Building Industrial Structures: Key Considerations and Best Practices
The construction of Building Industrial Structures is a critical aspect of modern economies, serving as the backbone for manufacturing, warehousing, and distribution. These facilities must be designed to meet specific operational needs while adhering to safety standards, environmental regulations, and cost-effectiveness. This article delves into the essential considerations and best practices for building industrial structures, focusing on planning, design, materials, and sustainability.
Planning and Site Selection
Understanding Requirements
Before breaking ground, it’s crucial to identify the operational requirements of the facility. This includes understanding the types of machinery that will be used, the volume of materials to be handled, and the necessary workflows. Engaging with stakeholders early in the planning process can help clarify these needs and ensure that the design accommodates them effectively.
Site Selection
Choosing the right location for an industrial structure involves several factors. Accessibility to transportation networks—such as highways, railroads, and ports—is paramount. Proximity to suppliers and customers can also reduce logistics costs and improve efficiency. Additionally, local zoning laws, environmental regulations, and the availability of utilities like water and electricity should be thoroughly investigated.
Design Considerations
Flexibility and Scalability
Industrial operations are often subject to change due to market demands, technology advancements, or shifts in business strategy. Therefore, the design of industrial structures should incorporate flexibility and scalability. Open floor plans, modular construction, and adjustable shelving systems allow for easy reconfiguration of space as needs evolve.
Safety and Compliance
Safety is a top priority in industrial construction. The structure must comply with local building codes and industry standards, such as OSHA regulations in the United States. This includes considerations for fire safety, hazardous materials handling, and employee safety protocols. Features such as proper ventilation, emergency exits, and safety signage are essential to create a secure working environment.
Aesthetic and Branding
While functionality is paramount, the aesthetic appeal of industrial structures should not be overlooked. A well-designed façade can reflect a company’s brand identity and contribute positively to the community. Integrating modern architectural elements, such as natural lighting and green spaces, can enhance the facility’s overall appearance and create a more inviting atmosphere.
Material Selection
Durability and Maintenance
Industrial structures are subject to heavy use and environmental stressors. Therefore, selecting durable materials is crucial to minimize maintenance costs and extend the lifespan of the building. Steel and reinforced concrete are common choices due to their strength and resilience. However, it’s essential to evaluate the long-term performance of materials in the specific conditions they will face, such as exposure to chemicals or extreme weather.
Sustainability
Sustainable construction practices are increasingly important in the industrial sector. Using recycled materials, reducing waste, and incorporating energy-efficient systems can significantly lower the environmental impact of industrial facilities. Features like green roofs, solar panels, and rainwater harvesting systems not only contribute to sustainability but can also result in cost savings over time.
Construction Techniques
Modular Construction
Modular construction involves prefabricating sections of the building off-site and then assembling them on location. This approach can significantly reduce construction time and costs while minimizing waste. Additionally, modular designs often allow for greater precision and quality control, which can lead to better long-term performance.
Lean Construction
Lean construction principles focus on maximizing value while minimizing waste throughout the construction process. This approach emphasizes efficient scheduling, resource management, and continuous improvement. By engaging all stakeholders in the planning and construction phases, teams can identify potential inefficiencies and address them proactively.
Technology Integration
Building Information Modeling (BIM)
BIM technology plays a vital role in the planning and construction of industrial structures. This 3D modeling tool allows architects and engineers to visualize the entire project, identify potential clashes, and optimize designs before construction begins. BIM also facilitates better communication among stakeholders, ensuring that everyone is on the same page.
Automation and Robotics
The integration of automation and robotics into construction processes is transforming how industrial structures are built. Drones can survey sites and monitor progress, while robotic systems can handle repetitive tasks with precision. These technologies enhance efficiency, reduce labor costs, and improve safety on job sites.
Post-Construction Considerations
Facility Management
Once construction is complete, effective facility management becomes crucial to maintaining the building’s functionality and safety. Implementing a comprehensive maintenance plan that includes regular inspections and preventative measures can help extend the life of the structure and reduce unexpected repair costs.
Employee Training and Engagement
The success of an industrial facility is not solely dependent on its design and construction. Employee training and engagement are essential for fostering a culture of safety and productivity. Ensuring that workers understand the layout, safety protocols, and operational procedures can enhance efficiency and reduce the likelihood of accidents.
Conclusion
Building industrial structures requires careful planning, design, and execution to meet the unique needs of modern businesses. By focusing on flexibility, safety, sustainability, and the integration of advanced technologies, companies can create facilities that not only support their operations but also contribute positively to the environment and community. As industries continue to evolve, staying ahead of trends and best practices will be essential for successful industrial construction in the future.
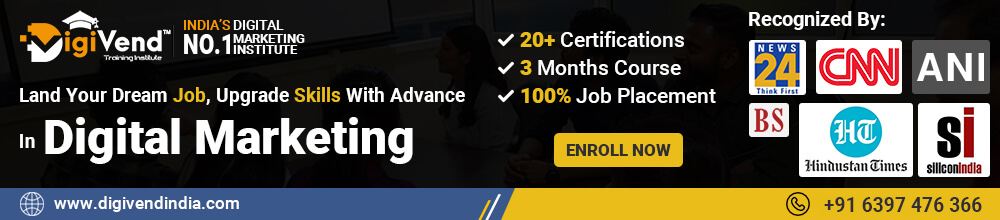