The Best Way to Export and Share Files from a Digitizer for Embroidery
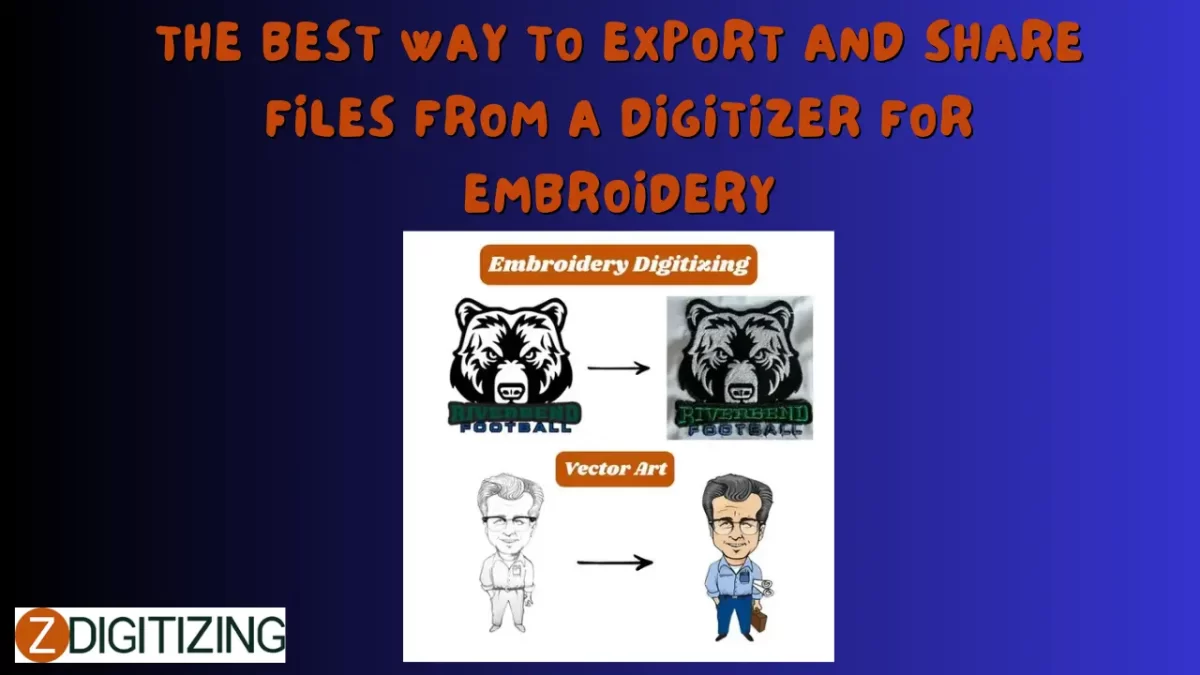
Digitizing for embroidery transforms artwork into stitchable designs, but the journey doesn’t end there—exporting and sharing those files correctly ensures they work seamlessly on embroidery machines and reach clients or team members without a hitch. From choosing the right file format to sharing securely, this step is crucial for success. What’s the best way to export and share files from a digitizer for embroidery? This guide walks you through the process, step-by-step, blending efficiency with quality. Whether you’re handling multi-color designs or prepping for bulk production, here’s how to get it right.
Why Exporting and Sharing Files Matters
A well-digitized design—complete with optimized stitch types and thread density—can falter if exported poorly. The wrong format might not load on an embroidery machine, or details like stabilizer needs could get lost in transit. Proper exporting ensures compatibility, preserves quality, and makes sharing—whether with clients, production teams, or friends—smooth and professional. Let’s dive into the best practices.
Tools You’ll Need
To export and share embroidery files effectively, gather these essentials:
- Digitizing Software: Hatch, Wilcom, Brother PE-Design, or Ink/Stitch (free).
- Computer: To process and export files.
- Embroidery Machine: To test compatibility (e.g., Brother, Janome, or industrial models).
- Design File: Your digitized artwork with stitch types like satin or fill.
- Storage: USB drive, cloud service (e.g., Google Drive), or email.
- Notes: Details on thread density, hooping, and stabilizer for sharing.
Step 1: Finalize Your Design Before Exporting
Why It Matters
Exporting an unpolished design—say, with uneven thread density or sloppy stбез чего-тоitch sequencing—locks in flaws, making them hard to fix later.
How to Do It
- Check Stitch Types: Ensure running stitches (2–3mm) outline cleanly, satin stitches (up to 10mm) suit text, and fill stitches (0.4–0.6mm density) cover solids without gaps.
- Tweak Thread Density: Adjust for fabric—e.g., 0.6mm for stretchy knits, 0.4mm for thick denim—to avoid puckering or sinking.
- Test Hooping: Stitch a sample with proper hooping—tight for stability, not distorted—to confirm the design holds.
- Preview: Use your software’s simulator—catch errors like jumps or misaligned multi-color designs.
Tip
Save a working file (e.g., .EMB for Wilcom)—export only after perfection.
Step 2: Choose the Right File Format
Why It Matters
Embroidery machines read specific formats—picking the wrong one can render your file unusable or degrade quality.
How to Do It
- Common Formats:
- .DST: Universal—works on most machines (Tajima, Brother), preserves stitch types but drops color data.
- .PES: Brother machines—keeps multi-color designs and details like thread density.
- .EXP: Melco machines—simple, widely compatible.
- .JEF: Janome machines—great for home units with color info.
- Match Machine: Check your machine’s manual—e.g., Brother PR1050X uses .PES, industrial Tajima prefers .DST.
- Client Needs: Ask recipients—production teams often want .DST for versatility.
Tip
Export a backup in native format (e.g., .HUS for Hatch)—retains editability.
Step 3: Optimize Export Settings
Why It Matters
Export settings—like stitch length or color sequencing—ensure the file runs smoothly on embroidery machines, avoiding breaks or misalignment.
How to Do It
- Stitch Length: Keep running stitches 2–3mm—longer risks snags in production.
- Color Sequencing: Order multi-color designs logically—e.g., background fills before outlines—cuts trims.
- Pull Compensation: Add 0.2–0.3mm—accounts for fabric stretch during hooping, preventing gaps.
- File Size: Compress if needed—large files (over 10MB) slow older machines; aim for under 1MB for simple designs.
Tip
Use default machine settings in software—e.g., Hatch’s “Brother PES” preset—then tweak as needed.
Step 4: Test the Exported File
Why It Matters
An untested file might fail mid-stitch—wasting thread, fabric, and time, especially if shared with a client.
How to Do It
- Stitch a Sample: Load the file (e.g., .DST) onto your embroidery machine—use scrap fabric with matching stabilizer (tear-away for cotton, cut-away for knits).
- Check Quality: Look for issues—e.g., puckering (too dense), gaps (low thread density), or breaks (poor sequencing).
- Refine: If satin stitches wobble, add underlay; if colors misalign, adjust order. Re-export and re-test.
Tip
Test on the exact machine type recipients use—e.g., Brother for .PES—to ensure compatibility.
Step 5: Share Files Efficiently and Clearly
Why It Matters
Sharing without context—like stabilizer type or thread colors—leaves recipients guessing, risking errors in production or use.
How to Do It
- Export Method:
- USB Drive: Fast for local teams—label clearly (e.g., “Logo_DST_March25”).
- Cloud Storage: Google Drive or Dropbox—secure, shareable links for remote clients.
- Email: Small files (under 5MB)—zip if needed for speed.
- Include Notes: Add a text file or email with:
- File format (e.g., .PES).
- Thread density (e.g., 0.5mm fill).
- Stitch types used (e.g., satin for text).
- Stabilizer recommendation (e.g., cut-away for jerseys).
- Hooping tips (e.g., “tight, no stretch”).
- Secure It: Password-protect zips or links—keeps designs safe.
Tip
Name files descriptively—e.g., “TeamLogo_PES_4x4”—avoids confusion.
Common Export and Sharing Mistakes to Avoid
- Wrong Format: Machine can’t read it. Fix: Confirm compatibility first.
- No Testing: Errors go unnoticed. Fix: Stitch a sample every time.
- Missing Info: Recipients fumble. Fix: Attach detailed notes.
Tips for Exporting and Sharing Like a Pro
- Batch Export: Save multiple formats (e.g., .DST and .PES)—covers all bases.
- Standardize Naming: Use dates or versions—e.g., “CapDesign_0325_DST”—tracks updates.
- Test on Fabric: Match stabilizer and fabric—e.g., tear-away on cotton tees.
- Keep Records: Log export settings—e.g., “0.5mm density, 600 SPM”—for repeats.
Why Exporting and Sharing Right Boosts Embroidery
Exporting and sharing files the best way ensures your multi-color designs, optimized stitch types, and perfect thread density reach their destination ready to shine. It saves time, avoids rework, and builds trust with clients or teams using embroidery machines. In 2025, with tools like Wilcom or free Ink/Stitch, this step is streamlined yet critical. Whether it’s a one-off gift or bulk order, your files will stitch out flawlessly—shared with pride.
Final Thoughts: Send Your Stitches with Confidence
Mastering the best way to export and share files from a digitizer for embroidery ties your hard work together—ensuring designs leap from screen to fabric without a snag. These five steps—finalizing your design, choosing formats, optimizing settings, testing exports, and sharing clearly—keep your hooping tight and your results top-notch. Grab your software, export a file, and share it smartly. From satin stitches to fill patterns, your embroidery is ready to impress—every thread in place!
FAQs About Exporting and Sharing Embroidery Files
What’s the best format for most embroidery machines?
.DST—universal, works across brands like Tajima and Brother.
Can free tools like Ink/Stitch export well?
Yes—Ink/Stitch exports .DST or .EXP with proper settings.
Why won’t my file load on the machine?
Wrong format—check machine manual (e.g., .PES for Brother).
What’s the best way to share multi-color designs?
Cloud link with notes on color order and thread density.
How do I ensure stitch types stay intact?
Export in machine-native format (e.g., .JEF for Janome)—preserves details.
Does file size affect embroidery quality?
No, but large files slow machines—keep under 1MB for efficiency.
Why include stabilizer info when sharing?
Guides hooping—e.g., “cut-away for knits” prevents puckering.
Can I share files securely?
Yes—password-protect zips or use secure cloud links.
How long does it take to export and share?
15–30 minutes—includes testing and note-writing.
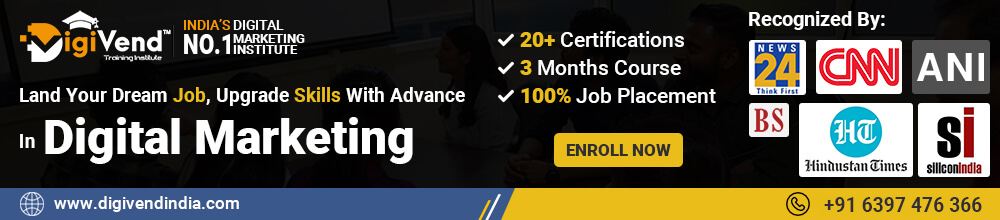