Accurate Level Indicators for Precise Liquid & Tank Monitoring
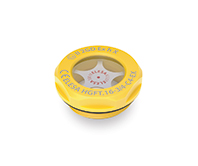
A level indicator is an essential device used to measure and monitor the liquid levels in tanks, reservoirs, and industrial containers. These instruments play a crucial role in ensuring operational efficiency, preventing overflow, and maintaining optimal liquid levels in various industries such as oil and gas, chemical processing, food and beverage, and water treatment plants.
Importance of a Level Indicator
A level indicator provides real-time data on liquid levels, helping industries maintain safety and efficiency. Some key benefits include:
- Prevention of Overflows and Spills: Avoids unnecessary wastage and environmental hazards.
- Improved Process Control: Ensures accurate measurement for consistent production quality.
- Enhanced Safety: Reduces the risk of accidents caused by incorrect fluid levels.
- Cost Savings: Helps manage raw materials efficiently, minimizing waste.
Types of Level Indicators
There are various types of level indicator devices, each designed for specific applications and environments:
1. Float Type Level Indicator
- Uses a floating mechanism to measure liquid levels.
- Commonly used in water tanks, fuel storage, and industrial reservoirs.
2. Magnetic Level Indicator
- Works with a magnetized float that rises and falls with the liquid level.
- Ideal for high-pressure and hazardous environments.
3. Ultrasonic Level Indicator
- Uses ultrasonic waves to detect liquid levels without direct contact.
- Suitable for applications requiring non-invasive measurement.
4. Radar Level Indicator
- Uses radar technology to determine liquid levels with high accuracy.
- Best for challenging environments, including corrosive and high-temperature liquids.
5. Capacitive Level Indicator
- Measures level changes based on variations in electrical capacitance.
- Commonly used for measuring bulk solids and non-conductive liquids.
6. Transparent Level Indicator
- Consists of a transparent glass tube to provide direct visual monitoring.
- Suitable for applications that require real-time manual inspection.
Industries That Use Level Indicators
A level indicator is widely used across multiple industries to ensure efficiency and safety in liquid management. Some key sectors include:
- Oil and Gas Industry: Monitors fuel and chemical storage levels.
- Water Treatment Plants: Helps manage water levels in reservoirs and filtration systems.
- Pharmaceutical Industry: Ensures accurate liquid measurement in drug production.
- Food and Beverage Industry: Assists in maintaining proper ingredient levels.
- Power Generation Plants: Monitors coolant and lubricant levels in machinery.
How to Choose the Right Level Indicator
When selecting a level indicator, consider the following factors to ensure optimal performance:
1. Type of Liquid
- Identify whether the liquid is corrosive, viscous, or non-conductive.
- Choose a material compatible with the liquid being measured.
2. Operating Environment
- Consider temperature, pressure, and hazardous conditions.
- Select a level indicator that can withstand extreme environments.
3. Measurement Accuracy
- Determine the required precision for the application.
- Some industries need highly accurate level readings for regulatory compliance.
4. Installation and Maintenance
- Choose an indicator that is easy to install and maintain.
- Non-contact indicators (ultrasonic and radar) require minimal maintenance.
5. Cost and Budget
- Compare different models to find a cost-effective solution.
- Balance affordability with durability and accuracy.
Installation and Maintenance Tips
Proper installation and maintenance of a level indicator are crucial for ensuring long-term accuracy and reliability. Follow these tips to maximize performance:
- Follow Manufacturer Guidelines: Always adhere to the recommended installation procedures.
- Regular Calibration: Periodically calibrate the level indicator to maintain accuracy.
- Check for Blockages: Ensure that floats, sensors, or probes are free from obstructions.
- Inspect for Wear and Tear: Replace worn-out components to prevent measurement errors.
- Use Protective Coatings: For harsh environments, apply coatings to protect against corrosion.
Top Manufacturers of Level Indicators
Several companies specialize in manufacturing high-quality level indicators, including:
- Emerson – Known for radar and ultrasonic level measurement systems.
- ABB – Offers advanced level monitoring solutions for industrial applications.
- Siemens – Specializes in innovative radar and capacitive level indicators.
- Honeywell – Provides reliable float and magnetic level indicators.
- VEGA – Experts in non-contact level measurement technologies.
Conclusion
A level indicator is an essential tool for monitoring liquid levels across various industries. Choosing the right level indicator depends on factors such as the type of liquid, operating conditions, and required accuracy. Regular maintenance and calibration ensure long-term reliability and efficiency. By investing in a high-quality and level indicator, businesses can enhance safety, reduce waste, and improve operational performance.
As technology advances, modern level indicators are becoming more precise, durable, and automated, integrating IoT and AI for real-time monitoring and predictive maintenance. Industries benefit from enhanced safety, efficiency, and cost savings. Investing in the right level indicator ensures seamless operations, regulatory compliance, and long-term sustainability in liquid management systems.
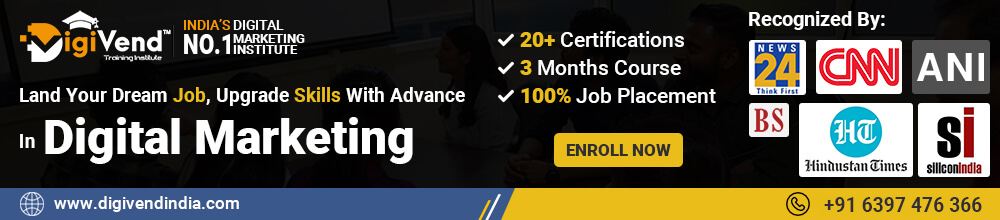