How Pharmaceutical Plant Planning Ensure Compliance with WHO-GMP, US-FDA, and EU-GMP Standards

Pharmaceutical plant compliance with WHO-GMP, US-FDA, and EU-GMP standards is critical for producing high-quality, safe products while meeting global regulatory requirements. Here’s a step-by-step guide to ensure your facility aligns with these stringent guidelines:
The Vital Role of Pharmaceutical Plant Planning
Pharmaceutical plant planning is the foundation for achieving operational excellence, regulatory compliance, and market readiness. A well-structured facility not only ensures smooth processes but also aligns with stringent global standards like WHO-GMP, US-FDA, and EU-GMP.
-
Key Elements of Plant Planning
Effective planning begins with understanding the purpose of the plant, such as API manufacturing, formulation, or packaging. Layouts should be designed to minimize contamination risks, ensure proper segregation of processes, and create efficient workflows. Cleanrooms, HVAC systems, and utilities must meet the highest quality benchmarks.
-
Regulatory Compliance and Licensing
Comprehensive planning is essential for meeting regulatory requirements. Facilities must integrate the standards of Schedule M in India while being adaptable for certifications like FDA and GMP. This includes creating detailed documentation, and validation protocols, and ensuring robust quality management systems.
-
Technology and Automation
Modern pharmaceutical plants leverage automation and advanced monitoring systems to streamline production, enhance accuracy, and maintain consistency. Incorporating these technologies during the planning stage can significantly improve efficiency and compliance.
-
Sustainability in Design
Sustainability is becoming increasingly important. Incorporating energy-efficient systems, water-saving technologies, and waste management solutions into the plant’s design ensures long-term cost savings and environmental compliance.
When it comes to Planning for API Plants, the stakes are even higher. These plants require precise layouts to prevent cross-contamination, maintain controlled environments, and meet global demands. Incorporating high-grade HVAC systems and validated utilities is just the beginning.
The Role of Expert Consultation
Navigating the complexities of pharmaceutical plant planning often requires specialized expertise. Professional pharmaceutical consultants provide valuable insights into facility design, process optimization, and regulatory compliance, helping businesses achieve approval faster and more efficiently.
Planning a pharmaceutical plant is a strategic investment. It ensures quality, safety, and global competitiveness, positioning businesses for sustainable success in the industry.
1. Understand Each Standard’s Requirements
- WHO-GMP: Focuses on good manufacturing practices with an emphasis on product quality, safety, and hygiene.
- US-FDA: Prioritizes compliance with cGMP (current GMP) for market approval in the United States.
- EU-GMP: Ensures product consistency, highlighting documentation and validation to meet European standards.
Familiarize your team with the specific regulations each standard mandates, as they vary in scope and detail.
2. Strategic Pharmaceutical Facility Planning
Designing a facility tailored to regulatory compliance is crucial:
- Create controlled environments that meet hygiene and cleanliness standards.
- Plan layouts to avoid cross-contamination and ensure streamlined workflows.
- Equip facilities with validated machinery, HVAC systems, and filtration technologies.
Work with experienced consultants to integrate these requirements into your facility’s blueprint.
3. Documentation and Validation
- Maintain thorough records for all processes, including Standard Operating Procedures (SOPs), validation protocols, and change management systems.
- Conduct comprehensive validation for equipment, processes, and utilities to demonstrate compliance with GMP standards.
Well-documented processes ease audits and instill confidence in regulatory authorities.
4. Staff Training
- Train personnel in GMP principles, emphasizing hygiene, quality control, and process adherence.
- Regularly update staff on changes in regulatory standards and conduct mock audits to enhance preparedness.
Knowledgeable staff are integral to maintaining compliance.
5. Seek Professional Guidance
- Partner with consultants specializing in WHO-GMP, US-FDA, and EU-GMP compliance. They provide expertise in licensing, facility design, validation, and product registration.
- Conduct gap analyses to identify and rectify non-compliance areas before audits.
6. Audit Readiness
- Prepare for routine inspections by regulatory bodies. Address findings promptly to maintain your facility’s operational status.
- Implement quality management systems (QMS) to ensure continuous improvement.
7. Obtain Approvals
- Address any observations or corrective actions requested during inspections.
- Secure FDA and GMP certifications upon satisfactory compliance.
Conclusion
Ensuring compliance with WHO-GMP, US-FDA, and EU-GMP standards requires meticulous planning, expert guidance, and a commitment to quality. By following these steps and partnering with experienced professionals, your pharmaceutical plant can meet global benchmarks, fostering trust and market accessibility.
For tailored support, consult experts who understand the intricacies of GMP compliance and can guide you through every stage of the process.
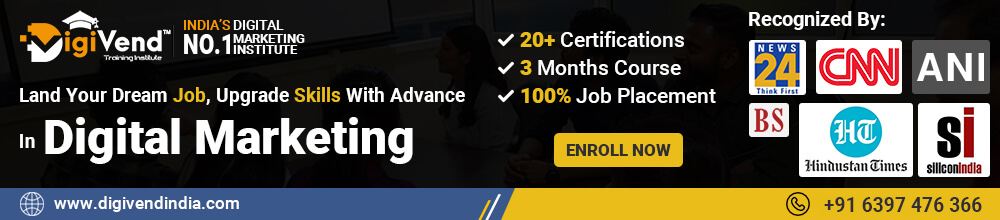