The Essential Guide to Temperature Reference Standards

Introduction to Temperature Reference Standards
In the world of precise temperature measurement, temperature reference standards serve as the foundation for accurate and reliable readings across countless industrial and scientific applications. These critical tools provide known, stable temperature points that enable calibration of instruments and validation of processes where even minor temperature variations can have significant consequences. From pharmaceutical manufacturing to aerospace engineering, maintaining proper temperature reference standards is not just good practice—it’s often a regulatory requirement that ensures product quality, safety, and consistency.
This comprehensive guide explores the different types of temperature reference standards, their applications in various industries, best practices for implementation, and how they form the backbone of reliable temperature measurement systems. Whether you’re a quality control manager, calibration technician, or process engineer, understanding these fundamental references is crucial for maintaining measurement integrity in your operations.
What Are Temperature Reference Standards?
Temperature reference standards are highly accurate, stable sources of known temperatures used to calibrate, validate, and verify temperature measurement devices. They establish traceability to international temperature scales and provide the benchmark against which all other temperature measurements are compared. These standards come in various forms, each suited to specific accuracy requirements and temperature ranges.
Key Characteristics of Quality Reference Standards:
- Metrological traceability to national or international standards
- Stability over time and use
- Reproducibility of temperature points
- Documented uncertainty calculations
- Regular verification against higher-level standards
Types of Temperature Reference Standards
1. Fixed-Point Cells
Fixed-point cells utilize the phase transition temperatures of pure substances to provide extremely accurate reference points. These include:
- Triple point of water (0.01°C) – The gold standard for temperature calibration
- Gallium melting point (29.7646°C) – Common for medical and pharmaceutical applications
- Indium, tin, zinc, and aluminum freezing points – Covering mid-range temperatures
- Silver and gold freezing points – For high-temperature applications
Advantages: Unparalleled accuracy (up to ±0.0001°C), long-term stability
Limitations: Limited to specific temperature points, requires skilled operation
2. Dry Block Calibrators
These portable devices use precisely controlled metal blocks with insertion wells for thermometers:
- Temperature range: -45°C to 1200°C
- Accuracy: Typically ±0.1°C to ±0.5°C
- Best for: Field calibration, industrial settings
3. Liquid Bath Calibrators
Using temperature-controlled fluids, these provide superior uniformity:
- Temperature range: -90°C to 600°C (depending on fluid)
- Accuracy: ±0.01°C or better
- Best for: Laboratory standards, high-precision applications
4. Infrared Blackbody Sources
For non-contact temperature measurement calibration:
- Temperature range: -15°C to 3000°C
- Accuracy: ±0.5°C to ±2°C of setpoint
- Best for: Thermal imagers, radiation thermometers
Importance of Traceability in Reference Standards
A critical aspect of temperature reference standards is their traceability to internationally recognized measurement systems. This traceability chain typically flows from:
- Primary standards maintained by national metrology institutes (NIST, PTB, NPL)
- Secondary standards used by accredited calibration laboratories
- Working standards employed in industrial and laboratory settings
- Process instruments used in daily operations
Maintaining this unbroken chain of comparisons with documented uncertainties is essential for:
- Meeting ISO 17025 and other quality standards
- Ensuring regulatory compliance (FDA, EMA, etc.)
- Supporting quality management systems
- Defending measurement results in audits
Industry Applications of Temperature Reference Standards
Pharmaceutical and Biotechnology
- Autoclave validation (121°C for sterilization)
- Stability chambers (25°C/60%RH for ICH guidelines)
- Lyophilization process monitoring
- Vaccine storage verification (2-8°C cold chain)
Food Processing
- Pasteurization temperature verification
- Cooking and sterilization process control
- Refrigeration and freezing monitoring
- Oven and fryer calibration
Petrochemical and Energy
- Refinery process temperature monitoring
- Pipeline temperature measurements
- Power plant turbine monitoring
- Cryogenic temperature verification
Aerospace and Automotive
- Composite material curing processes
- Engine component testing
- Environmental simulation chambers
- Wind tunnel measurements
Selecting the Right Temperature Reference Standard
Choosing the appropriate standard requires careful consideration of several factors:
1. Required Accuracy
- Research labs may need ±0.01°C or better
- Industrial processes often require ±0.1°C to ±1°C
- Field applications may tolerate ±2°C
2. Temperature Range
- Cryogenic applications: -200°C to 0°C
- Ambient range: 0°C to 100°C
- High temperature: Above 300°C
3. Portability Needs
- Fixed laboratory installations vs. field use
- Size and weight constraints
- Power requirements
4. Number of Calibration Points
- Single-point verification
- Multi-point characterization
- Full-range profiling
5. Maintenance Requirements
- Fixed-point cells need careful handling
- Liquid baths require fluid changes
- Dry blocks need periodic verification
Best Practices for Maintaining Reference Standards
To ensure ongoing accuracy and reliability:
- Regular Calibration – Schedule annual or biennial recalibration
- Proper Storage – Maintain in controlled environments when not in use
- Handling Procedures – Train staff on correct usage techniques
- Documentation – Keep complete records of calibration history
- Environmental Monitoring – Track conditions during calibration
- Uncertainty Analysis – Document and update measurement uncertainties
- Preventive Maintenance – Follow manufacturer’s service recommendations
Emerging Trends in Temperature Standards
The field of temperature metrology continues to evolve with several important developments:
1. Quantum-Based Temperature Standards
- Using fundamental physical constants
- Potentially redefining the kelvin scale
- Improved long-term stability
2. Smart, Connected Standards
- IoT-enabled reference devices
- Automated data logging and reporting
- Remote monitoring capabilities
3. Miniaturized Standards
- Chip-scale temperature references
- Portable fixed-point devices
- Field-deployable high-accuracy solutions
4. Improved Uncertainty Analysis
- Advanced statistical methods
- Better modeling of influence factors
- Automated uncertainty calculation tools
Conclusion: The Critical Role of Temperature Reference Standards
Temperature reference standards form the essential foundation for accurate temperature measurement across virtually every industry that relies on precise thermal control. From ensuring drug efficacy in pharmaceuticals to maintaining safety in energy production, these standards provide the confidence that temperature measurements are correct and reliable.
Implementing and maintaining proper temperature reference standards is not just about meeting regulatory requirements—it’s about protecting product quality, optimizing processes, and ultimately safeguarding end-users. By understanding the different types of standards available, their proper application, and maintenance requirements, organizations can establish robust temperature measurement systems that stand up to scrutiny while supporting operational excellence.
As temperature measurement technology advances, reference standards continue to evolve, offering greater accuracy, improved portability, and enhanced connectivity. Staying informed about these developments ensures your calibration program remains at the forefront of measurement science, ready to meet tomorrow’s challenges with confidence.
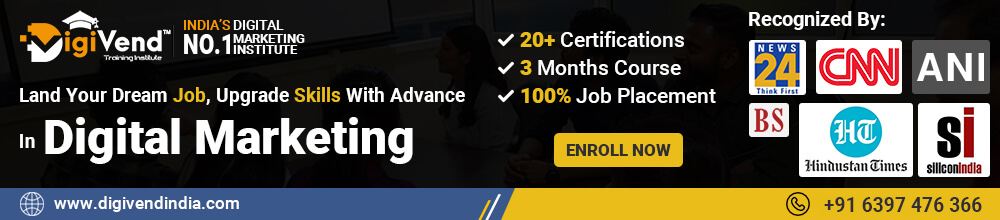