Hardware-in-the-Loop (HIL) Simulation: A Key Tool for Testing and Validation
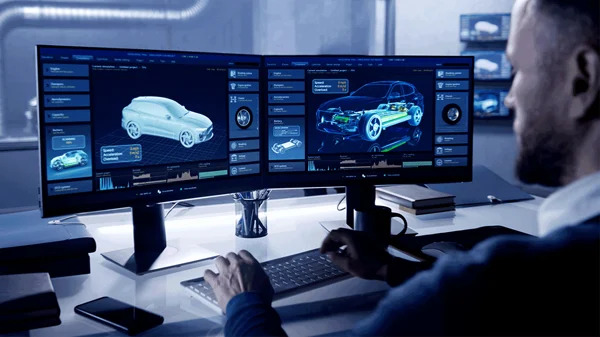
In the world of embedded systems, automotive technologies, and robotics, testing and validation play a crucial role in ensuring that products perform safely, efficiently, and as intended. Traditional testing methods can often be slow, costly, and limited in scope. This is where Hardware-in-the-Loop (HIL) simulation comes into play as a revolutionary approach to streamlining the development process.
In this blog, we will explore what HIL simulation is, how it works, and why it has become an essential tool for engineers across various industries, including the rapidly growing field of autonomous vehicles.
What is Hardware-in-the-Loop (HIL) Simulation?
Hardware-in-the-loop (HIL) simulation is an advanced testing method that combines real hardware with simulation software to test and validate embedded systems. Unlike traditional testing, where only the software or the hardware is tested independently, HIL simulation integrates both to provide a more accurate, real-world environment for testing.
In simple terms, HIL simulation involves connecting physical hardware (e.g., sensors, controllers, actuators) to a virtual environment that simulates the rest of the system. This hybrid setup allows engineers to test how the hardware interacts with the software in a controlled setting without needing to build and deploy the full system in real-world conditions.
How Does HIL Simulation Work?
HIL simulation typically involves three key components:
- Real-Time Simulation Software: This is the heart of the simulation, providing the virtual model of the system. The software simulates the dynamics of the system being tested, such as the vehicle, robotic system, or any other embedded system. It simulates inputs, outputs, and environmental factors that the hardware would experience in the real world.
- Physical Hardware: The hardware being tested is integrated into the simulation loop. This could be a controller, ECU (Electronic Control Unit), sensor, or actuator that is part of a larger system. The hardware interacts with the simulation software in real-time, providing feedback and receiving inputs, just as it would in the final product.
- Interface Systems: These are the links that allow communication between the real hardware and the simulation software. Interfaces such as I/O modules and communication protocols ensure that data flows seamlessly between the hardware and the virtual system, enabling synchronisation and real-time testing.
Benefits of HIL Simulation
- Cost-Effective Testing
Testing hardware in a real-world environment can be expensive and time-consuming. HIL simulation offers a cost-effective alternative by allowing engineers to test systems before physical prototypes are built. This early testing can help identify design flaws and optimize the hardware-software integration without incurring high costs. - Faster Time-to-Market
By running HIL simulations during the development process, engineers can quickly evaluate different configurations, test system behaviours under various scenarios, and validate performance. This accelerates the development cycle and allows products to reach the market faster. - Improved Accuracy and Reliability
HIL simulation provides a more accurate testing environment than traditional methods because it simulates real-world conditions in real-time. Engineers can test how the hardware responds to environmental factors, sensor inputs, or other systems in a safe, controlled environment. This results in higher reliability and fewer surprises during final deployment. - Real-Time Feedback
With HIL simulation, engineers can obtain immediate feedback on how the hardware performs in different scenarios. This enables faster iteration cycles and more effective troubleshooting, as issues can be identified and resolved early in the development process. - Risk Mitigation
Testing complex systems such as autonomous vehicles, industrial robots, and aviation systems using HIL simulation allows engineers to evaluate their performance in scenarios that may be dangerous or difficult to reproduce in the real world. By simulating extreme conditions or edge cases, engineers can mitigate risks before deploying the system in real-life environments.
HIL in Autonomous Vehicles
One of the most transformative applications of HIL simulation is in the development and testing of autonomous vehicles. HIL simulation provides a controlled environment for testing the interactions between the vehicle’s hardware and its software systems, including sensors, control units, and algorithms.
When testing autonomous driving systems, HIL testing allows engineers to simulate real-world driving conditions, such as traffic, road hazards, and sensor inputs, without having to conduct expensive and potentially dangerous physical tests. This is especially important for ensuring the safety and reliability of self-driving cars, as any failure or flaw in the system could lead to catastrophic results. With HIL in autonomous vehicles, engineers can test the hardware (like cameras, LiDAR, and radar) and software (such as navigation algorithms) together, ensuring the vehicle reacts properly in every possible scenario.
HIL Testing in Automotive
The automotive industry is one of the primary sectors benefiting from HIL testing. HIL testing in automotive has become essential for the development of Electronic Control Units (ECUs), powertrains, safety systems, and autonomous vehicle technologies. In particular, automakers use HIL simulation to validate how new ECUs and control systems will perform under various operating conditions.
Whether it’s testing advanced driver assistance systems (ADAS), electric vehicle (EV) powertrains, or safety features like airbags and ABS, HIL simulation helps engineers ensure that all components of the vehicle interact seamlessly. This method reduces the need for expensive physical testing, cuts down on the development timeline, and ensures the car’s reliability and safety before it hits the road.
HIL and MIL Testing: Complementary Approaches
While HIL testing is widely used to test hardware in a simulated environment, Model-in-the-Loop (MIL) testing is another important technique used earlier in the development process. MIL testing involves simulating the software or control algorithms with mathematical models, providing valuable insights before physical hardware is even integrated.
The combination of HIL and MIL testing is extremely powerful. MIL testing allows engineers to verify the performance of software models, while HIL testing adds the layer of real hardware, providing a more complete validation process. By using both methods together, engineers can ensure that the system’s software and hardware components work together optimally, reducing the risk of errors and improving overall system performance.
Applications of HIL Simulation
- Automotive Industry
HIL simulation is widely used in the automotive industry, especially for testing ECUs, powertrains, safety systems, and autonomous driving technology. Engineers can simulate various driving conditions, sensor data, and vehicle behaviours to test how the system responds before building prototypes. - Aerospace and Defense
In aerospace, HIL simulation is used to test flight control systems, avionics, and other critical components. The ability to simulate environmental factors like weather, turbulence, or mechanical failure scenarios ensures that the system is robust and reliable in all conditions. - Industrial Automation and Robotics
HIL simulation allows engineers to test industrial machines, robots, and automation systems in a virtual environment. By doing so, they can optimize performance and ensure smooth interactions between hardware components such as sensors, actuators, and controllers. - Renewable Energy
In the renewable energy sector, HIL simulation can test systems like wind turbines, solar power systems, and energy storage units. Engineers can simulate how these systems react to changing environmental conditions, helping to ensure their efficiency and longevity. - Consumer Electronics
HIL simulation is also employed in testing embedded systems in consumer electronics, such as smartphones, home appliances, and IoT devices. By simulating user interactions and environmental factors, engineers can fine-tune device performance and reliability.
The Future of HIL Simulation
As industries continue to evolve and adopt more advanced technologies like artificial intelligence, machine learning, and the Internet of Things (IoT), HIL simulation is expected to become even more integral to the development and testing processes. Innovations in real-time simulation software, faster processors, and enhanced integration techniques will make HIL simulations more accurate, accessible, and efficient than ever.
Moreover, the growing demand for autonomous systems, electric vehicles, and smart cities will further drive the need for rigorous testing and validation through HIL simulation. In the future, engineers will rely on this technology to accelerate the deployment of safer, smarter, and more sustainable systems.
Conclusion
Hardware-in-the-loop (HIL) simulation is a game-changing technology that has transformed the way Suzuki R&D India engineers test and validate automotive systems. By combining real hardware with virtual simulation, HIL testing enables Suzuki R&D India to optimise performance, ensure safety, and reduce development time.
From testing autonomous vehicle technologies to ensuring the reliability of safety-critical systems, HIL in autonomous vehicles, HIL testing in automotive, and HIL and MIL testing have become essential tools for Suzuki R&D India. As the automotive industry continues to evolve, HIL simulation will remain at the forefront of developing smarter, safer, and more sustainable transportation solutions.
If you’re involved in product development or system integration, incorporating HIL simulation into your workflow could be the key to accelerating innovation while ensuring the highest standards of performance and safety.
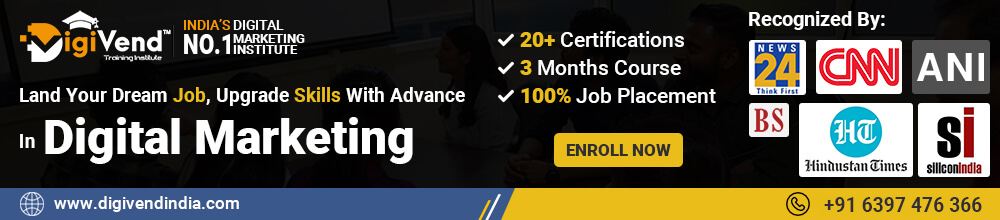