CNC Spindle Basics: An In-Depth Guide to Functionality and Types
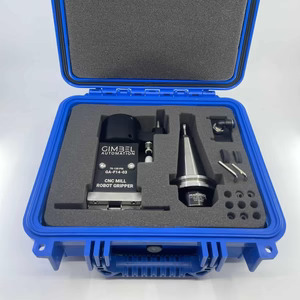
The CNC spindle is at the heart of every CNC machine, serving as the core component that drives tools, manages speed, and ensures precision. Understanding the different types of CNC spindle, how they operate, and their role in machining is essential for anyone working in CNC technology. In this guide, we’ll explore the fundamentals of CNC spindle, their types, and essential maintenance tips to maximize performance.
What is a CNC Spindle?
A CNC spindle is a rotating component in a CNC (Computer Numerical Control) machine that holds and drives the cutting tool. Its primary function is to rotate the tool at high speeds, allowing for precise machining operations on various materials, including metal, wood, and plastic. The spindle’s design, material, and motor power all play a crucial role in determining the overall efficiency and capability of the CNC machine.
Types of CNC Spindles
CNC spindles come in various types, each designed for specific applications and machining processes. Understanding the different types can help you choose the right spindle for your CNC machine.
- Air-Cooled Spindles
Air-cooled spindles use air for cooling, which is essential when performing high-speed machining tasks. They are typically lightweight and easy to install. However, they may not be as efficient as water-cooled spindles for prolonged operations. - Water-Cooled Spindles
These spindles utilize water for cooling and can operate at higher speeds for extended periods without overheating. They are commonly used in demanding machining applications, where temperature control is critical. - Direct Drive Spindles
Direct drive spindles connect the motor directly to the spindle shaft, eliminating the need for belts or pulleys. This design allows for high-speed operations and increased accuracy, making them ideal for precision machining. - Belt-Driven Spindles
Belt-driven spindles use belts to transfer power from the motor to the spindle. This type allows for variable speed settings and is commonly found in CNC milling machines. However, they may require more maintenance than direct drive spindles. - High-Frequency Spindles
These spindles operate at very high RPMs and are typically used for precision tasks such as engraving or high-speed milling. They are ideal for materials that require fine detail and minimal heat generation.
How CNC Spindles Work
CNC spindle function by converting electrical energy into mechanical energy. The motor within the spindle drives the spindle shaft, which in turn rotates the cutting tool. The speed of the spindle can be adjusted based on the material being machined and the desired finish quality. Here’s a basic overview of the operational process:
- Power Input: The spindle receives electrical power, either from a direct connection or through an external power source.
- Motor Activation: The motor activates, turning the spindle shaft.
- Tool Rotation: The connected cutting tool rotates at a predetermined speed, allowing it to engage with the material being machined.
- Cooling Mechanism: As the spindle operates, it generates heat, which is dissipated through air or water cooling to maintain optimal performance.
Importance of CNC Spindles in Machining
CNC spindles are critical for several reasons:
- Precision: The quality of machining largely depends on the spindle’s ability to maintain speed and accuracy. A well-functioning spindle ensures clean cuts and fine finishes.
- Versatility: With various types of spindles available, CNC machines can handle a wide range of materials and applications, from simple drilling to complex milling operations.
- Efficiency: High-speed spindles reduce machining time, increasing productivity and reducing operational costs.
Maintenance Tips for CNC Spindles
Proper maintenance of CNC spindle is essential for maximizing their lifespan and performance. Here are some essential maintenance tips:
- Regular Cleaning: Keep the spindle clean from debris and contaminants. Use a soft brush or cloth to wipe down the exterior and remove any buildup.
- Lubrication: Regularly lubricate bearings and other moving parts according to the manufacturer’s recommendations to ensure smooth operation.
- Check Alignment: Misalignment can cause excessive wear and tear. Regularly check and adjust the spindle’s alignment as needed.
- Monitor Temperature: Keep an eye on the spindle’s temperature during operation. If it gets too hot, investigate potential cooling issues.
- Inspect for Wear: Periodically inspect the spindle for signs of wear, such as unusual noises or vibrations, and replace worn components as necessary.
FAQs About CNC Spindles
1. What is the primary function of a CNC spindle?
The primary function of a CNC spindle is to hold and drive the cutting tool, providing the necessary speed and torque for machining operations.
2. How do I choose the right CNC spindle for my machine?
Consider factors such as the type of machining you will be doing, the materials you will be working with, and the spindle’s speed and power requirements.
3. What maintenance is required for a CNC spindle?
Regular cleaning, lubrication, alignment checks, temperature monitoring, and inspection for wear are essential for maintaining CNC spindles.
4. How often should I replace my CNC spindle?
The lifespan of a CNC spindle can vary based on usage and maintenance, but regular inspections can help determine when it needs replacement.
5. Can I upgrade my CNC spindle for better performance?
Yes, upgrading to a higher quality or different type of spindle can improve machining capabilities, speed, and overall performance.
Conclusion
Understanding CNC spindle is crucial for anyone involved in CNC machining. From their basic functionality to the different types available, knowing how to choose and maintain a spindle can greatly impact your machining success. By keeping your CNC spindle in top condition, you ensure precise, efficient, and high-quality machining operations.
Read More
Empowering Teams with Self-Service Visualization Tools for Data-Driven Decisions
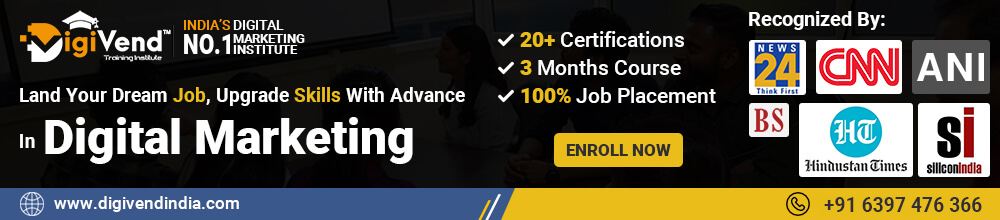