The Critical Role of Validation Equipment in Ensuring Process Reliability and Compliance

Introduction
In highly regulated industries such as pharmaceuticals, biotechnology, medical devices, and food production, ensuring the accuracy, consistency, and compliance of manufacturing processes is non-negotiable. This is where validation equipment plays a pivotal role. Validation equipment is used to verify that systems, processes, and equipment operate within predefined specifications, ensuring product quality, safety, and regulatory compliance.
This article explores the importance of validation equipment, its key applications, regulatory requirements, types of validation equipment, and best practices for implementation.
What is Validation Equipment?
Validation equipment refers to specialized tools and instruments used to test, measure, and document that manufacturing processes, laboratory systems, and production equipment meet established standards. It ensures that processes are consistent, reproducible, and compliant with industry regulations such as Good Manufacturing Practices (GMP), FDA guidelines, and ISO standards.
Why is Validation Equipment Necessary?
- Ensures Product Quality & Safety – Validated processes reduce the risk of defects, contamination, and product failures.
- Regulatory Compliance – Mandatory for industries like pharmaceuticals to meet FDA, EMA, and ISO requirements.
- Process Optimization – Identifies inefficiencies, reducing waste and improving productivity.
- Risk Mitigation – Prevents costly recalls, regulatory penalties, and reputational damage.
Key Applications of Validation Equipment
Validation equipment is used across multiple industries for various critical processes:
1. Pharmaceutical & Biotechnology
- Autoclave Validation – Ensures sterilization effectiveness through temperature mapping.
- Lyophilizer (Freeze Dryer) Validation – Confirms temperature and pressure uniformity.
- Cleanroom Monitoring – Validates air quality, particle counts, and HVAC performance.
2. Medical Device Manufacturing
- Sterilization Validation – Verifies ethylene oxide (EtO), gamma radiation, or steam sterilization.
- Packaging Integrity Testing – Ensures sterile barrier systems remain intact.
3. Food & Beverage Industry
- Pasteurization Validation – Confirms heat treatment effectiveness.
- Environmental Monitoring – Tracks microbial contamination in production areas.
4. Laboratory & Research
- Equipment Calibration – Ensures accuracy of balances, pipettes, and incubators.
- Data Logging & Monitoring – Tracks temperature, humidity, and pressure in storage units.
Types of Validation Equipment
Different validation processes require specialized equipment. Some of the most common types include:
1. Temperature Mapping Systems
- Used for autoclaves, incubators, and storage facilities.
- Includes data loggers, thermocouples, and wireless sensors.
2. Environmental Monitoring Systems
- Measures particle counts, microbial contamination, and airflow in cleanrooms.
- Includes air samplers, particle counters, and anemometers.
3. Pressure & Vacuum Validation Tools
- Ensures lyophilizers, sterilizers, and vacuum chambers operate correctly.
- Includes pressure transducers and vacuum gauges.
4. Humidity & Moisture Analyzers
- Critical for stability testing chambers and packaging validation.
5. Calibration Equipment
- Ensures the accuracy of scales, pipettes, and spectrophotometers.
Regulatory Requirements for Validation Equipment
Compliance with regulatory standards is mandatory in industries where product safety is critical. Key regulations include:
✅ FDA 21 CFR Part 11 – Ensures electronic data integrity.
✅ EU GMP Annex 15 – Covers qualification and validation requirements.
✅ ISO 13485 – Medical device quality management systems.
✅ USP <1225> & <1227> – Guidelines for analytical method validation.
Failure to comply can result in warning letters, fines, or shutdowns.
Best Practices for Using Validation Equipment
- Select the Right Equipment – Choose instruments that meet industry-specific requirements.
- Regular Calibration & Maintenance – Ensures accuracy and extends equipment lifespan.
- Proper Documentation – Maintain detailed records for audits and inspections.
- Train Personnel – Staff should understand proper usage and compliance protocols.
- Periodic Revalidation – Ensures continued accuracy and compliance over time.
Future Trends in Validation Equipment
- Automation & AI Integration – Smart sensors and AI-driven analytics improve efficiency.
- Wireless Monitoring – Eliminates manual data logging, reducing human error.
- Cloud-Based Validation – Enables real-time tracking and remote compliance checks.
Emerging Technologies in Validation Equipment
The validation equipment industry is rapidly evolving with cutting-edge innovations enhancing accuracy and efficiency. IoT-enabled sensors now provide real-time monitoring, allowing instant detection of deviations in critical processes like sterilization or cleanroom environments. Blockchain integration is being explored for tamper-proof validation records, ensuring data integrity for regulatory audits. Additionally, predictive analytics powered by machine learning can forecast equipment failures before they occur, minimizing downtime.
Industry Case Studies
- A leading pharmaceutical company reduced sterilization validation time by 40% using automated wireless data loggers.
- A medical device manufacturer achieved zero FDA observations after implementing AI-driven environmental monitoring.
These advancements underscore how next-gen validation equipment is revolutionizing compliance and operational efficiency.
Why This Matters for Your Business
Staying ahead of technological trends ensures your validation processes remain cost-effective, compliant, and future-proof. Whether adopting wireless sensors or AI analytics, proactive investment in advanced validation equipment can yield long-term ROI by preventing costly non-compliance incidents.
Actionable Takeaway:
Audit your current validation protocols to identify gaps where modern equipment could drive improvements.
Conclusion
Validation equipment is indispensable for ensuring process reliability, regulatory compliance, and product quality across multiple industries. From sterilization validation in pharmaceuticals to clean-room monitoring in medical device manufacturing, the right validation tools help mitigate risks and optimize operations.
Investing in high-quality validation equipment, adhering to regulatory standards, and following best practices will ensure long-term compliance and operational excellence.
Is your facility using the right validation equipment? If not, now is the time to assess your validation processes and implement the necessary tools to stay compliant and efficient.
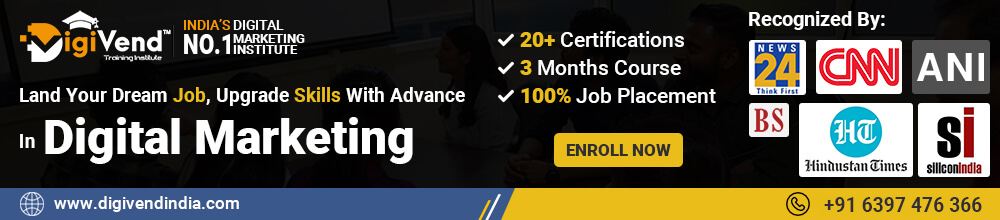