decisions to optimize your molding process.
The Importance of Material Selection
Choosing the right material is fundamental to preventing defects. Different plastics have unique processing characteristics, and what works for one may not work for another. Here are some factors to consider:
- Flow properties. These affect how easily the material fills the mold cavity.
- Shrinkage rates. Understanding and accounting for shrinkage is crucial to preventing warpage and dimensional issues.
- Thermal stability. This impacts the material’s behavior during processing and cooling.
- Moisture sensitivity. Some materials require thorough drying to prevent defects like splay or delamination.
Working closely with material suppliers and conducting thorough material testing can help you select the best resin for your application and minimize defect risks.
Continuous Improvement: The Key to Long-Term Success
In the ever-evolving world of injection molding, standing still means falling behind. Embrace a culture of continuous improvement by:
-
- * Regularly reviewing and updating process parameters. What worked yesterday may not be optimal today.
-
- * Encouraging operator feedback and suggestions. Those on the front lines often have valuable insights.
-
- * Staying informed about industry trends and innovations. Attend trade shows, read industry publications, and network with peers.
* Benchmarking your performance against industry standards. This helps identify areas for improvement and celebrates successes.
Remember, every defect is an opportunity to learn and improve. By maintaining a curious and analytical mindset, you’ll continuously refine your processes and produce higher quality parts.
The Value of Local Expertise
While global sourcing has its advantages, there’s significant value in working with local injection molding experts. They can provide rapid response times, easier communication, and a deeper understanding of local market needs and regulations.
Benefits of local partnerships include:
- Faster prototype iterations. Quick turnaround times can accelerate your product development cycle.
- Easier on-site problem-solving. Face-to-face meetings can lead to quicker resolution of complex issues.
- Reduced shipping costs and lead times. This can be particularly beneficial for just-in-time manufacturing.
- Better alignment with local quality standards. Local experts understand and can help you meet regional regulations.
By combining global knowledge with local expertise, you can create a robust and responsive production ecosystem.
Conclusion: Turning Challenges into Opportunities
Injection molding defects may seem daunting, but they’re also opportunities for growth and improvement. By understanding these common issues and their solutions, you’re well-equipped to tackle challenges head-on and produce consistently high-quality parts.</p
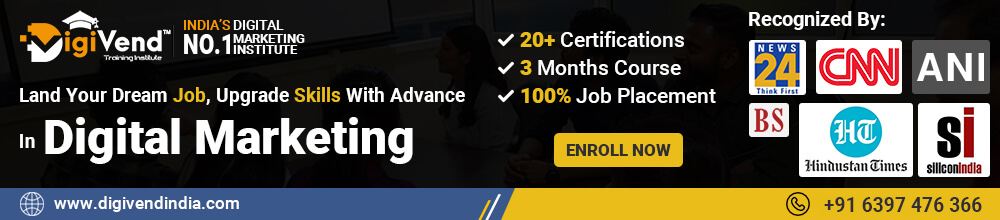