Comprehensive Guide to Salt Spray Test Chambers: Working, Installation, Concepts, and Standards
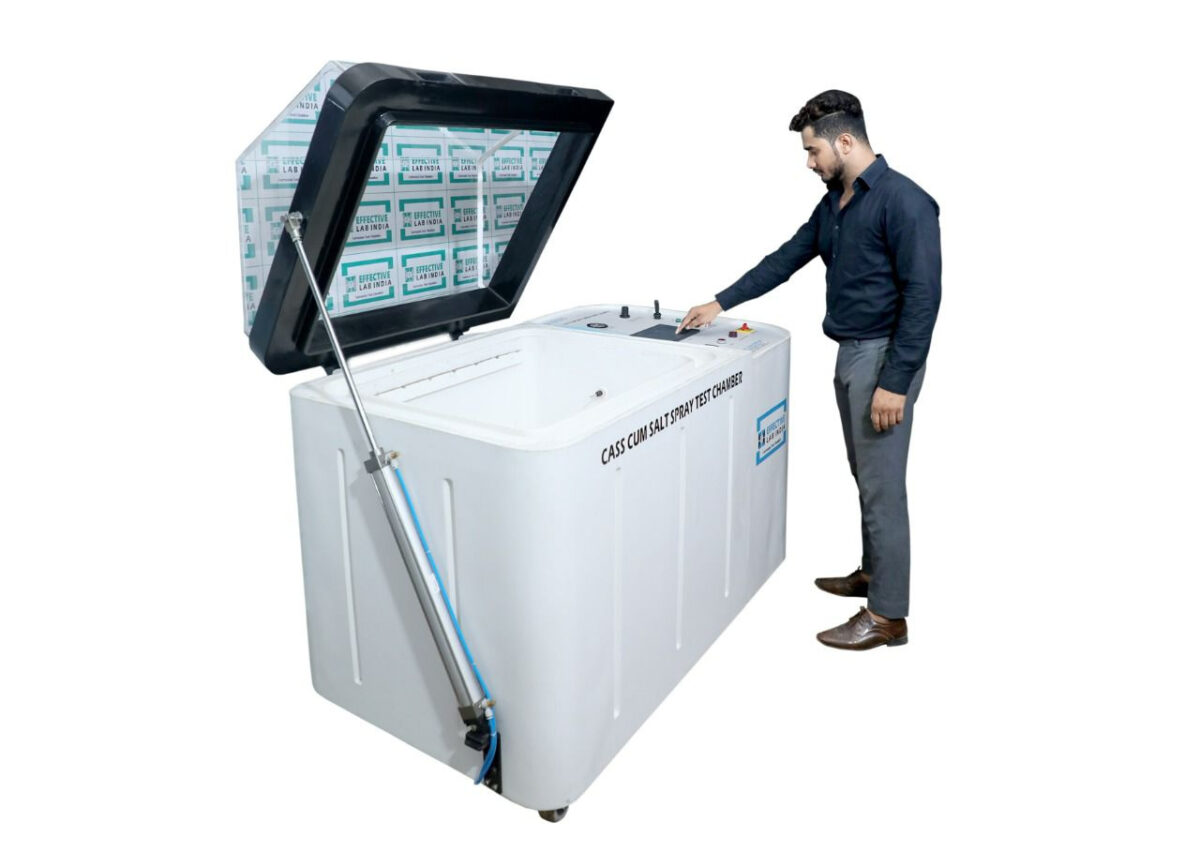
Salt Spray Test Chambers are specialized equipment used to test the corrosion resistance of materials and surface coatings. Manufactured by Effective Lab India, these chambers simulate a corrosive environment to evaluate the durability of coatings, paints, metals, and other materials exposed to salt-laden conditions.
Salt Spray Test Concept
The salt spray test is an accelerated corrosion test that subjects samples to a controlled salt mist environment. This test is commonly used for quality assurance and research purposes to ensure materials meet specific corrosion resistance standards.
- Test Principle: A solution of sodium chloride (NaCl) is atomized using compressed air to create a fine mist inside the test chamber. This mist settles on the samples, exposing them to highly corrosive conditions.
- Purpose: The test replicates harsh environmental conditions to predict the longevity and performance of materials in real-world applications.
Working of Salt Spray Test Chamber
- Preparation:
- Prepare a solution with distilled water and NaCl (typically 5% concentration).
- Ensure the pH of the solution is within the desired range, usually between 6.5 and 7.2.
- Chamber Operation:
- The chamber is equipped with a reservoir for the salt solution, a heater for temperature control, and atomizing nozzles.
- Compressed air draws the solution into the nozzle, creating a fine mist evenly distributed across the chamber.
- The chamber maintains a controlled environment at a specific temperature (e.g., 35°C for neutral salt spray testing).
- Sample Placement:
- Samples are placed at an angle (typically 15-30 degrees) to ensure uniform exposure to the mist.
- The duration of the test depends on the standard or specification being followed.
- Monitoring and Documentation:
- Monitor the chamber’s temperature, mist density, and pH levels throughout the test.
- After the test, inspect the samples for corrosion, blistering, or coating degradation.
Installation Guide
- Site Requirements:
- Install the salt spray test chamber in a well-ventilated area with proper drainage facilities.
- Ensure a stable, vibration-free surface for the chamber.
- Provide access to power supply and compressed air.
- Utility Connections:
- Connect the chamber to a dedicated power outlet with appropriate voltage as specified by the manufacturer.
- Attach a compressed air line with a pressure regulator.
- Initial Setup:
- Calibrate the chamber controls, including temperature, air pressure, and mist flow rate.
- Conduct a trial run to check for leaks, mist uniformity, and temperature stability.
- Maintenance Tips:
- Regularly clean the chamber and its components to prevent salt buildup.
- Replace filters and inspect nozzles periodically for proper functioning.
Standard Analysis
The salt spray test adheres to several international standards, including:
- ASTM B117: The most widely used standard for salt spray testing. Specifies test conditions, sample placement, and evaluation criteria.
- ISO 9227: Provides guidelines for neutral salt spray (NSS), acetic acid salt spray (AASS), and copper-accelerated acetic acid salt spray (CASS) tests.
- JIS Z 2371: A Japanese standard outlining test methods for corrosion resistance evaluation.
Key Parameters Evaluated
- Time to Corrosion: The duration before visible corrosion appears on the sample.
- Coating Performance: Assessment of blistering, peeling, or discoloration.
- Material Durability: Comparison of corrosion rates between different materials or coatings.
Introduction to ASTM B117 Salt Spray Test
Corrosion is a silent enemy of materials, especially metals. But how do you ensure your product withstands harsh environments? That’s where the ASTM B117 Salt Spray Test comes into play. This globally recognized standard is a reliable way to assess a material’s resistance to corrosion, ensuring products meet quality benchmarks.
What is ASTM B117?
Overview of Salt Spray Testing
The ASTM B117 standard outlines the methodology for conducting a controlled salt spray (or fog) test. By simulating a corrosive environment, the test helps evaluate how materials react under conditions that promote rust and degradation.
The Role of ASTM in Testing Standards
The American Society for Testing and Materials (ASTM) developed this protocol to provide a consistent framework. This ensures uniformity across industries when testing corrosion resistance.
Understanding ASTM B117 Salt Spray Test Hours
What Are Salt Spray Test Hours?
The term “test hours” refers to the duration a sample is subjected to the corrosive environment in the salt fog chamber.
Measuring Corrosion Durability
Longer test durations typically indicate higher corrosion resistance. For example, a sample that withstands 500 hours without visible damage is considered more durable than one that shows signs of rust after 100 hours.
Interpreting the Test Results
The results are visually inspected for corrosion, rust, or pitting. The findings help manufacturers determine if the material meets the required standards.
Conclusion
Salt Spray Chambers by Effective Lab India offers a reliable method for assessing the corrosion resistance of materials. Proper installation, regular maintenance, and adherence to test standards are essential for accurate results. These chambers play a critical role in ensuring the quality and longevity of products across various industries, including automotive, aerospace, and construction.
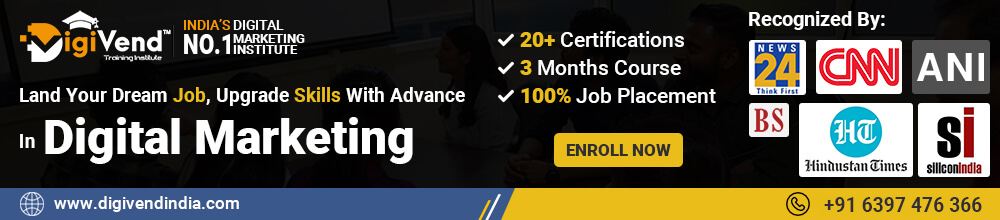