Comparing Rigid-Flex PCBs to Traditional PCBs: Which is Better?
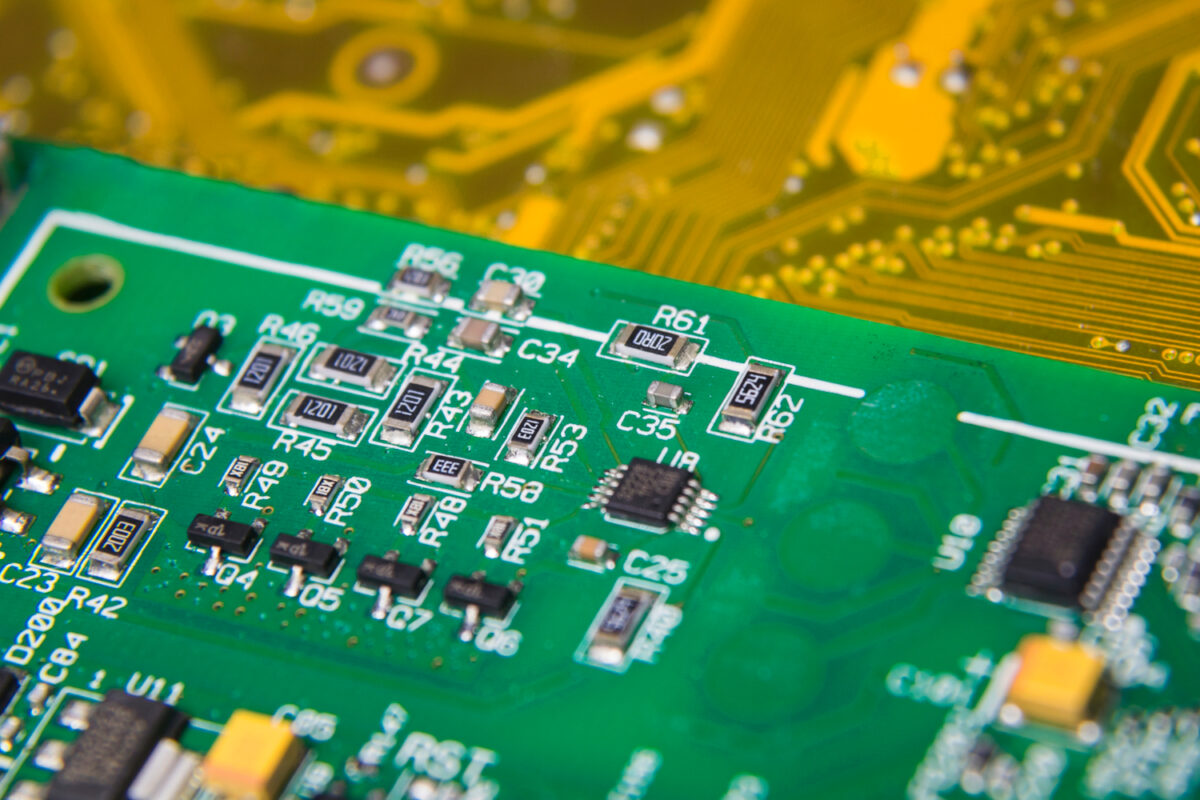
Printed Circuit Boards (PCBs) are integral components of modern electronics. Whether it’s a smartphone, medical device, or industrial equipment, PCBs ensure that electrical signals are transmitted between components reliably. Over the years, traditional rigid PCBs have evolved to meet the needs of an increasingly complex and miniaturized world. However, the rise of rigid-flex PCBs has given designers more flexibility (literally) in their projects. But which is better: rigid-flex or traditional PCBs? This article will explore the key differences, benefits, and drawbacks of each, helping you make an informed choice.
What Are Traditional PCBs?
Traditional PCBs are solid, inflexible boards made from non-conductive substrates such as fiberglass. Layers of conductive copper traces are embedded in these boards, which allow electrical currents to flow between components like capacitors, resistors, and microchips. These PCBs are widely used in various electronic applications, from household appliances to aerospace technologies.
Key Characteristics of Traditional PCBs:
- Rigid Construction: Traditional PCBs have no flexibility and are used where physical stability is essential.
- Layer Options: They can be single-sided, double-sided, or multi-layered, depending on the complexity of the circuit.
- Cost-Effective: Traditional PCBs are less expensive to manufacture compared to rigid-flex counterparts, especially for high-volume production.
- Variety of Sizes and Thicknesses: Available in different sizes and thicknesses, allowing customization for different projects.
However, traditional PCBs are not without limitations. They can take up more space, are prone to cracking under mechanical stress, and lack the adaptability required for complex and compact designs.
What Are Rigid-Flex PCBs?
Rigid-flex PCBs combine elements of both rigid and flexible PCBs. They consist of multiple layers of flexible circuit substrates attached to one or more rigid sections. This allows parts of the circuit to bend while others remain solid. Rigid-flex technology is often used in advanced electronics where space-saving, reliability, and adaptability are essential.
Key Characteristics of Rigid-Flex PCBs:
- Hybrid Construction: Combines the best features of both rigid and flexible PCBs.
- Space-Saving: Flexible sections allow for intricate designs that can fold or bend, making them ideal for devices with limited internal space.
- Durability: Rigid-flex PCBs are highly resistant to vibration and mechanical stress, increasing their longevity, particularly in high-performance and mobile applications.
- Reduced Weight: Due to the elimination of connectors and cables between separate rigid PCBs, rigid-flex PCBs are often lighter and more compact.
While rigid-flex PCBs offer significant advantages in terms of design flexibility and durability, they tend to be more expensive and complex to manufacture compared to traditional PCBs.
Key Differences Between Rigid and Rigid-Flex PCBs
1. Design Flexibility
Rigid PCBs are restricted by their lack of flexibility, limiting their use in compact or movable applications. This is where rigid-flex PCBs shine. The ability to fold, twist, and bend the flexible sections provides engineers with greater design freedom, allowing for the creation of more complex and compact products. For instance, rigid-flex PCBs are often found in wearable devices, smartphones, and aerospace systems where space optimization is critical.
2. Cost
Cost is a significant factor when choosing between rigid and rigid-flex PCBs. Traditional rigid PCBs are generally more cost-effective, particularly for straightforward designs and mass production. In contrast, rigid-flex PCBs are more expensive due to the increased complexity in design, materials, and manufacturing processes. However, the cost might be justified for applications that require higher reliability and space-saving capabilities.
3. Durability and Reliability
Rigid PCBs can be fragile when subjected to mechanical stress or vibrations, which could lead to cracks and eventual circuit failure. Rigid-flex PCBs, however, are designed to withstand such conditions. They are ideal for applications exposed to extreme environments, such as automotive, aerospace, and industrial machinery. The absence of connectors between boards also enhances reliability since these connections are prone to wear and tear over time.
4. Space and Weight Efficiency
In traditional PCBs, multiple rigid boards may be connected using cables, connectors, or solder joints. This not only adds weight but also takes up valuable space. Rigid-flex PCBs eliminate the need for these additional connectors and cabling, enabling lighter and more space-efficient designs. This is why rigid-flex PCBs are often the preferred choice in consumer electronics and portable devices where compactness is paramount.
5. Manufacturing Complexity
Traditional PCBs have a simpler manufacturing process compared to rigid-flex PCBs. The complexity of rigid-flex design requires precise engineering and advanced manufacturing techniques to ensure proper functioning across both rigid and flexible sections. This complexity can lead to longer lead times and higher production costs, making traditional PCBs a better choice for simpler, less demanding projects.
When to Choose Traditional PCBs
Traditional rigid PCBs are ideal in situations where cost is a primary concern, and the product doesn’t require flexibility. If you are designing consumer electronics like desktop computers, kitchen appliances, or simple gadgets, traditional PCBs offer a cost-effective solution. They are also suitable for high-volume production runs due to their ease of manufacturing.
Use Traditional PCBs If:
- The design does not require flexibility.
- Your project has ample space for the PCB.
- You are looking for a cost-effective solution for high-volume production.
- The device will not be exposed to extreme environments or mechanical stress.
When to Choose Rigid-Flex PCBs
Rigid-flex PCBs are the best option for designs that demand high durability, compactness, and the ability to bend or flex. They are especially useful in applications like medical devices, aerospace technologies, and modern smartphones. Although they come with a higher price tag, the performance advantages they offer can outweigh the initial investment, particularly for high-reliability or space-constrained applications.
Use Rigid-Flex PCBs If:
- Your design requires both flexibility and rigidity.
- The device will face mechanical stress or vibrations.
- Space and weight efficiency are critical factors.
- You need enhanced durability and reliability for long-term use.
Conclusion
Both rigid and rigid-flex PCBs have their place in modern electronics. Traditional rigid PCBs are a cost-effective and reliable choice for many consumer and industrial applications. However, when space-saving, durability, and design flexibility are essential, rigid-flex PCBs offer a superior solution despite the higher manufacturing costs. Ultimately, the choice between rigid and rigid-flex PCBs depends on the specific needs of your project, including factors like budget, environmental conditions, and device complexity.
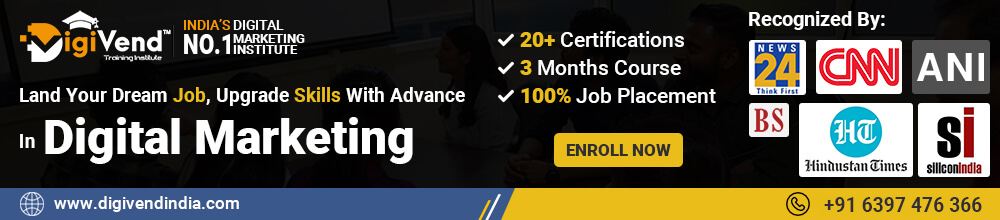