All You Need To Know About Shampoo Manufacturing Cost
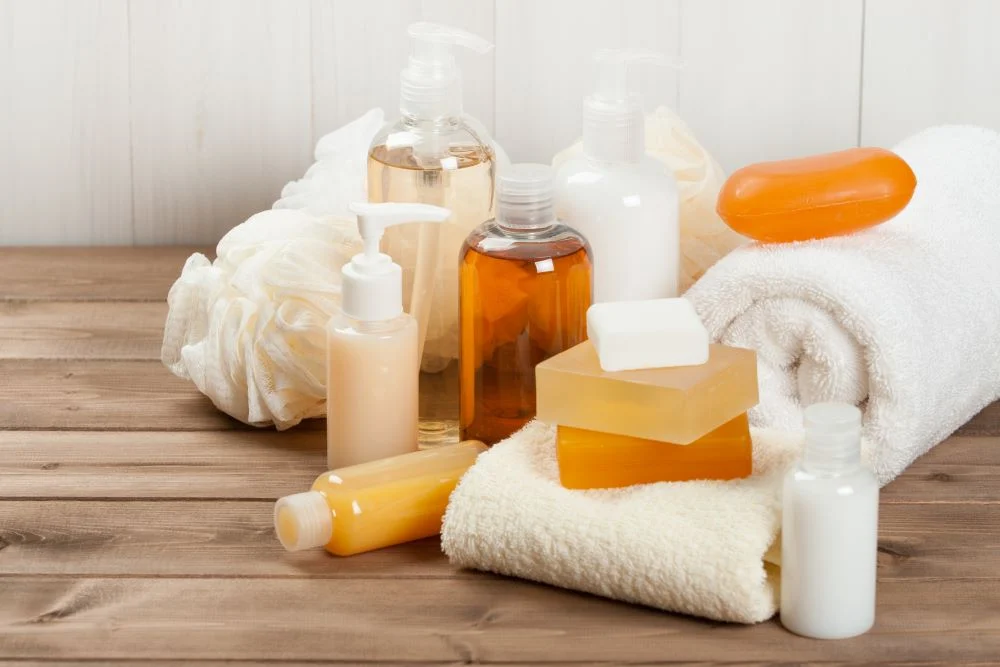
Shampoo is an essential personal care product used by almost everyone on a daily basis. However, not many people are aware of the actual process and costs involved in manufacturing shampoo. In this blog, we will discuss the various aspects of shampoo manufacturing including raw material procurement, formulation, packaging, quality testing and more. By the end, you will have a clear understanding of the shampoo manufacturing cost process and the associated costs. Let’s get started.
-
Raw material procurement
Shampoo manufacturing starts with procuring the right raw materials. The main raw materials required are surfactants, conditioning agents, thickeners, preservatives, fragrances, dyes and water. Surfactants like sodium lauryl sulfate and sodium laureth sulfate form the base of any shampoo. Conditioning agents like silicones provide nourishment. Thickeners provide the right viscosity. Preservatives prevent microbial growth. Fragrances and dyes provide the desired smell as well as color. Water is the main solvent used. Procuring high quality raw materials from reliable suppliers is important to maintain consistency in quality. It also contributes significantly to the total manufacturing cost.
-
Formulation development
Once the raw materials are procured, an appropriate formulation is developed based on the desired functionality of the shampoo. The R&D team experiments with different concentrations and combinations of raw materials to achieve the right cleansing, conditioning, foaming and viscosity properties. Multiple trials are conducted to finalize the most effective and stable formulation. This formulation development process requires specialized equipment, experienced scientists and several rounds of testing. It contributes around 10-15% to the total manufacturing cost.
-
Packaging material selection
After the formulation is ready, appropriate packaging materials are selected based on the target consumer segment. For mass market products, HDPE bottles are commonly used. For premium products, PET bottles or plastic-glass bottles find more use. The packaging type also depends on the desired volume of the product – 50ml, 100ml, 250ml, etc. Other factors like shelf-life, safety, visual appeal, costs also guide the packaging decision. The packaging materials themselves contribute around 15-20% to the total cost of manufacturing.
-
Bottling/filling and sealing operations
Once the packaging materials are selected, the next step is filling the formulation into the packaging containers using automated filling machines. These machines fill an accurate volume of the shampoo into each bottle at high speeds. The filled bottles then go through capping/sealing using crowning machines. Special care is taken to avoid any spillage or contamination during these processes. Bottling lines require huge capital investments and account for 10-15% of the total manufacturing cost. Proper maintenance and operation of such machinery is also critical.
-
Quality testing
No shampoo manufacturing companies process is complete without rigorous quality testing at various stages – right from raw materials to the finished products. Tests are conducted to check parameters like pH balance, viscosity, microbial contamination, stability over time, etc. Samples from each batch also undergo sensory evaluation. Regulatory standards and specifications laid down by various certification bodies are strictly followed. Sophisticated analytical equipment and trained personnel are required for quality control. This adds another 5-7% to the total cost. Only cleared batches are released for packaging and distribution.
-
Secondary packaging
The primary packaged products then undergo secondary packaging depending on how they will be shipped. For retail, multipacks of 6 or 10 bottles are bundled together and packed in corrugated boxes. For industrial use, 20-25 kg bags or barrels are used. Tertiary packaging like pallets is also used. This protects the products during transportation and storage. The packaging materials, labor and machinery required for secondary packaging contribute around 3-5% to the total cost. Proper packaging is essential to avoid damage during shipping.
-
Storage and inventory management
Adequate storage space is required to stock the finished products until they are dispatched. Environmental conditions like temperature and humidity are controlled in the warehouses. Inventory levels are closely monitored using ERP systems to ensure just-in-time delivery. Excessive storage leads to increased carrying costs of inventory. Sales might decline as a result of low inventory.Effective inventory management is thus important from a cost perspective. It accounts for around 2-3% of the total manufacturing cost.
-
Transportation and logistics
Once the production is completed, the finished products need to be transported from the manufacturing facility to distribution centers, retailers or direct customers depending on the supply chain model. This involves careful planning and coordination of transportation modes – road, rail or sea. Selection of logistics partners, route optimization, load planning, etc are important factors. Transportation and logistics can contribute 5-7% to the total cost depending on the destination and volumes handled. Efficient logistics management is thus crucial.
-
Marketing and sales promotion
While the above costs are related to production, the marketing and promotion costs are also substantial. These include expenses incurred on advertising, sales team salaries, discounts, retail promotions, samples, etc. In the highly competitive personal care market, regular new campaigns and offers are a must to sustain sales volumes. Marketing can account for as high as 15-20% of the total cost depending on the scale of operations and promotional intensity in a particular period. Careful planning of budgets is required.
-
Regulatory compliances
Strict compliance with various quality and safety regulations is a must in the cosmetics industry. This involves costs related to obtaining various certifications, periodic audits, product approvals and license renewals. Adhering to environmental standards during manufacturing also leads to additional infrastructure investments. Compliance with different regulatory bodies across countries adds further complexity. On an average, regulatory related costs are around 2-5% of the total cost. Non-compliance can attract heavy penalties and loss of reputation.
Conclusion
As seen above, shampoo manufacturing is a complex process involving multiple stages from raw material procurement to distribution. While formulation and packaging costs are major contributors, other aspects like quality control, logistics, marketing and regulatory compliances also demand substantial investments. By understanding the cost breakup, entrepreneurs can make informed decisions regarding capacity, pricing and focus areas for cost optimization like Aura Herbal. With efficient management of each stage, overall costs can be controlled to some extent.
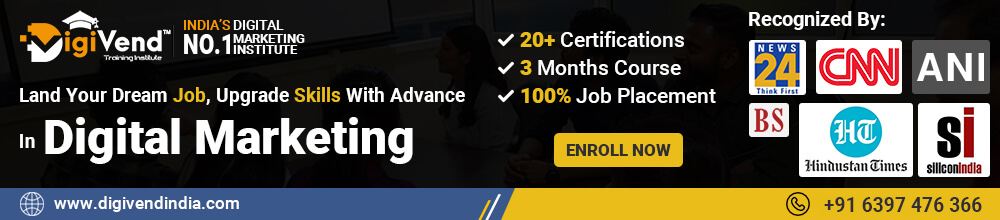