Salt Spray Testing Solutions for Pipes and Valves

Salt spray testing is becoming an essential technique for assessing a material’s durability, particularly for pipelines and valves used in extremely harsh environments. Corrosion may severely shorten the life of pipelines and valves when they are exposed to moisture, chemicals, and salt. Salt spray testing helps to simulate these conditions, providing insights into how these materials withstand corrosion over time. The interpretation of salt spray testing, its importance for pipes and valves, and simple options for corrosion-resistant environments will all be discussed in this article.
What is Salt Spray Testing?
A standardized test method for the corrosion resistance of a material is the salt spray test, commonly referred to as the salt corrosion test. In this experiment, the sample is exposed to salt-laden mist for a predetermined time in a control chamber. By simulating harsh conditions and accelerating the corrosion processes of materials, salt spray testing helps engineers and manufacturers evaluate the performance and durability of their products in hard circumstances.
Why Pipes and Valves Need Salt Spray Testing
Pipes and valves play a vital role in many industries, from water and sewage systems to oil and gas pipelines. Given that corrosion can compromise both safety and functionality, salt spray testing is essential for identifying weak points in materials and ensuring reliability. Without proper testing, corroded pipes and valves may fail prematurely, leading to costly repairs, downtime, and potential hazards.
Salt Spray Testing Standards
Several guidelines are used to ensure accuracy and consistency when performing salt spray testing. Here are a few generally accepted standards:
- A popular standard called ASTM B117 offers instructions on how to do salt spray testing.
- The international standard ISO 9227 specifies the criteria for salt spray testing.
Fulfilling these requirements is essential since they guarantee that test findings are accurate and similar across the globe.
Types of Salt Spray Testing Solutions for Pipes and Valves
According to the corrosive solution being utilized, salt spray tests are often divided into three categories:
- Neutral Salt Spray (NSS) – This technique mimics general corrosion by using a salt solution with a neutral pH.
- Acetic Acid Salt Spray (AASS) – To test more aggressively against elements like aluminum, Acetic Acid Salt Spray (AASS) is added to the solution.
- Copper-Accelerated Acetic Acid Salt Spray (CASS) – Copper-Accelerated Acetic Acid Salt Spray (CASS) is a technique used in the automotive and aerospace industries to evaluate high-performance materials using both acetic acid and copper chloride.
Materials Commonly Tested with Salt Spray Testing
The following materials are suitable for salt spray testing in pipelines and valves:
- Metals – These include alloys of copper, iron, and steel that are prone to corrosion and rust.
- Coated Surfaces – Galvanised and anodized surfaces are examples of coated surfaces that need to be tested to confirm the efficacy of protective coatings.
- Non-Metallic Materials – The ability of some polymers and plastics to withstand deterioration in saline conditions is also evaluated.
Steps in the Salt Spray Testing Process
The salt spray testing procedure is optimized for accurate corrosion detection tools:
- Sample Preparation – The sample is cleaned and cleaned to ensure consistent exposure.
- Chamber Setup – The humidity and temperature of the salt spray chamber are controlled.
- Test Duration – Often lasting hours or even days, the length of testing varies depending on the case and the application being used.
Understanding Salt Spray Chambers
These tests require the use of salt spray chambers. The temperature, humidity, and salt spray concentration may all be adjusted in these chambers, making them the perfect setting for rapid corrosion testing.
Challenges in Salt Spray Testing for Pipes and Valves
Although salt spray testing works well, it has drawbacks. For example, it doesn’t always match up exactly with actual circumstances. The rate of corrosion can be impacted by additional variables such as temperature changes, chemical exposure, and mechanical wear.
Benefits of Salt Spray Testing for Quality Assurance
Salt spray testing plays a vital role in quality assurance by:
- Extending the product’s life by identifying corrosion vulnerabilities.
- Helping manufacturers improve materials and coatings.
- ensure that valves and pipelines can withstand extreme conditions.
Choosing the Right Salt Spray Testing Solution Provider
When selecting a testing provider, consider:
- Experience – Look for companies that have tested pipelines and valves for salt spray.
- Certifications – Ensure certifications follow guidelines such as ISO 9227 and ASTM B117.
Salt Spray Testing Equipment for In-House Testing
Salt spray testing equipment is available for businesses who want to do testing internally. These instruments can be reasonably priced for companies that test products on a regular basis. Nonetheless, outsourcing can guarantee more accurate testing and save up-front expenses.
Cost Considerations in Salt Spray Testing
The cost of salt spray testing can vary based on factors such as:
- Test duration
- Equipment and chamber maintenance
- Sample size
Balancing budget and testing frequency can help businesses determine the best approach.
Conclusion
When assessing and enhancing pipes and valves, particularly those subjected to corrosive conditions, a salt spray chamber is an essential instrument. Companies may take proactive measures to safeguard the products they sell, lower maintenance costs, and increase their lifespan by knowing the basic principles of salt spray testing and its role in quality assurance. Manufacturers have the assurance they satisfy industry requirements and produce trustworthy, long-lasting products by choosing a suitable testing service and procedure.
Frequently Asked Questions (FAQs)
- How long does a typical salt spray test last?
- Depending on the material and standard, tests can last from a few hours to several days to simulate years of corrosion.
- What industries benefit most from salt spray testing?
- Industries like automotive, aerospace, oil and gas, and water utilities rely heavily on corrosion-resistant pipes and valves.
- Is salt spray testing accurate for predicting real-world corrosion?
- Salt spray testing is an accelerated test, meaning it’s not a perfect predictor but still highly valuable for assessing durability.
- Can I conduct salt spray testing in-house?
- Yes, there are machines available for in-house testing, but the investment may be high for some businesses.
- How much does salt spray testing cost?
- Costs vary widely, with factors like test duration, sample preparation, and machine maintenance playing roles in pricing.
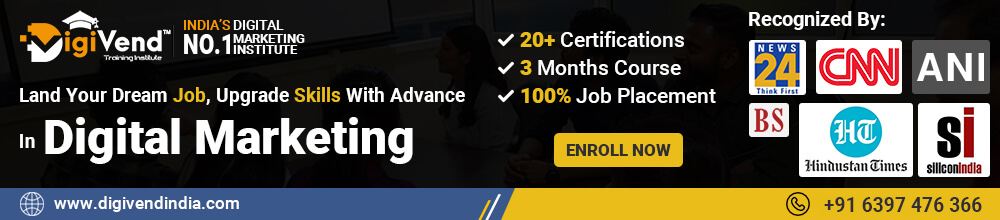