About Reliable Rubber Extrusions And Inflatable Seals Manufacturers

Introduction:
Dynamical sealing solutions such as inflatable seals are intended to cover gaps and irregularities and offer a dependable barrier among surfaces by expanding. When compressed with air or other gases, inflatable seals, in contrast to conventional static seals, can alter their shape to fit a variety of measurements. Their exceptional quality renders them invaluable in situations where reliable, flexible sealing is needed under changing circumstances.
These seals are made of elastomers, such as silicone, EPDM (ethylene propylene diene monomer), and neoprene, or flexible materials like rubber. The criteria of the application, which take into account things like durability, chemical compatibility, and temperature tolerance, determine the material to be used. To increase strength and durability and make sure the seals work well even in harsh environments, reinforcement in the shape of textiles or other materials can be applied.
Inflatable seals are extensively utilized in many different sectors. In the aerospace industry, they keep doors and access hatches on airplanes airtight to guarantee efficiency and safety at high altitudes. They are used by the car industry to reduce noise and offer comfort by sealing doors and sunroofs. These seals provide ship doors and bulkheads with watertight protection in marine conditions, which is essential for preserving buoyancy and preventing water infiltration. Furthermore, by preventing contamination in cleanrooms and processing equipment, inflatable seals help the pharmaceutical and food processing sectors maintain strict hygiene standards.
Inflatable seals are perfect for complex and dynamic sealing applications because they can maintain a tight seal while allowing for movement and fluctuating pressures. These seals continue to develop, providing improved performance and broadening their variety of applications in contemporary industrial and commercial contexts, thanks to continuous developments in materials and production procedures.
Inflatable Seals Manufacturer
Selection of Materials and Manufacturing Procedures
Inflatable seal production is mostly dependent on the minute details of the manufacturing process and the selection of appropriate materials. Specialized materials that can resist severe chemicals or extreme temperatures, such Viton or fluorosilicone, may be needed for certain applications.
These elastomers are commonly molding or extruded into predetermined profiles to start the manufacturing process. While moulding requires forming the material into discrete components, extrusion entails pushing the elastomer through a die to produce continuous lengths of material with a constant cross-sectional shape. To guarantee that the finished product satisfies design requirements, both approaches demand exact control. Often strengthened with fabric or other materials, these seals increase in flexibility and durability.
Design and Customizing
One important service offered by producers of inflatable seals is customization. In order to create seals that meet particular shapes and functions, manufacturers collaborate closely with clients to understand the specific requirements of various applications. Seals with particular inflation mechanisms and pressure ratings, as well as those with irregular, circular, or rectangular geometries, may fall under this category.
From the first stages of design until the end of manufacturing, engineers work with clients, modelling and testing prototypes with the use of computer-aided design (CAD) tools and simulation software. Through this iterative approach, the seals are guaranteed to meet performance and dimensional criteria as well as to interact seamlessly with the client’s systems. Choosing the best material grade may also be a part of customization, taking into consideration things like mechanical loads, operational temperatures, and chemical exposure.
Compliance & Quality
For manufacturers of inflatable seals, quality control is crucial since the dependability of these seals affects performance and safety in crucial applications. To make sure seals meet or surpass industry standards, manufacturers follow strict testing procedures, including as fatigue, environmental, and pressure testing. One of their quality assurance processes’ main goals is frequently to ensure compliance with appropriate standards, FDA regulations, and certifications like ISO 9001.
Technological Innovations
The industry is known for its constant innovation, as manufacturers spend money on R&D to improve the performance and flexibility of inflatable seals. More effective hard seals are driven by advances in materials science, such as the development of new elastomers with improved properties, and improvements in manufacturing processes such as touchscreens about the self and makes it possible.
Services & Support for Customers
Leading manufacturers provide a range of support services in addition to creating high-quality seals to guarantee customer satisfaction and maximum seal performance. This comprises:
- Consultation Services: To help clients choose the right seal for their application.
- Installation Guidance: Providing instructions and support for proper seal installation.
- Maintenance and Repair Services: Offering solutions for maintaining seal integrity and extending service life.
- Technical Documentation: Supplying detailed specifications, installation guides, and maintenance manuals.
Application and Industry Focus
Many industries rely on manufacturers, including food processing, automobiles, maritime, aviation, and medicines. Because they stop air from leaking into doors & door seals, inflatable seals are crucial in aircraft. They also provide reliable window and door seals in automobile applications. These seals are essential to the food and pharmaceutical industries for controlled environments and watertight compartment maintenance, as well as to the marine industry for preventing contamination.
Conclusion:
Rubber extrusions are essential parts of many commercial and industrial applications because they offer a variety of options for structural support, insulation, and sealing. Produced with the application of pressure on a shaped die, these extrusions yield continuous profiles with regular cross-sectional shapes, including tubes, strips, and intricate geometries.
Rubber extrusions are primarily advantageous due of their versatility. Their ability to be tailored to particular dimensional and performance specifications enables them to be used for a multitude of applications, such as protective edging, weatherstripping, gaskets, and seals. Commonly utilized materials include silicone, EPDM, neoprene, and rubber; these materials were selected for their resistance to mechanical wear, UV radiation, temperature extremes, and chemicals.
Rubber extrusions are crucial in various industries like electronics, construction, automotive, and aerospace for creating tough, flexible parts that extend life, improve structural performance, and enhance structural integrity and energy efficiency.
Rubber extrusions can now be used to create more complicated profiles and improve their performance attributes thanks to developments in material science and extrusion technology. All things considered, rubber extrusions are essential to contemporary engineering and production since they provide dependable solutions that satisfy the strict requirements of a wide range of sectors and applications.
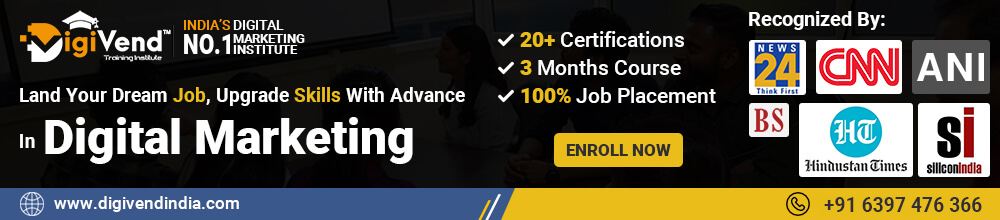