Satin Fabric Manufacturing Plant Project Report 2024: Process, Market, and Sustainability
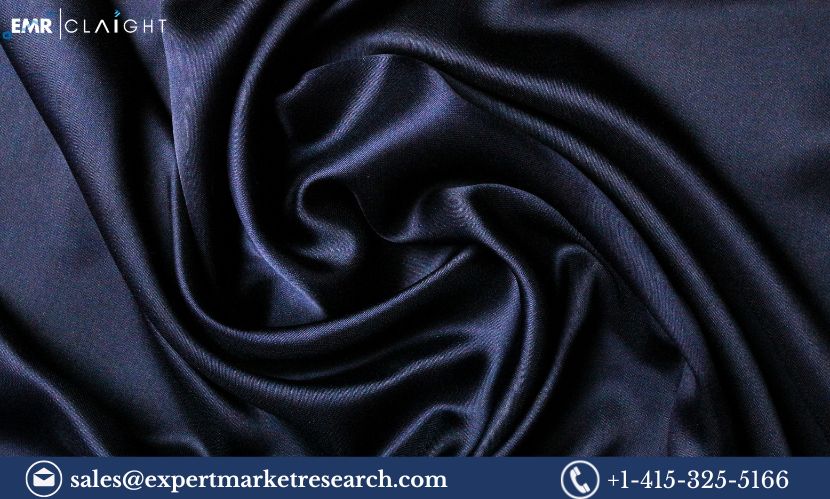
Satin fabric, renowned for its smooth, glossy finish and luxurious appeal, is a versatile material widely used in the fashion and textile industries. Establishing a Satin Fabric Manufacturing Plant can offer significant business opportunities due to the growing demand in sectors such as clothing, upholstery, and home decor. This Satin Fabric Manufacturing Plant Project Report provides an in-depth overview of the steps involved in setting up a satin fabric manufacturing plant, focusing on the key considerations, market trends, equipment requirements, and operational aspects of the business.
Introduction to Satin Fabric and Its Applications
Satin is a weave pattern rather than a specific type of fiber. It is characterized by its smooth and reflective surface, which results from the weaving technique that allows more threads to be exposed on the fabric’s surface. Satin can be made from a variety of fibers, including silk, polyester, acetate, and nylon, each contributing to different qualities in terms of sheen, texture, and durability.
Satin fabrics have a wide range of applications:
- Fashion Industry: Satin is widely used in high-end fashion garments such as evening dresses, wedding gowns, and accessories.
- Upholstery: The fabric is used in home decor, especially for drapery, cushions, and furniture coverings due to its elegant appearance.
- Bedding: Satin is also commonly used in luxurious bedding, particularly in pillowcases and bed linens, known for its soft feel against the skin.
- Accessories: From satin ribbons to handbags and footwear, the fabric’s versatility allows it to be used in a variety of fashion accessories.
The demand for satin fabric continues to grow due to its aesthetic appeal and its widespread use in both the fashion and home furnishings industries.
Get a Free Sample Report with Table of Contents@
Key Considerations for Setting Up a Satin Fabric Manufacturing Plant
1. Market Demand and Growth Potential
The global textile industry has seen an increasing demand for premium fabrics like satin, driven by the following factors:
- Rising Disposable Income: As disposable income levels rise, especially in emerging markets, consumers are increasingly inclined to spend on luxury items, boosting the demand for satin-based products.
- Trends in Fashion and Home Decor: Satin remains popular in high-end fashion and home decor trends due to its ability to convey luxury and sophistication.
- Sustainability Focus: With the growing emphasis on sustainable and eco-friendly fashion, satin made from natural fibers like silk is gaining popularity. However, there is also an increasing preference for satin alternatives made from synthetic fibers such as polyester, which can be more affordable and durable.
2. Raw Materials and Sourcing
The primary raw materials required for manufacturing satin fabric are the fibers used to create the fabric. Depending on the intended product and its price point, manufacturers can choose from several options:
- Silk: The most luxurious option, silk satin, offers exceptional softness and shine. However, it is also more expensive to produce, which may limit its widespread use in mass-market products.
- Polyester: This synthetic fiber is commonly used in satin fabric production due to its affordability and durability. Polyester satin offers similar aesthetic qualities to silk but at a lower cost.
- Acetate/Nylon: Other synthetic fibers like acetate or nylon may also be used in satin fabric production, offering a balance between affordability and shine.
Securing reliable and cost-effective suppliers for these raw materials is essential to ensuring smooth production processes and maintaining product quality.
3. Manufacturing Process of Satin Fabric
The manufacturing of satin fabric involves several critical stages, from sourcing raw materials to weaving and finishing the fabric. Below is an outline of the basic process for satin fabric production:
- Step 1: Fiber Selection and Preparation
The process begins with selecting the appropriate fiber, such as silk, polyester, or acetate. The fibers are then prepared by dyeing (if necessary) and conditioning to ensure they are ready for the weaving process. - Step 2: Weaving
Satin fabric is produced using a satin weave, a method where the yarns are interlaced in such a way that they create a smooth surface. The weaving process involves using a loom to weave the fibers in a way that allows for maximum light reflection, giving the fabric its characteristic glossy finish. - Step 3: Dyeing and Printing
After weaving, satin fabrics may undergo dyeing or printing to add color or patterns. Satin is often dyed using reactive dyes to achieve vibrant, long-lasting colors. Some satin fabrics may also be printed with designs or patterns, depending on market demands. - Step 4: Finishing and Quality Control
The final step involves applying finishing treatments to enhance the fabric’s appearance and durability. These treatments include processes like heat setting, calendering (pressing the fabric to give it a glossy finish), and adding any other required finishes (e.g., water-repellency or flame resistance).The fabric is then subjected to strict quality control procedures to ensure consistency, smoothness, and color accuracy. - Step 5: Cutting and Packaging
Once the satin fabric is finished, it is cut into the required dimensions (such as rolls or sheets) and then packaged for shipment to customers or distributors.
4. Equipment and Infrastructure
Setting up a satin fabric manufacturing plant requires a range of specialized equipment and infrastructure. Some of the key equipment involved includes:
- Spinning Machines: These machines are used for spinning the fibers (such as polyester or silk) into yarns.
- Weaving Looms: Modern shuttle or shuttleless looms are essential for weaving satin fabric, allowing for the satin weave pattern that gives the fabric its characteristic smooth surface.
- Dyeing Machines: Automated dyeing machines are required for efficiently dyeing large quantities of fabric, ensuring uniform color and texture.
- Calendering Machines: These machines are used to press the fabric, giving it the glossy, smooth finish characteristic of satin.
- Finishing Equipment: Other equipment includes machines for heat setting, calendaring, and adding any additional finishes to the fabric.
The plant will also require space for raw material storage, production lines, packaging units, and quality control departments to ensure a smooth workflow and efficient operations.
5. Safety and Environmental Considerations
As with any manufacturing process, safety and environmental regulations must be adhered to when producing satin fabric. Key considerations include:
- Chemical Safety: During the dyeing and finishing processes, chemicals such as dyes, solvents, and finishers are used. It is crucial to ensure proper storage, handling, and disposal of these chemicals to prevent accidents and environmental damage.
- Waste Management: Managing waste, particularly from dyeing and printing operations, is important. Wastewater treatment systems should be installed to ensure compliance with environmental standards.
- Energy Consumption: The manufacturing process can be energy-intensive, especially in the dyeing and finishing stages. Energy-efficient machinery and renewable energy options should be considered to reduce the plant’s carbon footprint.
6. Marketing and Distribution
Once the satin fabric is manufactured, the next step is marketing and distribution. Key strategies for a successful distribution network include:
- Target Market: Satin fabric manufacturers generally target industries such as fashion, home decor, and upholstery. The plant can also explore niche markets by producing specialized satin products such as wedding gowns or luxury bedding.
- Distribution Channels: Products can be sold through wholesale distributors, directly to retailers, or through e-commerce platforms.
- Branding: Developing a strong brand presence in the market can help differentiate the product, especially in the luxury segment. Emphasizing the quality, durability, and eco-friendliness of the fabric can attract consumers looking for premium and sustainable fabrics.
7. Financial and Investment Considerations
Setting up a satin fabric manufacturing plant involves significant capital investment, which includes costs for:
- Plant Infrastructure: Building or renting factory space, installing equipment, and ensuring proper utilities (e.g., water, electricity) are available.
- Raw Materials: Purchasing sufficient raw materials (fibers, dyes, etc.) for production.
- Operational Costs: Salaries, energy costs, maintenance, and other operational expenses.
- Marketing and Distribution: Setting aside budgets for advertising, sales teams, and distribution networks.
A detailed business plan with projected cash flows, return on investment (ROI), and break-even analysis is essential for securing financing and ensuring the profitability of the plant.
FAQs
1. What is satin fabric made from?
Satin fabric can be made from natural fibers like silk or synthetic fibers like polyester, acetate, or nylon, with each offering different qualities in terms of cost, durability, and appearance.
2. What industries use satin fabric?
Satin is commonly used in the fashion industry for eveningwear, wedding dresses, and accessories. It is also used in home decor (upholstery, bedding) and textiles.
3. How is satin fabric manufactured?
Satin fabric is made using a satin weave technique on weaving looms. After the weaving process, the fabric undergoes dyeing, finishing, and quality control before it is cut and packaged.
4. What equipment is required for satin fabric manufacturing?
Key equipment includes spinning machines, weaving looms, dyeing machines, calendering machines, and other finishing equipment.
Media Contact:
Company Name: Claight Corporation
Contact Person: Lewis Fernandas, Corporate Sales Specialist — U.S.A.
Email: sales@expertmarketresearch.com
Toll Free Number: +1–415–325–5166 | +44–702–402–5790
Address: 30 North Gould Street, Sheridan, WY 82801, USA
Website: www.expertmarketresearch.com
Aus Site: https://www.expertmarketresearch.com.au
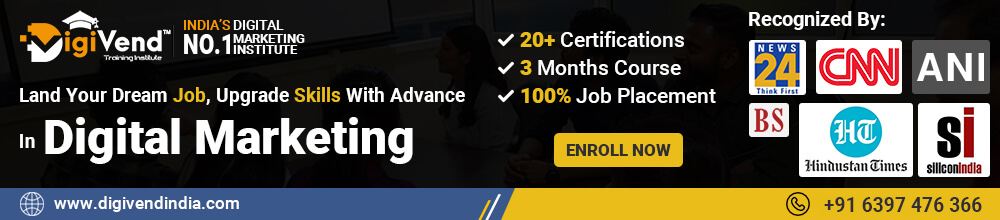