Comparative Analysis: Evaluating Different Industrial Valve Technologies

Industrial valves are critical components in many sectors, including oil and gas, water treatment, chemical processing, and power generation. They control the flow and pressure of liquids, gases, and slurries within a system, ensuring efficient and safe operations. In this article, we provide a comparative analysis of different industrial valve technologies, discussing their design, functionality, and best-use scenarios. We will also highlight the importance of choosing reliable valve manufacturers, such as 4ma Valves automation, and offer insights into why companies across the globe, including top valve manufacturers in india, are turning to advanced valve technologies to optimize their operations.
Overview of Industrial Valve Technologies
Industrial valves come in various types, each with unique features designed to meet specific process requirements. The most common types include:
- Ball Valves: Known for their durability and ability to provide a tight seal, ball valves are popular in applications that require rapid shutoff. They feature a spherical disc (the ball) that controls the flow, rotating 90 degrees to open or close the valve.
- Butterfly Valves: These valves offer a lightweight and cost-effective solution for flow control. The disc rotates to modulate the flow, making them ideal for large pipe diameters. Their simple design allows for easy installation and maintenance, and they perform well in throttling applications.
- Gate Valves: Designed primarily for on/off control, gate valves use a flat or wedge-shaped gate that moves up or down to control flow. They are best suited for applications where minimal pressure drop is essential when the valve is fully open.
- Globe Valves: Globe valves are excellent for throttling applications due to their precise control of flow. Their design allows for smooth and regulated flow, making them a preferred choice in systems where accurate control is crucial.
- Check Valves: Essential for preventing backflow, check valves automatically close when the fluid flow reverses. They play a significant role in protecting equipment and maintaining system integrity.
Comparative Features and Considerations
When evaluating different industrial valve technologies, several factors come into play:
Functionality and Flow Control
- Ball and Butterfly Valves: Both offer quick operation and reliable shutoff capabilities. Ball valves, with their full port design, allow for minimal pressure drop and are typically used in high-pressure applications. Butterfly valves, while generally lighter and more cost-effective, are favored in larger systems where space and weight considerations are crucial.
- Globe and Gate Valves: Globe valves provide excellent throttling control due to their design, which supports gradual opening and closing. Conversely, gate valves are ideal for applications that require a full, unobstructed flow and minimal pressure loss, but they are not well-suited for throttling applications.
Durability and Maintenance
- Material Considerations: The longevity and reliability of a valve depend largely on the materials used in its construction. Industrial environments, especially those involving corrosive substances or extreme temperatures, require valves made from robust materials like stainless steel or specialized alloys. Companies such as 4ma Valves automation emphasize the use of high-grade materials and innovative design to ensure maximum durability and minimal maintenance requirements.
- Operational Efficiency: A key aspect of valve performance is how well it maintains its function over time. For instance, ball valves often require less maintenance due to their simple design, while globe valves, despite their precise control, may necessitate regular adjustments to prevent wear.
Cost Implications
The initial cost of the valve is only one part of the overall investment. Operational efficiency, ease of maintenance, and the potential for system downtime must all be factored into the equation. While butterfly valves tend to be more economical, their efficiency in large-scale operations can make them a cost-effective option over time. Valve manufacturers in India and other regions are continually innovating to strike the right balance between upfront costs and long-term performance, offering solutions that meet both budgetary and operational demands.
The Role of Innovation in Industrial Valves
Modern industrial operations demand valves that are not only reliable but also intelligent. Advances in automation and IoT (Internet of Things) technologies are transforming how valves are monitored and controlled. For example, smart valves equipped with sensors and real-time monitoring capabilities can predict maintenance needs and optimize performance, thereby reducing downtime and improving safety. Companies like 4ma Valves automation are at the forefront of this innovation, integrating advanced technology into their products to offer enhanced operational efficiency and reliability.
Choosing the Right Valve Technology
Selecting the appropriate valve technology involves assessing the specific requirements of your industrial process, including:
- Flow Rate and Pressure: Determine the operational parameters of your system. High-pressure applications might benefit from ball or gate valves, while processes requiring fine control may find globe valves more suitable.
- Environmental Conditions: Consider the operating environment. Corrosive chemicals, extreme temperatures, and high particulate matter may dictate the use of specialized materials or designs.
- System Dynamics: Evaluate the system’s dynamics, including potential pressure surges and flow variability. Understanding these aspects can help in choosing a valve that maintains efficiency and safety under varying conditions.
Conclusion
In the ever-evolving industrial landscape, the choice of valve technology can have a significant impact on process efficiency, safety, and cost management. By conducting a comparative analysis of different valve types—ranging from ball and butterfly valves to globe and gate valves—industry professionals can make informed decisions tailored to their unique needs. The integration of modern automation technologies further enhances the performance and reliability of these systems. As the global market continues to expand, trusted suppliers such as 4ma Valves automation and leading valve manufacturers in india are setting new benchmarks in quality, innovation, and service, ensuring that industrial operations remain both efficient and secure in the face of growing challenges.
Also, read A Comprehensive Guide to Industrial Valve Maintenance
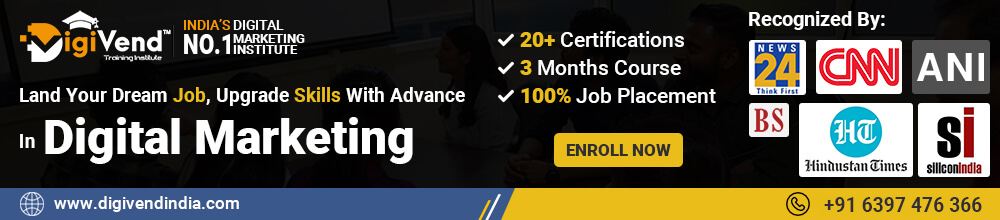