Shrink Film Wrapping Machines vs. Stretch Wrapping Machines: Key Differences
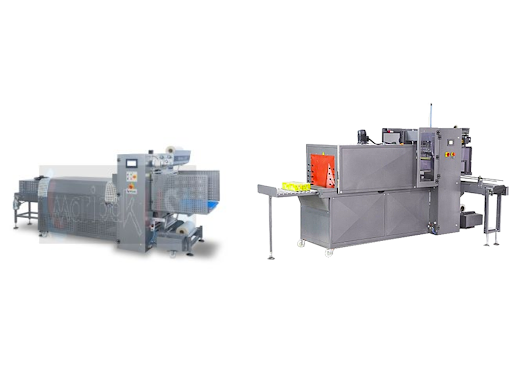
When it comes to packaging products for shipping or storage, businesses have a variety of wrapping solutions available. Among the most popular are shrink film wrapping machines and stretch-wrapping machines. Both serve important roles in ensuring products are securely packed, but they are quite different in terms of functionality and application. In this article, we’ll explore the key differences between these two types of machines and help you decide which is best for your needs.
1. Functionality
Shrink film wrapping machines work by applying heat to shrink a plastic film tightly around a product, creating a sealed, secure package. This is typically used for single-item packaging or bundling multiple items together. The heat causes the shrink wrap packaging to conform tightly to the product, providing excellent protection against dust, moisture, and tampering.
On the other hand, stretch wrapping machines use a stretchable plastic film that is wound around the product, stretching the film as it is applied. The wrapping process uses tension to ensure the film tightly adheres to the product. Stretch wrapping is generally used for palletizing goods, as it can hold larger volumes of products together.
2. Material Differences
Both types of machines use plastic films, but the materials vary. Shrink packaging typically uses materials like PVC, polyethylene (PE), or polypropylene (PP), which become smaller and tighter when heated. This tightness provides a strong protective barrier against environmental elements.
Stretch wrap packaging, on the other hand, uses materials like low-density polyethylene (LDPE) that are stretchy and durable. The stretch film can be applied with varying degrees of tension, depending on the required strength and type of product being wrapped.
3. Efficiency and Speed
In terms of speed, shrink-film wrapping machines tend to be slower compared to stretch-wrapping machines. This is because the shrink-wrapping process requires the application of heat, which takes time to ensure the film shrinks properly. However, shrink-wrap packaging provides a more secure, tamper-proof seal that is ideal for smaller products.
Stretch wrapping machines are generally faster because they simply need to apply the film around the product and stretch it. This makes stretch wrap packaging an ideal choice for high-volume, large-scale applications such as palletizing, where speed is critical.
4. Cost Considerations
When it comes to cost, shrink film wrapping machines and shrink packaging materials may initially seem more expensive due to the heat application equipment and the cost of shrink films. However, the enhanced product protection and the tamper-evident seal often justify the investment, especially for fragile or high-value items.
Stretch wrapping machines, by contrast, can be a more cost-effective solution for bulk packaging. The materials used in stretch wrapping tend to be less expensive than shrink films, and the process is more efficient for larger product volumes.
5. Product Protection and Versatility
While both wrapping techniques provide strong protection, shrink packaging offers a tighter, more secure fit, making it ideal for items that need to be completely sealed off from external elements. This makes it highly suitable for retail-ready products or any item that requires a tamper-evident seal.
Stretch wrapping is better suited for bundling large quantities of products together on a pallet. While the film doesn’t conform as tightly as shrink wrap, it still offers reliable protection against dirt, moisture, and shifting during transportation.
Conclusion
In conclusion, both shrink film wrapping machines and stretch wrapping machines offer unique benefits depending on the type of product you are packaging. If you need a tight, secure, and tamper-evident seal, shrink-wrap packaging is the best option. If you’re working with larger quantities of products or require fast and efficient palletizing, stretch packaging is the way to go. Understanding the key differences between these two types of wrapping systems can help you choose the right one for your business’s needs, ultimately improving efficiency, cost-effectiveness, and product protection.
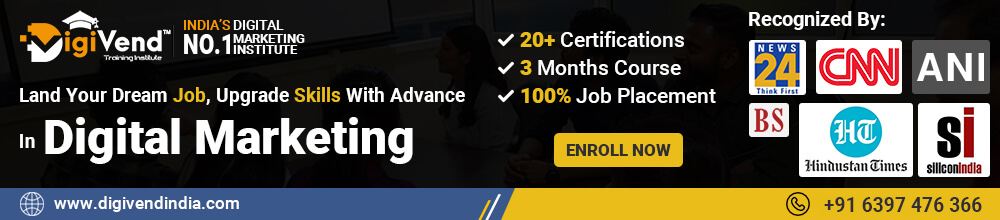