Cleanroom Air Conditioning Systems: Ultimate Guide to Efficiency & Maintenance
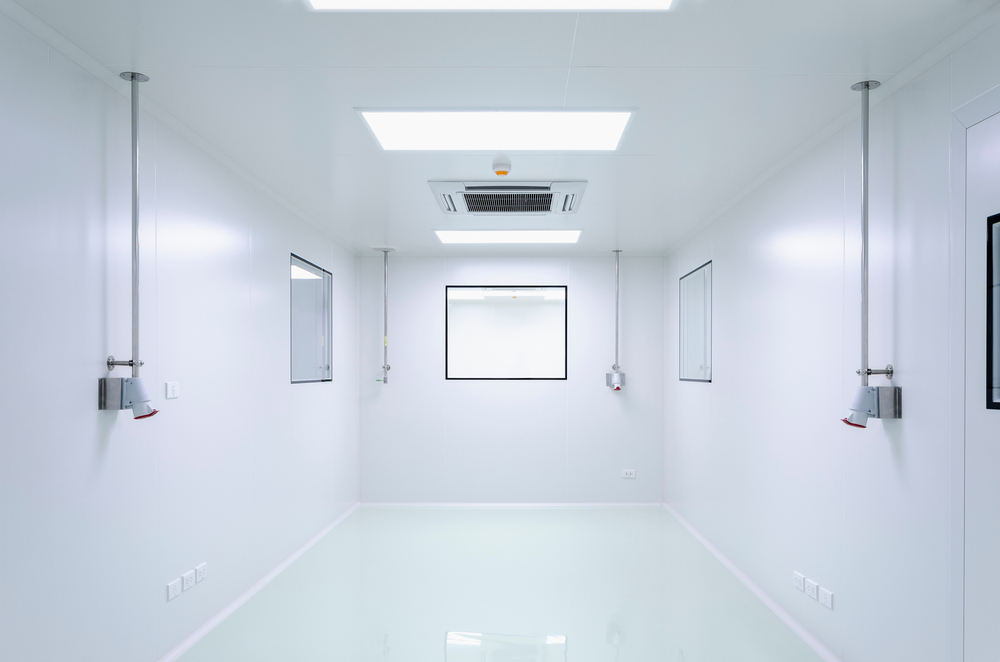
Cleanroom air conditioning systems are engineered marvels that silently uphold the integrity of critical environments. From semiconductor fabrication to vaccine production, these systems ensure air purity, temperature stability, and humidity control with surgical precision. Yet, their complexity demands more than passive oversight—it requires a proactive, knowledge-driven approach to maintenance and optimization.
In this guide, we’ll delve into the technical and operational nuances of cleanroom air conditioning systems, equipping you with actionable strategies to maximize efficiency, ensure compliance, and avoid costly downtime. Whether you manage a pharmaceutical lab, a biotech facility, or an electronics assembly line, this resource will help you transform your system into a pillar of reliability.
The Critical Role of Cleanroom Air Conditioning Systems
Cleanrooms are not mere rooms—they are meticulously controlled ecosystems. Even minor deviations in temperature or airborne particles can derail production, invalidate research, or trigger regulatory penalties. Cleanroom air conditioning systems serve as the first line of defense, combining advanced filtration, climate control, and real-time monitoring to sustain these fragile environments.
Why Efficiency Matters: Beyond Basic Compliance
Efficiency in cleanroom air conditioning systems isn’t just about reducing energy bills—it’s about operational survival. Consider these stakes:
- Product Integrity: A single contaminant in a semiconductor cleanroom can ruin a batch of microchips, costing millions.
- Regulatory Compliance: Facilities must adhere to ISO 14644, EU GMP, or FDA standards, where documentation of system performance is mandatory.
- Cost Management: Energy waste from poorly maintained systems can inflate annual operating costs by 20–30%, eroding profitability.
By prioritizing efficiency, facilities protect their reputation, avoid recalls, and maintain a competitive edge.
Core Components of Cleanroom Air Conditioning Systems
Understanding the anatomy of your system is essential for effective maintenance. Below, we break down the key components and their roles:
- HEPA/ULPA Filtration Systems
- High-Efficiency Particulate Air (HEPA) and Ultra-Low Penetration Air (ULPA) filters are the cornerstone of contamination control.
- HEPA Filters: Capture 99.97% of particles ≥0.3 microns (e.g., dust, microbes).
- ULPA Filters: Trap 99.999% of particles ≥0.12 microns (critical for nanotechnology or optics manufacturing).
- Filter Housing: Must be airtight to prevent bypass leakage, which undermines filtration efficacy.
- Precision Cooling and Humidity Control
- Chilled Water Coils: Regulate temperature by circulating coolant at precise rates.
- Desiccant Wheels: Control humidity in arid climates by absorbing moisture from incoming air.
- Steam Humidifiers: Add moisture in dry environments to maintain ±5% humidity tolerance.
- Airflow Management
- Variable Frequency Drives (VFDs): Adjust fan speeds dynamically to maintain pressure differentials (e.g., +15 Pa in ISO Class 5 cleanrooms).
- Laminar Flow Systems: Direct air in unidirectional streams to minimize particle dispersion.
- Monitoring and Automation
- IoT Sensors: Track real-time data on temperature, humidity, and particle counts.
- Building Management Systems (BMS): Centralize control and automate responses to deviations.
Proactive Maintenance: A Step-by-Step Framework
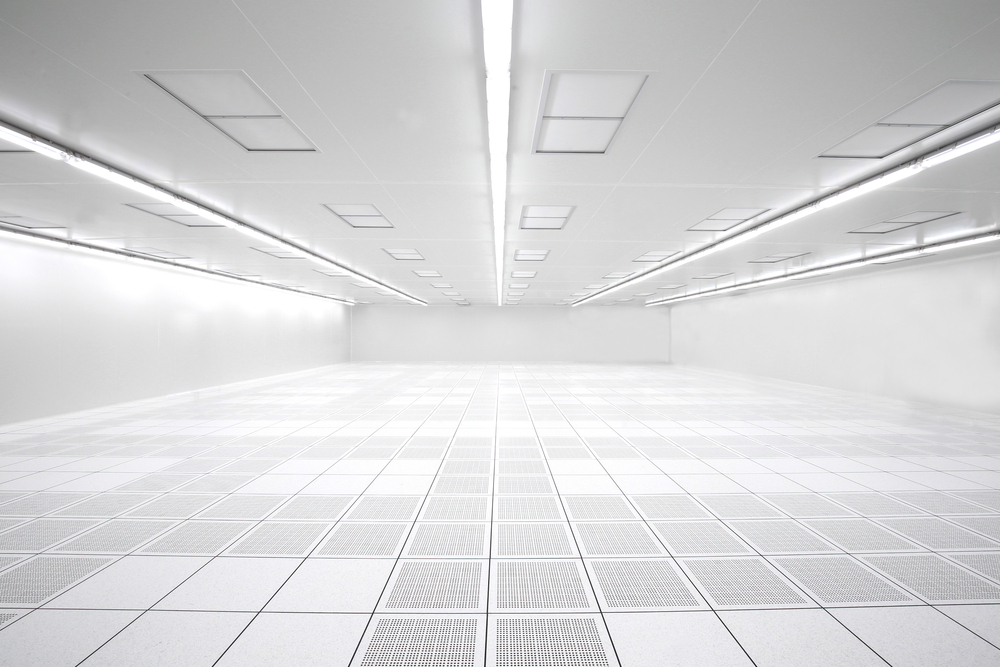
Neglecting maintenance risks catastrophic failures. Follow this structured approach to ensure peak performance:
- Filter Replacement and Integrity Testing
- Frequency: Replace pre-filters every 3 months, HEPA filters annually (or when pressure drop exceeds 50 Pa).
- Testing: Conduct annual DOP (Dispersed Oil Particulate) testing to verify filter integrity.
- Coil and Duct Cleaning
- Coil Degradation: Dirty coils reduce heat exchange efficiency by up to 30%. Clean quarterly with non-corrosive agents.
- Duct Inspection: Use robotic cameras annually to detect microbial growth or debris accumulation.
- Sensor Calibration and System Audits
- Calibration: Recalibrate temperature and humidity sensors every 6 months to prevent drift.
- Third-Party Audits: Schedule bi-annual audits to validate compliance with ISO or industry-specific standards.
- Documentation and Trend Analysis
- Digital Logs: Use CMMS software to track filter changes, energy consumption, and repair histories.
- Predictive Analytics: Analyze data trends to forecast component failures (e.g., fan motor wear).
Troubleshooting Common Issues: Expert Insights
Even robust systems encounter hiccups. Here’s how to diagnose and resolve frequent challenges:
- Inconsistent Temperature or Humidity
- Root Causes: Refrigerant leaks, faulty humidifiers, or sensor miscalibration.
- Fix: For leaks, engage licensed technicians to recharge refrigerant. Recalibrate sensors using NIST-traceable tools.
- Poor Airflow or Pressure Imbalances
- Root Causes: Clogged filters, obstructed ducts, or VFD malfunctions.
- Fix: Replace filters immediately. Inspect ducts for blockages and reset VFD parameters.
- Unusual Noises or Vibrations
- Root Causes: Worn-out fan bearings, loose belts, or imbalanced blower wheels.
- Fix: Lubricate bearings annually and replace belts showing cracks or fraying.
Cost-Effective Upgrades for Sustainable Operations
Modernizing your cleanroom air conditioning systems can yield rapid ROI while future-proofing operations:
- Energy Recovery Ventilators (ERVs): Capture waste heat from exhaust air to pre-condition incoming air, cutting heating costs by 40%.
- Smart Zoning Systems: Divide cleanrooms into zones with independent climate controls, reducing energy waste in unused areas.
- LED Lighting Retrofits: Lower heat emissions from lighting, reducing cooling loads by 10–15%.
- Solar-Powered Cooling: Integrate solar thermal systems to offset electricity demand during peak hours.
Conclusion: Elevating Your Cleanroom’s Performance
Cleanroom air conditioning systems are not static installations—they demand vigilant stewardship. By adopting the strategies outlined here, you’ll transform maintenance from a reactive chore into a strategic advantage. From leveraging IoT for real-time alerts to investing in energy recovery tech, every action you take fortifies your facility against risks while enhancing sustainability.
Remember: The true cost of inefficiency isn’t just financial—it’s the erosion of quality, compliance, and trust. Stay ahead by prioritizing precision, documentation, and innovation.
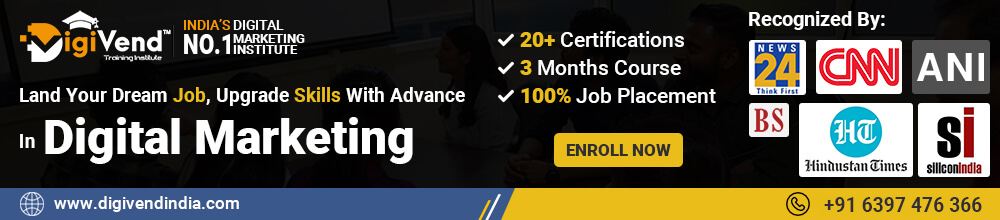