TPM Implementation Roadmap: A Step-by-Step Guide for Indian Manufacturers
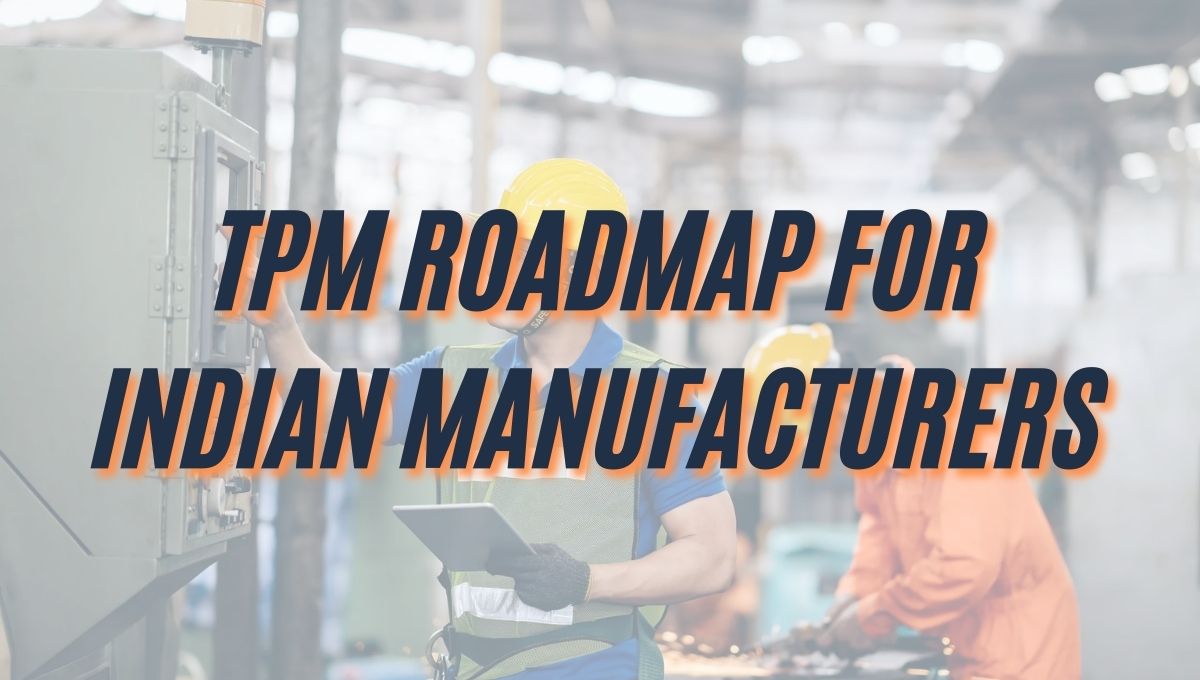
Today, manufacturing companies strive for efficient operations and minimal downtime to stay ahead. Total Productive Maintenance (TPM) is a proven approach that helps achieve these goals by enhancing productivity and equipment reliability. Indian manufacturers are increasingly seeking TPM consultants to assist with the structured adoption of TPM principles. This guide outlines a step-by-step roadmap for implementing TPM, showcasing how Indian manufacturers can improve their operations with the support of expert TPM consultants.
What is Total Productive Maintenance (TPM)?
Total Productive Maintenance is a comprehensive approach aimed at maintaining and improving the integrity of production and quality systems through machine and equipment reliability. Originating from Japan, TPM focuses on maximizing equipment efficiency by involving every employee, from operators to managers, in the maintenance process.
The benefits of TPM include reduced downtime, enhanced productivity, improved safety, and minimized waste. For Indian manufacturers, implementing TPM effectively can lead to significant improvements in operational performance and cost savings.
Why Indian Manufacturers Need TPM Consultants
While the principles of TPM are straightforward, implementing them can be challenging without the right expertise. Here’s why TPM consultants are invaluable for Indian manufacturers:
- Expertise in TPM Tools: TPM consultants have extensive knowledge of TPM pillars, such as Autonomous Maintenance, Planned Maintenance, and Quality Maintenance, which are essential for successful implementation.
- Tailored Implementation: Consultants analyze each company’s unique requirements and provide customized solutions, ensuring that the TPM practices adopted are best suited for specific operational needs.
- Training and Mentorship: TPM implementation requires a shift in culture, with an emphasis on employee involvement. Consultants play a crucial role in training and mentoring teams, promoting a company-wide commitment to TPM.
- Faster Results: With the structured approach provided by TPM consultants, Indian manufacturers can achieve quicker results, reducing downtime and improving productivity efficiently.
The TPM Implementation Roadmap for Indian Manufacturers
Implementing TPM is a gradual process that requires careful planning and consistent effort. Here is a step-by-step roadmap for Indian manufacturers to adopt TPM successfully:
Step 1: Top Management Commitment and Goal Setting
For TPM to succeed, buy-in from top management is essential. TPM consultants in India recommend that senior leaders are not only committed to the concept but actively support its implementation by providing necessary resources.
- Define Goals: Management must outline clear goals for TPM, focusing on areas like reducing downtime, minimizing defects, improving productivity, and enhancing employee engagement.
- Allocate Resources: It is crucial to allocate resources, including financial investment, personnel, and time, to support the TPM journey.
Step 2: TPM Awareness and Training
Creating awareness about TPM and its benefits is the next step. TPM consultants often facilitate initial training sessions to introduce the concept and its principles to employees at all levels.
- Conduct Training Programs: Comprehensive training on TPM concepts, such as the Eight Pillars of TPM, is essential. This training should involve everyone, from machine operators to maintenance personnel and managers.
- Promote a Shared Vision: Employees should understand how TPM aligns with the company’s goals and how it will positively impact their daily work.
Step 3: Establish the TPM Promotion Team
A dedicated team is required to lead and monitor the TPM implementation process. This team is often comprised of personnel from various departments, including maintenance, production, and quality.
- Select Team Members: The team should be made up of individuals who are enthusiastic about TPM and can influence their peers.
- Define Roles and Responsibilities: Each member of the team should have a clear role, whether it’s in maintenance, process improvement, or training others on TPM practices.
Step 4: Conduct Initial Assessments
TPM consultants emphasize the importance of conducting initial assessments to identify existing inefficiencies and areas for improvement. These assessments establish a baseline to measure the effectiveness of TPM implementation.
- Perform Equipment Assessments: Analyze the current state of equipment, focusing on common issues, failure rates, and maintenance history.
- Identify Bottlenecks: Determine which equipment or processes contribute to downtime or impact production quality negatively.
Step 5: Launch the 5S Program
5S is a workplace organization method that sets the foundation for successful TPM implementation by creating an orderly and efficient environment. The 5S steps are Sort, Set in order, Shine, Standardize, and Sustain.
- Sort: Identify and remove unnecessary items from the workspace.
- Set in Order: Organize essential items in accessible and logical locations.
- Shine: Clean the work area to ensure that any equipment issues, such as leaks or misalignments, are noticeable.
- Standardize: Develop standards for maintaining organization and cleanliness.
- Sustain: Promote a culture where 5S practices are followed consistently.
Step 6: Implement the Eight Pillars of TPM

The Eight Pillars of TPM form the core framework for achieving equipment reliability and operational efficiency. Each pillar addresses specific aspects of equipment management and process improvement.
1. Autonomous Maintenance
This pillar involves empowering operators to take responsibility for basic maintenance tasks, such as cleaning, inspection, and lubrication. TPM consultants train operators to conduct routine maintenance, enabling maintenance personnel to focus on more complex tasks.
2. Planned Maintenance
Planned Maintenance focuses on scheduling maintenance activities based on equipment performance and historical data. Consultants assist in setting up maintenance schedules and establishing protocols to ensure timely interventions.
3. Focused Improvement
Also known as Kobetsu Kaizen, this pillar aims at identifying and eliminating specific losses in equipment and processes. Through cross-functional teams, consultants guide improvement projects targeting major productivity issues.
4. Quality Maintenance
Quality Maintenance aims to prevent defects by maintaining ideal equipment conditions. This pillar involves inspecting and monitoring equipment to prevent quality issues before they arise, ensuring that products meet quality standards consistently.
5. Early Equipment Management
Early Equipment Management incorporates TPM principles in the design and installation of new equipment. This approach allows manufacturers to optimize equipment from the start, reducing future maintenance requirements and ensuring efficient operation.
6. Training and Education
TPM consultants emphasize continuous learning, as training is vital to sustain TPM. This pillar involves training employees in TPM methods and developing their technical skills, preparing them to handle equipment maintenance and improvement tasks effectively.
7. Safety, Health, and Environment
Safety is central to TPM, as a safe work environment enhances productivity and morale. The Safety, Health, and Environment pillar focuses on establishing practices that ensure a safe and healthy workplace.
8. TPM in Administration
TPM consultants often advise Indian manufacturers to extend TPM principles beyond the production floor to administrative functions. This pillar helps improve efficiency in areas like procurement, scheduling, and inventory management.
Step 7: Measure, Analyze, and Improve
Regular monitoring and analysis are essential to gauge the success of TPM implementation. Metrics such as Overall Equipment Effectiveness (OEE), Mean Time Between Failures (MTBF), and Mean Time to Repair (MTTR) are commonly used.
- Monitor Key Metrics: Set up dashboards and reports to track performance metrics regularly.
- Analyze Results: Use data to identify trends, recurring issues, and areas for improvement.
- Implement Improvements: Based on insights from analysis, make continuous adjustments to TPM practices to achieve incremental gains.
Step 8: Sustain and Scale TPM Practices
Sustaining TPM is a continuous process that involves reinforcing practices and scaling them across other departments or locations as the company grows.
- Conduct Regular Audits: Schedule routine audits to ensure TPM practices are followed consistently.
- Celebrate Milestones: Recognize achievements and celebrate milestones to keep employees motivated and engaged in TPM efforts.
- Scale to Other Areas: As TPM practices mature, expand their application to other departments, plants, or even new lines of business.
Success Stories: TPM in Action for Indian Manufacturers
Numerous Indian manufacturers across industries have successfully implemented TPM with the help of TPM consultants. Here are some examples:
- Automotive: Indian automotive companies have leveraged TPM to reduce unplanned downtime and improve assembly line efficiency, resulting in higher productivity and cost savings.
- Pharmaceutical: In highly regulated sectors like pharmaceuticals, TPM ensures equipment reliability, compliance, and quality. Companies have reported fewer disruptions, higher yield rates, and improved product quality.
- Textiles: The labor-intensive textile industry has benefited from TPM by reducing machine downtime and empowering operators to handle basic maintenance tasks.
Conclusion
Implementing TPM can significantly enhance productivity, safety, and quality in manufacturing. Indian manufacturers who partner with TPM consultants benefit from structured guidance, customized training, and faster results. By following this step-by-step roadmap, manufacturers can effectively implement TPM, ensuring sustained improvements and a competitive edge in the market.
Elevate Your Manufacturing: Learn How to Implement TPM Effectively! https://www.ribcon.com/resource-center/total-productive-maintenance/
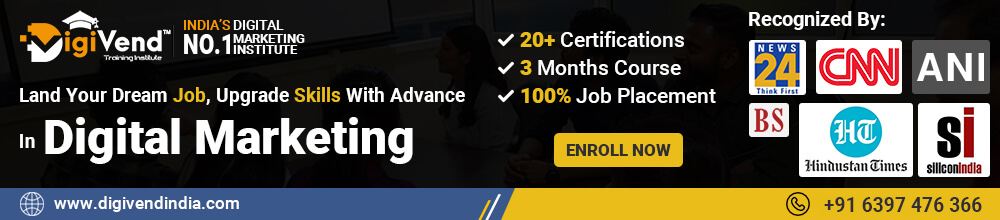