Elevating Production: CNC Metal Bending Advancements
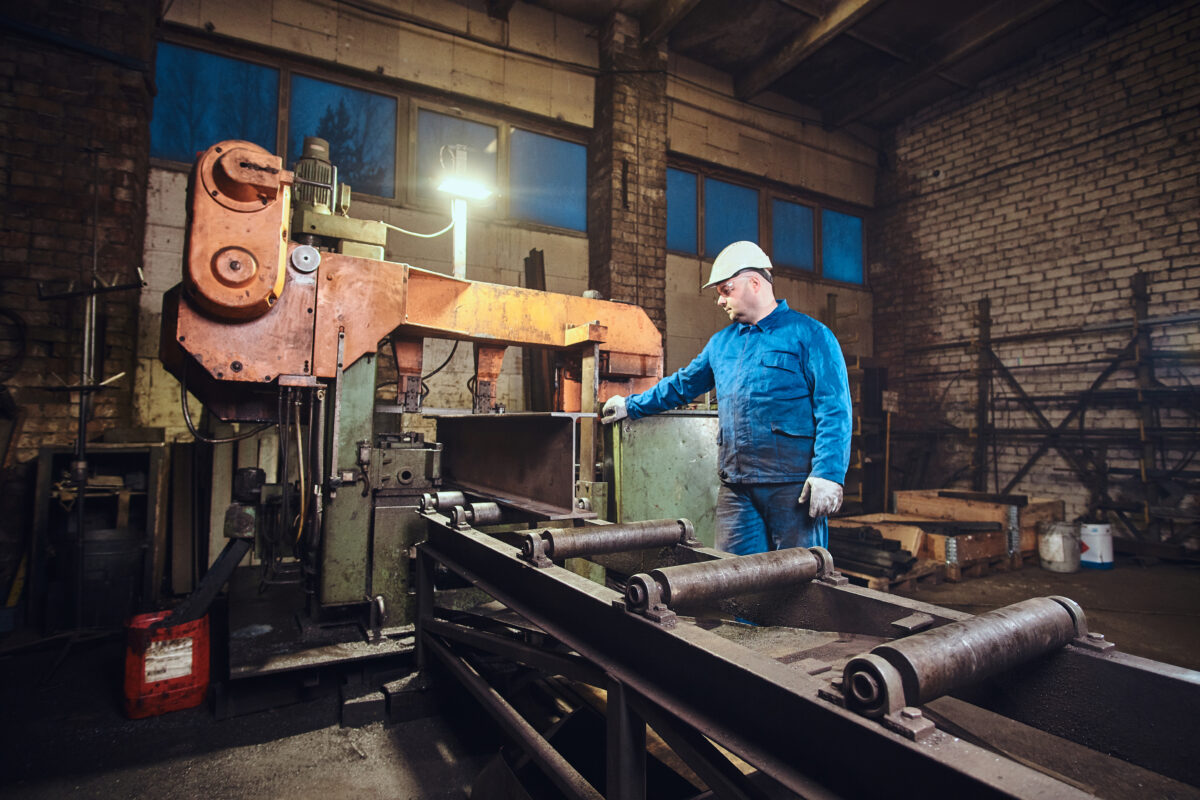
In the world of manufacturing, efficiency is king. Every advancement that enhances productivity holds significant value, and in the realm of metal fabrication, CNC (Computer Numerical Control) machines have revolutionized the process. Among these, CNC metal bending machines stand out as game-changers. Let’s delve into how these advancements are elevating production in the metalworking industry.
The Rise of CNC Metal Bending
CNC metal bending machines have become indispensable tools in modern fabrication facilities. These machines use computer-controlled systems to precisely manipulate metal sheets, offering unparalleled accuracy and repeatability. As technology continues to advance, so too does the capability of these machines, leading to remarkable improvements in production efficiency.
Enhanced Precision Through Automation
One of the key advantages of CNC sheet metal bending machines is their ability to achieve precise bends consistently. By automating the bending process, these machines eliminate the variability that can arise from manual operation. Each bend is executed with meticulous accuracy, ensuring uniformity across production runs. This precision not only improves the quality of finished parts but also reduces waste by minimizing errors and rework.
Increased Speed and Throughput
Another significant benefit of CNC metal bending advancements is the increase in speed and throughput. Modern machines are equipped with advanced servo-driven hydraulic systems and high-speed processors, allowing them to perform bends at a rapid pace. This accelerated production rate translates to shorter lead times and greater output, enabling manufacturers to meet tight deadlines and customer demands more efficiently.
Versatility in Material Handling
CNC metal bending machines are not limited to a single type of metal or thickness. With advancements in tooling technology and machine design, these machines can handle a wide range of materials, including steel, aluminum, copper, and more. Additionally, they can accommodate varying sheet thicknesses, allowing for greater flexibility in product design and fabrication. This versatility opens up opportunities for manufacturers to explore new markets and applications.
Integration with CAD/CAM Software
The integration of CNC metal bending machines with CAD (Computer-Aided Design) and CAM (Computer-Aided Manufacturing) software has been a significant driver of productivity improvements. Design files can be directly imported into the machine’s control system, eliminating the need for manual programming and reducing setup times. CAM software optimizes bending sequences and tool paths, maximizing efficiency and minimizing material waste. This seamless integration streamlines the entire production process, from design to finished part.
Remote Monitoring and Maintenance
Advancements in connectivity technology have enabled remote monitoring and maintenance capabilities for CNC metal bending machines. Manufacturers can now monitor machine performance in real-time, track production metrics, and diagnose issues remotely. This proactive approach to maintenance minimizes downtime and ensures optimal machine uptime, further enhancing productivity and overall equipment effectiveness (OEE).
Energy Efficiency and Sustainability
Modern CNC metal bending machines are designed with energy efficiency in mind. Through the use of servo-driven systems and intelligent power management, these machines consume less energy while maintaining high levels of productivity. Additionally, advancements in material utilization and optimization techniques contribute to reduced waste and improved sustainability. By minimizing environmental impact, manufacturers can align with increasingly stringent regulations and meet the growing demand for eco-friendly products.
Training and Skill Development
As CNC metal bending technology continues to evolve, so too must the skills of the workforce operating these machines. Manufacturers invest in training programs to ensure that operators are proficient in machine operation, programming, and troubleshooting. By empowering their workforce with the knowledge and skills needed to harness the full potential of CNC metal bending machines, manufacturers can maximize productivity and drive continuous improvement initiatives.
Embracing Automation for Labor Optimization
The integration of automation in CNC sheet metal bending machines not only enhances productivity but also optimizes labor utilization. By automating repetitive tasks, such as material handling and part positioning, these machines reduce the reliance on manual labor, allowing operators to focus on higher-value activities like quality control and process optimization. This redistribution of labor resources maximizes efficiency and contributes to a more streamlined production workflow. Additionally, automation mitigates the impact of labor shortages and skill gaps, ensuring consistent output and reducing dependency on manual intervention.
Final Outlook
Therefore, CNC metal bending advancements are propelling the manufacturing industry into a new era of productivity. With enhanced precision, speed, versatility, and integration capabilities, these machines are enabling manufacturers to meet the ever-increasing demands of the market more efficiently than ever before. By embracing these advancements and investing in technology and workforce development, manufacturers can stay ahead of the competition and thrive in an increasingly competitive landscape.
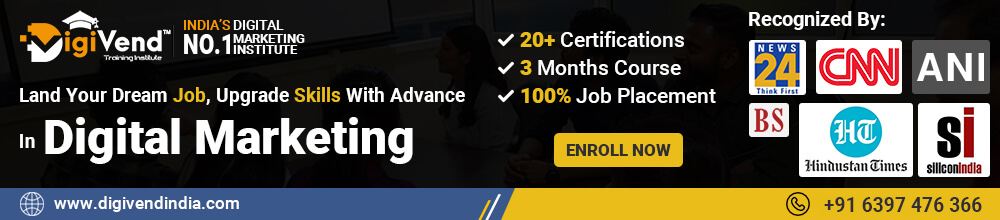