A Complete Guide to Valve Materials: From Stainless Steel to Super Alloys
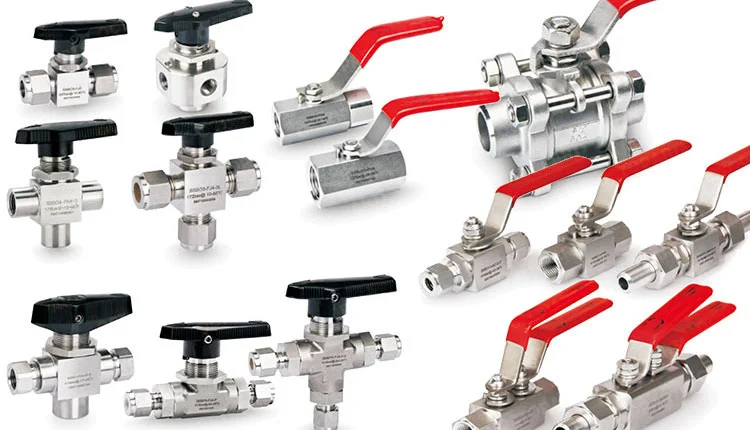
Valves are indispensable components in industrial systems, responsible for regulating the flow of liquids, gases, and steam under various conditions. The material used in valve construction plays a critical role in determining performance, durability, and suitability for specific environments. From versatile stainless steel to advanced super alloys, each material offers unique benefits tailored to specific applications. This guide explores key valve materials, their properties, and where they are most effectively used.
1. Stainless Steel Valves
Stainless steel is one of the most widely used materials for valve manufacturing due to its exceptional resistance to corrosion, oxidation, and high-temperature environments. Stainless steel valves, particularly stainless steel ball valves suppliers, are preferred for their reliability and long service life in demanding applications.
Key Features:
- Excellent corrosion resistance, even in aggressive environments
- Strong mechanical properties and durability
- Resistant to high temperatures and pressures
Common Grades:
- 304 Stainless Steel: General-purpose use, offering good corrosion resistance
- 316 Stainless Steel: Enhanced corrosion resistance, ideal for marine and chemical applications
Applications:
- Food and beverage processing
- Water and wastewater treatment
- Petrochemical and oil & gas industries
Stainless steel valves are versatile and widely used across industries due to their longevity and ability to handle both high-pressure and high-temperature conditions. These qualities make them a cost-effective option in the long run for industries looking for reliability and performance.
2. Carbon Steel Valves
Carbon steel is known for its strength, affordability, and ability to withstand high pressures. While less resistant to corrosion compared to stainless steel, carbon steel valves are widely used in non-corrosive environments.
Key Features:
- High tensile strength and toughness
- Cost-effective for high-pressure systems
- Limited corrosion resistance
Applications:
- Steam and high-temperature systems
- Oil and gas pipelines
- Industrial water and air systems
The primary advantage of carbon steel valves is their cost-efficiency in heavy-duty applications. These valves are ideal for systems where the flow media does not contain highly corrosive substances, allowing industries to save on material costs while maintaining performance.
3. Cast Iron and Ductile Iron Valves
Cast iron and ductile iron are traditional materials commonly used for valves in low-pressure systems. Ductile iron offers enhanced flexibility and impact resistance compared to cast iron.
Key Features:
- Cost-effective for large-scale systems
- Excellent wear resistance
- Suitable for low to moderate pressures
Applications:
- Municipal water supply systems
- HVAC (Heating, Ventilation, and Air Conditioning)
- Low-pressure steam and gas systems
Ductile iron valves, with their high tensile strength and flexibility, offer an economical solution for water distribution and HVAC systems. They combine durability and affordability, making them a preferred choice for non-extreme operating conditions.
4. Bronze and Brass Valves
Bronze and brass valves are well-suited for applications requiring corrosion resistance in environments such as potable water systems and marine operations. Bronze valves are particularly effective in saltwater environments.
Key Features:
- Superior machinability and corrosion resistance
- Ideal for low-pressure and moderate-temperature applications
- Resistant to saltwater corrosion (bronze)
Applications:
- Plumbing systems
- Marine and offshore applications
- Heating and cooling systems
Bronze and brass valves are particularly popular in plumbing and HVAC systems where moderate temperatures and pressures are involved. Their anti-corrosive properties make them invaluable in marine environments.
5. Alloy Steel Valves
Alloy steel is specifically designed to handle extreme pressures, temperatures, and mechanical stresses. By adding elements like chromium, molybdenum, and nickel, alloy steel valves achieve superior performance in harsh environments.
Key Features:
- High mechanical strength and wear resistance
- Withstands extreme temperatures and pressures
- Suitable for demanding industrial applications
Applications:
- Power generation plants
- Oil refineries and petrochemical processing
- High-temperature steam systems
Alloy steel valves offer a balance between cost and durability for demanding applications. Their ability to resist wear and extreme operating conditions makes them critical in power plants and refineries.
6. Super Alloy Valves
Super alloys are advanced materials designed for the most extreme industrial applications, where high performance, strength, and resistance to corrosion are critical. These include Inconel, Hastelloy, and Monel alloys.
Common Super Alloys:
- Inconel: Excellent high-temperature and high-pressure resistance
- Hastelloy: Superior corrosion resistance in chemical and acidic environments
- Monel: Exceptional resistance to saltwater and marine conditions
Key Features:
- Outstanding strength and performance in harsh environments
- Exceptional corrosion, oxidation, and wear resistance
- Long service life with minimal maintenance
Applications:
- Aerospace and power generation systems
- Chemical processing and refineries
- Marine and offshore operations
Super alloy valves represent the pinnacle of performance and reliability. Industries dealing with aggressive chemicals, high-pressure steam, and corrosive seawater environments depend on these materials to maintain operational efficiency.
How to Choose the Right Valve Material
Selecting the right valve material involves understanding the specific demands of your application. Key factors to consider include:
- Operating Conditions: Assess temperature, pressure, and media type (liquid, gas, steam, etc.)
- Corrosion Resistance: Determine the presence of corrosive agents such as chemicals or seawater
- Mechanical Strength: Ensure the material can handle the stress and flow conditions
- Cost and Maintenance: Balance material cost with long-term durability and maintenance requirements
For instance, stainless steel valves offer excellent performance in diverse conditions but may be overkill for low-pressure water systems where cast iron or brass would suffice. On the other hand, super alloys are essential for systems operating in extreme temperatures or aggressive chemical environments.
Conclusion
From stainless steel valves for their versatility to super alloy valves for extreme conditions, selecting the appropriate valve material ensures optimal performance, safety, and durability. Industries such as oil and gas, chemical processing, water treatment, and marine operations benefit significantly from understanding the properties of these materials.
For premium-quality valves, including stainless steel ball valves and super alloy solutions, partnering with trusted suppliers guarantees reliability and adherence to industry standards. Make informed decisions to enhance system efficiency and longevity.
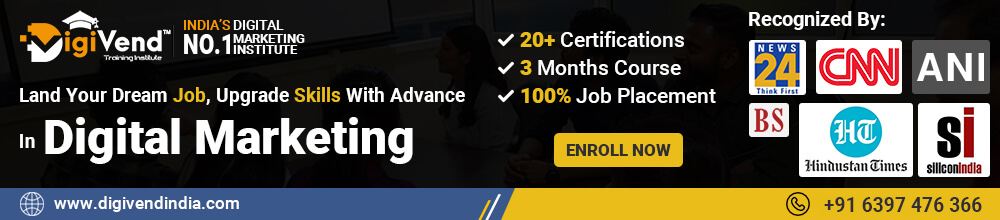