FRL Units Explained: Why Filtration, Regulation, and Lubrication Are Essential
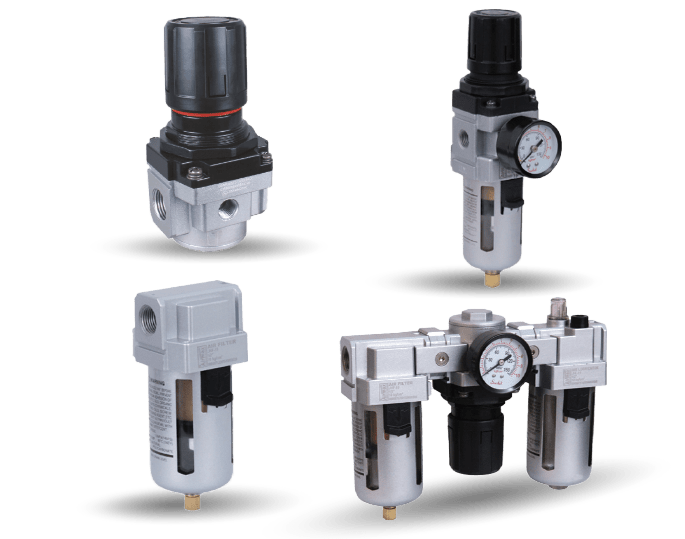
Pneumatic systems, which use compressed air to power machinery and tools, are integral to many industrial processes. However, without proper maintenance and air preparation, these systems can become inefficient, leading to equipment wear and failure. This is where the FRL unit comes in. An FRL unit (Filtration, Regulation, and Lubrication) is a crucial component in any pneumatic system, ensuring that air is clean, pressure is controlled, and essential lubrication is provided to prevent mechanical wear.
In this blog post, we’ll dive into each element of the FRL unit, explaining why filtration, regulation, and lubrication are essential for maintaining the efficiency and longevity of your pneumatic systems.
What Is an FRL Unit?
An FRL unit combines three key functions: Filtration, Regulation, and Lubrication. These functions are typically housed in a single modular unit, which can be easily installed into a pneumatic system. Each component of the FRL unit serves a critical purpose:
- Filtration removes contaminants from the compressed air.
- Regulation ensures consistent and safe pressure levels.
- Lubrication provides oil mist to the air, reducing friction in pneumatic components.
Without an FRL unit, pneumatic systems are vulnerable to damage from moisture, debris, and inconsistent air pressure, all of which can reduce efficiency and lead to equipment breakdowns.
The Importance of Filtration in FRL Units
Compressed air often contains water, dust, rust, and other particles that can cause serious damage to pneumatic equipment. This contamination can lead to:
- Blockages in air passages
- Corrosion of system components
- Premature wear and tear of seals and valves
The filtration component of the FRL unit prevents these problems by removing harmful contaminants from the air before it reaches the pneumatic equipment.
FRL units use filters, typically made of materials like sintered bronze or synthetic fibers, to trap solid particles and separate moisture from the air. The moisture is collected in a bowl beneath the filter, which can then be drained periodically.
By ensuring clean air, filtration helps to protect pneumatic tools and machinery from premature failure, reduce maintenance costs, and improve overall system performance.
The Role of Regulation in FRL Units
In any pneumatic system, maintaining consistent air pressure is crucial for both safety and performance. If the air pressure is too high, it can damage sensitive components or cause malfunction. On the other hand, if the pressure is too low, the system may not function correctly, leading to inefficiency.
The regulation part of the FRL unit ensures that air pressure is kept within the optimal range for the system’s specific needs. The regulator typically consists of a pressure gauge and an adjustable knob, allowing operators to set the desired pressure level.
By keeping the pressure within a safe and consistent range, the regulation component prevents equipment damage, reduces energy consumption, and ensures that the system operates at peak efficiency.
Why is regulation so important?
- Energy Efficiency: Correct air pressure minimizes the energy required to power the pneumatic system.
- Safety: Prevents over-pressurization, which can cause dangerous failures or bursts in the system.
- Consistency: Ensures that tools and machinery perform at their best without fluctuations in pressure.
Lubrication: A Key Factor in Pneumatic System Longevity
Pneumatic systems involve moving parts that create friction, which can lead to heat buildup and wear over time. The lubrication component of an FRL unit helps to mitigate this by introducing a controlled amount of oil mist into the airflow. This oil mist lubricates the internal parts of pneumatic tools and valves, reducing friction and wear.
Lubrication offers several key benefits:
- Reduces Wear: Minimizes friction between moving parts, extending the life of pneumatic components.
- Prevents Corrosion: The oil mist can create a protective layer, reducing the risk of rust and corrosion.
- Improves Efficiency: Properly lubricated parts move more smoothly, reducing energy consumption and improving overall system performance.
However, it’s important to note that not all pneumatic systems require lubrication, particularly those using oil-free components. In systems that do require lubrication, the amount of oil must be carefully controlled to avoid over-lubrication, which can cause clogging and other issues.
The Benefits of Using FRL Units in Pneumatic Systems
Now that we’ve explored each individual function of the FRL unit, it’s clear why these components are so critical to the performance and longevity of pneumatic systems. By filtering out contaminants, regulating pressure, and providing essential lubrication, an FRL unit ensures that your equipment operates smoothly and efficiently.
Here are some of the key benefits of using an FRL unit in your pneumatic system:
- Extended Equipment Lifespan: By protecting against contaminants, excessive pressure, and friction, FRL units help to extend the life of pneumatic tools and machinery.
- Reduced Maintenance Costs: Clean air and proper lubrication reduce the need for frequent repairs and replacements.
- Improved System Efficiency: Consistent air pressure and well-lubricated components allow the system to operate at its optimal level, reducing energy consumption.
- Enhanced Safety: Pressure regulation prevents accidents caused by over-pressurization, and clean air reduces the risk of system failure.
Conclusion
FRL units are an essential part of any pneumatic system, combining filtration, regulation, and lubrication to ensure clean air, consistent pressure, and smooth operation. By using an FRL unit, you can protect your equipment from damage, reduce maintenance costs, and improve the efficiency and longevity of your system.
Whether you’re running a small workshop or a large industrial operation, investing in a high-quality FRL unit will pay off in the long run by keeping your pneumatic systems running smoothly. Understanding the importance of filtration, regulation, and lubrication will help you get the most out of your equipment and maintain a safe, efficient work environment.
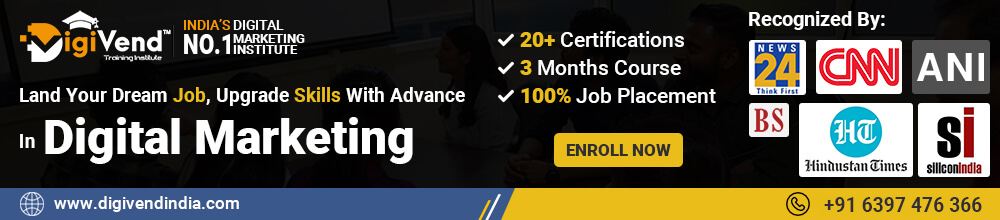