The Essential Guide to Stability Chamber Validation

Introduction to Stability Chamber Validation
Stability chambers are critical in industries such as pharmaceuticals, biotechnology, food storage, and medical devices, where precise environmental conditions (temperature, humidity, and sometimes light) must be maintained to ensure product integrity. Stability chamber validation is the systematic process of verifying that these chambers operate within specified parameters and comply with regulatory standards such as ICH guidelines, FDA 21 CFR Part 11, and EU GMP Annex 15.
This guide explores the importance of stability chamber validation, key steps in the validation process, regulatory requirements, and best practices to ensure compliance and operational reliability.
Why Stability Chamber Validation is Essential
1. Regulatory Compliance
Regulatory agencies like the FDA, EMA, and WHO require documented evidence that stability chambers perform as intended. Non-compliance can lead to:
- Product recalls
- Regulatory warnings or fines
- Delays in product approvals
2. Data Integrity & Product Stability
Stability studies determine shelf life and storage conditions for drugs and biologics. If a chamber malfunctions, it can lead to:
- False stability data
- Compromised product quality
- Risk to patient safety
3. Risk Mitigation
Proper validation identifies potential failures before they impact product stability, reducing costly deviations and investigations.
Types of Stability Chamber Validation
1. Installation Qualification (IQ)
Confirms that the chamber is installed correctly according to manufacturer specifications. Key checks include:
- Proper electrical and mechanical installation
- Sensor and control system verification
- Documentation review (manuals, calibration certificates)
2. Operational Qualification (OQ)
Tests whether the chamber operates as intended under normal conditions. This includes:
- Temperature and humidity uniformity mapping
- Door opening recovery tests
- Alarm system verification (power failure, parameter deviations)
3. Performance Qualification (PQ)
Demonstrates that the chamber maintains required conditions over an extended period (typically 7+ days). Tests include:
- Long-term stability monitoring
- Worst-case scenario testing (full load conditions)
- Data logging and trend analysis
Key Steps in Stability Chamber Validation
1. Temperature & Humidity Mapping
- Objective: Identify hot/cold spots and humidity variations.
- Method: Place calibrated data loggers at multiple locations (minimum 9-12 points, including corners and center).
- Acceptance Criteria: Typically ±2°C for temperature and ±5% RH for humidity (based on ICH Q1A guidelines).
2. Sensor Calibration & Placement
- Use NIST-traceable sensors for accurate measurements.
- Ensure sensors are not placed near walls, doors, or airflow vents.
3. Door Opening Test
- Simulate frequent door openings to assess recovery time.
- Acceptance: Chamber should return to setpoint within 15-30 minutes.
4. Power Failure Recovery Test
- Verify that the chamber restores conditions after a power outage.
- Alarm systems should trigger and record deviations.
5. Alarm & Data Logging Verification
- Test high/low temperature/humidity alarms.
- Ensure data loggers or 21 CFR Part 11-compliant software records all parameters.
Regulatory Guidelines for Stability Chamber Validation
Regulation | Key Requirement |
---|---|
ICH Q1A (R2) | Defines stability testing conditions for pharmaceuticals. |
FDA 21 CFR Part 11 | Requires electronic data integrity and audit trails. |
EU GMP Annex 15 | Mandates qualification and validation protocols. |
USP <1079> | Provides guidelines for storage and stability testing. |
Failure to comply with these standards can result in regulatory actions, including product rejection or facility shutdowns.
Best Practices for Stability Chamber Validation
1. Perform Regular Requalification
- Annual requalification is recommended.
- Revalidate after major repairs or relocations.
2. Use High-Quality Data Loggers
- Wireless loggers reduce cable interference.
- Choose loggers with low uncertainty (±0.1°C or better).
3. Implement Continuous Monitoring
- Real-time monitoring systems alert staff to deviations immediately.
- Cloud-based solutions allow remote access to stability data.
4. Document Everything
- Maintain a validation master plan (VMP).
- Keep records of calibration, mapping studies, and alarm tests.
5. Train Personnel
- Ensure staff understand GxP compliance and proper chamber usage.
Common Challenges in Stability Chamber Validation
1. Non-Uniform Temperature Distribution
- Solution: Optimize airflow with proper shelving and fan adjustments.
2. Humidity Fluctuations
- Solution: Regularly check water supply and humidifier function.
3. Data Integrity Issues
- Solution: Use 21 CFR Part 11-compliant software with audit trails.
4. Power or Sensor Failures
- Solution: Install backup power (UPS) and redundant sensors.
Future Trends in Stability Chamber Validation
1. IoT & Smart Monitoring
- Wireless sensors and AI-driven analytics predict failures before they occur.
2. Automated Validation Software
- Reduces human error in data collection and reporting.
3. Energy-Efficient Chambers
- New designs minimize power consumption while maintaining stability.
Conclusion
Stability chamber validation is a non-negotiable requirement for industries relying on controlled storage conditions. By following a structured IQ/OQ/PQ approach, complying with regulatory standards, and implementing best practices, companies can ensure data integrity, product safety, and compliance.
Is your stability chamber validation up to date? If not, now is the time to review your protocols and implement robust monitoring solutions to avoid regulatory risks.
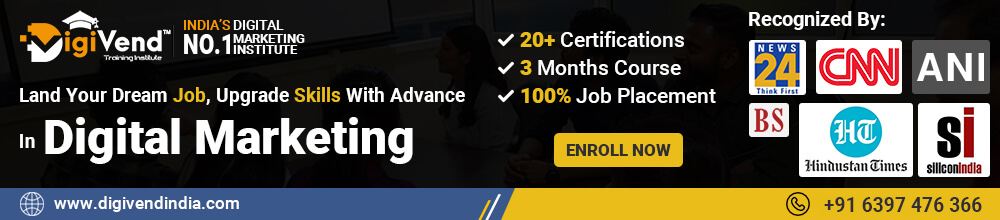