The Importance of Resistance Welding Machine Suppliers in Industrial Manufacturing

Resistance welding is one of the most widely used processes in industrial manufacturing, offering efficient and high-quality solutions for joining metals. Resistance welding machine suppliers play an integral role in ensuring that manufacturers across various industries have access to reliable and advanced welding technologies. From automotive to electronics and aerospace, these suppliers offer equipment that delivers consistent, durable welds while optimizing production efficiency.
What is Resistance Welding?
Resistance welding is a process that involves the application of pressure and passing an electric current through the workpieces to create heat and form a weld. Unlike other forms of welding, such as arc welding, resistance welding does not require filler materials or shielding gas. This makes it a cleaner and more efficient process, particularly for mass production applications.
There are several types of resistance welding, including:
- Spot Welding: One of the most common types, spot welding is used to join two or more metal sheets by applying pressure and electric current to a small area. It is commonly used in the automotive industry for assembling car bodies.
- Seam Welding: This method is similar to spot welding but is used to create continuous, leak-proof welds. Seam welding is often used for producing metal containers, such as fuel tanks and radiators.
- Projection Welding: In this process, the workpiece is designed with projections that concentrate the welding current, allowing for multiple welds to be made simultaneously. This method is used for manufacturing parts like fasteners and brackets.
- Butt Welding: Used for joining two pieces of metal end-to-end, butt welding is ideal for applications like joining wires or rods.
Why Resistance Welding is Crucial for Manufacturing
Resistance welding offers several advantages that make it indispensable in modern manufacturing. These include:
- High Efficiency: Resistance welding is a fast process, making it ideal for high-volume production. It allows manufacturers to produce strong, durable welds in a short amount of time, reducing production costs.
- Clean and Safe: Since resistance welding does not require filler materials or shielding gas, it produces less waste and minimizes the risk of contamination. This makes it a cleaner and more environmentally friendly process.
- Precision and Consistency: Automated resistance welding machines offer precise control over the welding parameters, ensuring consistent results across all welds. This level of precision is crucial in industries like automotive and aerospace, where safety and performance are paramount.
- Minimal Distortion: The localized heat generated during resistance welding minimizes the thermal distortion of the workpiece, resulting in higher-quality welds.
The Role of Resistance Welding Machine Suppliers
Resistance welding machine suppliers are critical partners for manufacturers looking to improve their production processes. Here are some ways in which these suppliers add value:
- Providing Advanced Equipment: Resistance welding machine suppliers offer a wide range of equipment designed to meet the specific needs of different industries. From basic spot welding machines to complex automated systems, suppliers ensure that manufacturers have access to the latest technology.
- Customization and Flexibility: In many industries, standard welding machines may not be sufficient to meet specific production requirements. Suppliers offer customized machines tailored to the unique needs of their clients, whether it’s for specialized materials or complex geometries.
- Technical Support and Training: Resistance welding machines require proper setup and operation to function optimally. Suppliers provide technical support, including training, troubleshooting, and maintenance services, to ensure that manufacturers can use the machines efficiently.
- Innovation and Upgrades: As manufacturing processes continue to evolve, so do welding technologies. Suppliers that prioritize innovation offer machines with advanced features, such as automated controls, real-time monitoring, and data analytics. These features help manufacturers improve efficiency and reduce the risk of defects.
- Sustainability Initiatives: Many suppliers are focusing on developing energy-efficient resistance welding machines that reduce electricity consumption. These machines not only help manufacturers save on energy costs but also support sustainability efforts by minimizing the environmental impact of industrial processes.
How to Choose the Right Resistance Welding Machine Supplier
Choosing the right resistance welding machine supplier is crucial for maximizing the benefits of this welding process. Here are some factors to consider when selecting a supplier:
- Industry Experience: Look for suppliers with a proven track record in providing resistance welding machines to your industry. Suppliers with experience in your specific field are more likely to understand your unique requirements and offer suitable solutions.
- Range of Products: A good supplier should offer a comprehensive range of machines, from manual and semi-automated systems to fully automated solutions. This ensures that you have access to the right machine for your specific application.
- After-Sales Support: Welding machines require regular maintenance and occasional repairs to function at their best. Ensure that the supplier offers reliable after-sales support, including maintenance services, spare parts, and technical assistance.
- Customization Options: If your production process involves unique materials or geometries, choose a supplier that offers customization services. This ensures that the welding machine is tailored to your specific needs.
- Reputation and Reviews: Check customer reviews and testimonials to gauge the reliability of the supplier. Positive feedback from other manufacturers can provide valuable insights into the supplier’s product quality and customer service.
Future Trends in Resistance Welding
The future of resistance welding is set to be shaped by several technological advancements:
- Automation and Robotics: Automated resistance welding systems are becoming more common, especially in industries like automotive and electronics. These systems improve production efficiency, reduce labor costs, and enhance weld quality by minimizing human error.
- Data Analytics: Modern resistance welding machines are equipped with sensors that collect data during the welding process. This data can be analyzed to optimize welding parameters, improve efficiency, and predict maintenance needs.
- Sustainability: With increasing emphasis on reducing the environmental impact of manufacturing, suppliers are focusing on developing energy-efficient welding machines. These machines consume less power and produce fewer emissions, contributing to sustainability goals.
- Advanced Materials: As industries continue to adopt new materials, such as high-strength alloys and composites, resistance welding machines will need to evolve to accommodate these materials. Suppliers are investing in research and development to create machines capable of welding advanced materials without compromising quality.
Conclusion
Resistance welding machine suppliers are vital to the success of industries that rely on efficient, high-quality welding processes. By providing advanced equipment, customization options, and technical support, these suppliers help manufacturers improve their production capabilities while reducing costs and waste. As technology continues to advance, suppliers that prioritize innovation and sustainability will play a crucial role in shaping the future of resistance welding.
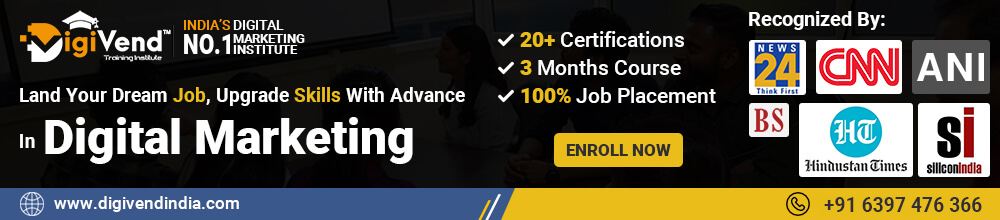