Paper Roll Supplier
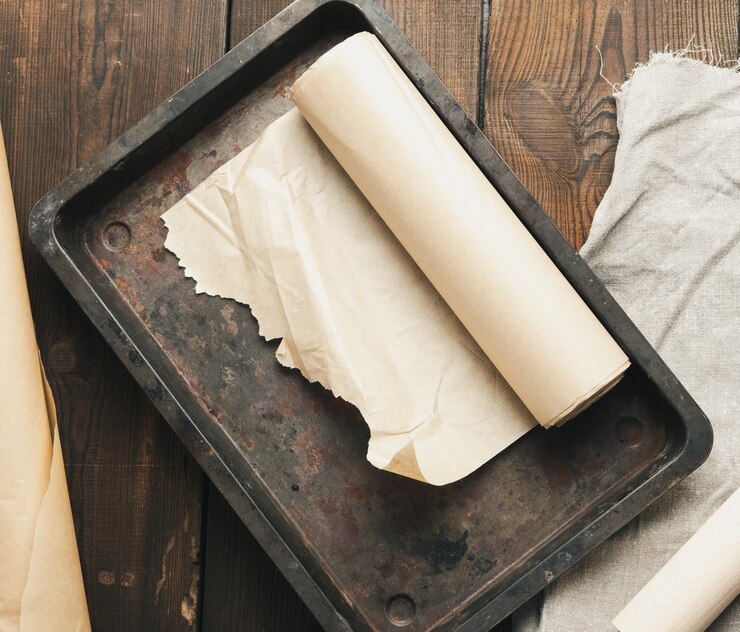
In industries where cash registers, ATMs, and point-of-sale (POS) systems are used, paper rolls are essential. Whether you’re running a retail business, a bank, or even a hotel, paper rolls are a necessity. When it comes to sourcing these products, businesses often face a choice: purchasing from paper roll supplier or directly from paper roll manufacturers. Understanding the differences, advantages, and processes involved in each can help in making an informed decision.
1. What are Paper Rolls?
Paper rolls are cylindrical rolls of paper used in printing receipts, tickets, invoices, and other transactional documents. They come in various forms, such as thermal paper rolls, bond paper rolls, and carbonless paper rolls. Each type is suited to specific industries, depending on the printing method used and the durability needed.
- Thermal Paper Rolls: Ideal for POS systems and ATMs, as they don’t require ink ribbons.
- Bond Paper Rolls: Typically used in impact printers for long-lasting printed documents.
- Carbonless Paper Rolls: Used for multi-part forms, creating duplicates without carbon paper.
2. Paper Roll Suppliers vs. Paper Roll Manufacturers
Paper Roll Suppliers
A paper roll supplier acts as a middleman between the manufacturer and the end user. Suppliers source paper rolls from manufacturers and distribute them to businesses in various industries. Their primary role is to make the product more accessible to a broad customer base. Many suppliers offer diverse products and flexible quantities to accommodate both small and large orders.
Advantages of Buying from Paper Roll Suppliers:
- Variety: Suppliers often carry a range of paper types, sizes, and brands, offering more choices to meet specific business needs.
- Convenience: Suppliers typically maintain stock and can deliver quickly, reducing wait times.
- Customer Support: Many suppliers offer additional services such as consulting, customized order sizes, or technical support for POS machines and printers.
- Lower Minimum Order Quantities (MOQ): Suppliers are likely to offer smaller order quantities, making them suitable for small businesses.
Disadvantages of Buying from Paper Roll Suppliers:
- Higher Cost: Since suppliers act as intermediaries, their prices are often higher due to their markup on the manufacturer’s price.
- Limited Customization: Suppliers might not always offer the specific customizations that manufacturers can provide, such as unique sizing or branding options.
Paper Roll Manufacturers
A paper roll manufacture is the entity responsible for producing paper rolls. Manufacturers handle everything from raw material sourcing and production to quality control. These companies typically sell in bulk and may deal directly with large businesses or distributors.
Advantages of Buying from Paper Roll Manufacturers:
- Cost Savings: Purchasing directly from the manufacturer cuts out the middleman, reducing the overall cost per unit, especially for large orders.
- Customization: Manufacturers can create custom paper rolls tailored to specific needs, including special sizes, branding, or unique paper types.
- Bulk Purchasing: If you require large quantities, manufacturers can provide consistent supply without running the risk of stockouts.
Disadvantages of Buying from Paper Roll Manufacturers:
- Higher Minimum Order Quantities (MOQ): Manufacturers generally require large orders to make it economically viable, which might not be suitable for smaller businesses.
- Longer Lead Times: Since products are made to order, especially for custom requests, lead times may be longer than purchasing from a supplier that holds ready stock.
- Limited Product Range: Many manufacturers specialize in a specific type of paper roll (e.g., thermal or bond paper) rather than offering a variety.
3. Factors to Consider When Choosing Between Suppliers and Manufacturers
a) Order Volume
If you require a large volume of paper rolls regularly, working directly with a manufacturer might be more cost-effective. However, for smaller or irregular orders, suppliers offer greater flexibility and convenience.
b) Customization Needs
For companies that require branded paper rolls or custom sizes, manufacturers are typically the best option as they can provide tailored solutions. Suppliers may not have the same level of customization, but they are ideal if your needs are more generic.
c) Cost Considerations
Manufacturers provide better pricing for large orders, but suppliers may offer competitive pricing for smaller quantities, saving storage costs and minimizing waste.
d) Speed of Delivery
Suppliers usually have products in stock and can ship quickly, making them ideal for businesses that need immediate or frequent deliveries. Manufacturers, on the other hand, may have longer lead times, particularly for customized orders.
4. Paper Roll Production Process
Understanding the production process of paper rolls can also help in selecting the right supplier or manufacturer. Here’s a simplified breakdown of the key steps:
a) Raw Material Sourcing
Manufacturers begin by sourcing high-quality paper pulp, the primary raw material used in paper roll production. The quality and type of pulp determine the characteristics of the final product, such as thickness, strength, and durability.
b) Pulping and Bleaching
The pulp is then processed and bleached to achieve the desired whiteness and texture. For thermal paper, additional coatings are applied to the paper surface, allowing it to react to heat during the printing process.
c) Rolling and Cutting
Once the paper is formed and coated (if necessary), it’s rolled onto large spindles and cut into the required sizes. This step is crucial for ensuring the paper rolls meet the industry-specific standards for width, diameter, and length.
d) Quality Control
Before packaging, manufacturers conduct rigorous quality control tests to ensure the paper rolls meet specific standards, such as tensile strength, thickness, and resistance to environmental factors like humidity.
5. Trends in the Paper Roll Industry
a) Eco-Friendly Options
With growing concern over environmental sustainability, many paper roll manufacturers are shifting toward the use of recycled materials and eco-friendly production processes. Some suppliers also offer BPA-free thermal paper as an alternative to traditional thermal paper that contains the chemical bisphenol A, which has raised health concerns.
b) Customization and Branding
More businesses are opting for customized paper rolls that feature their logo, branding messages, or promotional offers. This trend is growing among retailers and restaurants as a way to enhance brand visibility and customer engagement.
c) Innovation in Technology
Advances in POS systems and ATM technology have led to the development of high-performance paper rolls that can handle faster printing speeds, higher durability, and compatibility with digital systems. Many manufacturers are working closely with technology companies to design paper rolls that meet the specific needs of modern business operations.
6. How to Choose the Right Partner
Whether you choose a paper roll supplier or manufacturer, consider the following when making your decision:
- Reputation: Look for reviews, customer testimonials, and industry recognition.
- Product Range: Ensure they offer the type of paper rolls your business needs (thermal, bond, carbonless).
- Reliability: Can they provide consistent supply, especially if your business relies on high transaction volume?
- Price: Compare pricing structures, including bulk order discounts, shipping costs, and potential markups.
- Customer Service: Opt for partners with strong customer support who can address issues promptly.
Conclusion
Both paper roll suppliers and manufacturers play crucial roles in the paper roll supply chain. Understanding their differences and strengths can help businesses make the right choice based on their operational needs, order volume, and budget. For small businesses with irregular needs, suppliers provide flexibility and convenience. Larger companies that require bulk orders or custom products may benefit more from working directly with manufacturers to save costs and get tailored solutions.
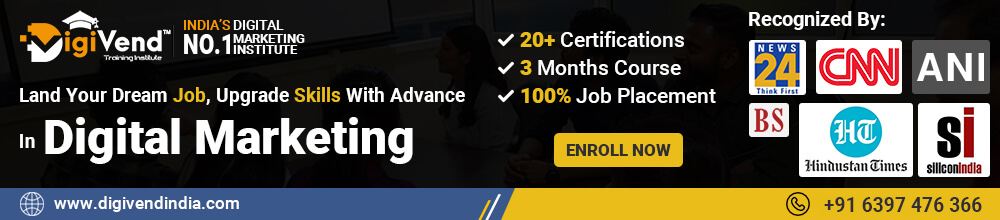