Double Acting Cylinder: How It Works and Why It’s Essential for Pneumatic Systems
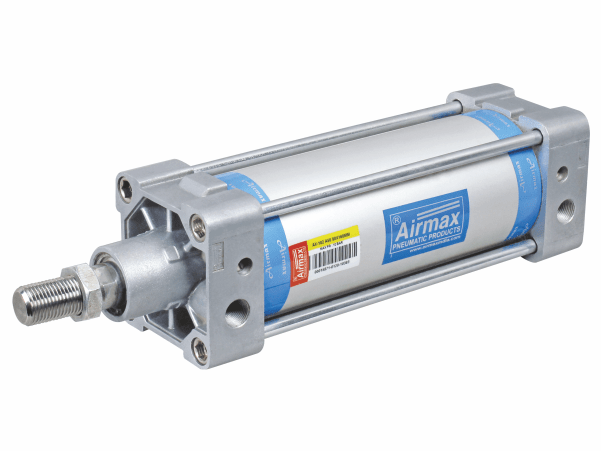
A double acting cylinder is a critical component in pneumatic systems, widely used in industrial automation, manufacturing, and mechanical applications. Unlike single acting cylinders, which use air pressure to move in only one direction, double acting cylinders operate in both directions, providing enhanced efficiency and control.
In this article, we will explore how a double acting cylinder works, its key benefits, and why it is an essential component in modern pneumatic systems.
What is a Double Acting Cylinder?
A double acting cylinder is a type of pneumatic actuator that utilizes air pressure to move the piston in both forward and backward directions. It consists of:
- Cylinder Body – Houses the piston and seals.
- Piston – Moves inside the cylinder to perform mechanical work.
- Rod – Extends from the piston to transfer motion.
- Ports – Two air inlet ports to control movement in both directions.
How Does a Double Acting Cylinder Work?
The working principle of a double acting cylinder involves two main strokes:
1. Forward Stroke (Extension):
- Compressed air enters the first port.
- The air pressure pushes the piston forward.
- The air from the second port exhausts out.
- The piston rod extends outward to perform mechanical work.
2. Backward Stroke (Retraction):
- Compressed air enters the second port.
- The air pressure moves the piston in the opposite direction.
- The air from the first port exhausts out.
- The piston rod retracts to its original position.
This bidirectional movement ensures greater force application, precision, and flexibility in industrial applications.
Key Advantages of a Double Acting Cylinder
1. Greater Force and Control
Since air pressure is applied in both directions, double acting cylinders provide greater force output and more precise control compared to single acting cylinders. This is essential in applications requiring fine-tuned movement.
2. Increased Efficiency
By eliminating reliance on springs, these cylinders reduce energy losses and provide consistent performance in automated systems. This leads to improved speed and efficiency in industrial operations.
3. Versatile Applications
Double acting cylinders are widely used in industries such as:
- Automotive: For robotic assembly lines and lifting mechanisms.
- Manufacturing: In automated material handling, presses, and CNC machines.
- Packaging: For sealing, sorting, and conveyor systems.
- Construction: In heavy machinery and hydraulic systems for lifting and positioning.
- Medical Equipment: Used in advanced prosthetics and automated medical devices.
4. Extended Lifespan
Balanced force distribution reduces mechanical wear and tear, making these cylinders more durable and reliable in demanding environments.
5. Customization and Adaptability
Available in different sizes, materials (stainless steel, aluminum, etc.), stroke lengths, and mounting options, double acting cylinders can be tailored to suit specific industrial applications.
Types of Double Acting Cylinders
1. Tie-Rod Cylinders
- Designed for heavy-duty applications.
- Feature high strength and easy maintenance.
2. Welded Cylinders
- Compact and durable construction.
- Suitable for harsh environments with high pressure requirements.
3. Compact Cylinders
- Short stroke lengths and small size for tight spaces.
- Used in precision applications like robotics.
4. Rotary Actuators
- Convert pneumatic energy into rotational motion.
- Ideal for clamping and indexing applications.
Why Double Acting Cylinders Are Essential for Pneumatic Systems
1. Improved Motion Control
In pneumatic systems, precise control over movement is crucial. Double acting cylinders ensure consistent and controlled operations, enhancing productivity.
2. Higher Load Handling Capability
Because they generate force in both directions, they can handle heavier loads efficiently, making them ideal for industrial applications.
3. Customization and Adaptability
Available in various sizes, stroke lengths, and materials, double acting cylinders can be tailored for different industrial needs.
Maintenance Tips for Double Acting Cylinders
Proper maintenance ensures the longevity and optimal performance of double acting cylinders. Here are some essential maintenance practices:
- Regular Lubrication: Use appropriate lubricants to reduce friction and wear.
- Seal Inspection: Check and replace worn-out seals and gaskets to prevent air leakage.
- Clean Air Supply: Ensure the air supply is free from contaminants, moisture, and debris to avoid clogging.
- Pressure Monitoring: Maintain the recommended air pressure for efficient operation.
- Alignment Check: Ensure proper cylinder alignment to prevent side loads and excessive wear.
Conclusion
A double acting cylinder is an indispensable component in pneumatic systems, offering superior force control, efficiency, and durability. Whether used in industrial automation, robotics, or packaging, these cylinders enhance productivity and reliability.
If you’re looking for a high-performance double acting cylinder for your applications, consult a trusted supplier to get the best fit for your needs.
If you’re looking for a high-performance double acting cylinder, consult a trusted supplier to find the best fit for your specific needs. Proper selection and maintenance will ensure long-lasting performance and operational efficiency.
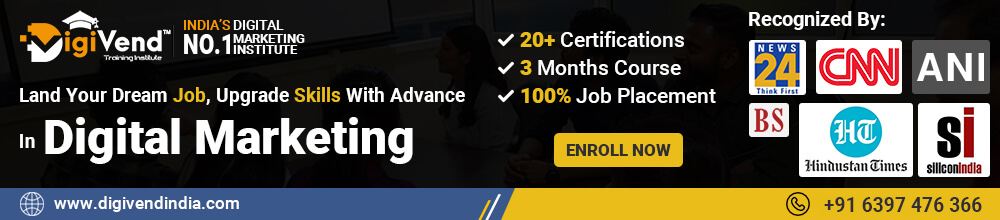