Maximizing Safety and Performance with Control Transformers
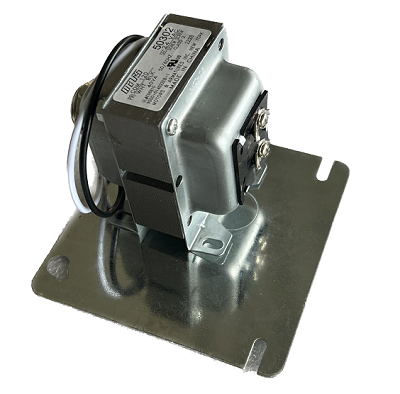
You must pay attention to safety and performance when it comes to electrical systems. Ensuring that your electrical components are performing properly is essential, whether managing an industrial facility, heavy machinery operation, or manufacturing plant. In case you’ve ever wondered how they do it, transformers are among the unsung heroes that keep some of these systems safe and dependable.
However, what precisely are control transformers, and why are they so vital to your electrical systems’ functionality and safety? Let’s investigate more closely.
What Are Control Transformers?
A transformer that provides a steady and sound voltage is central to any efficient electrical network. These special types of transformers deliver a constant voltage output irrespective of the variation in the input power. Such transformers are usually applied in industrial applications, where the control circuit of certain machines requires a steady and stable power supply.
Suppose you are in an organization that is providing services in a factory, and one day, the energy supply is a little irregular. If a control transformer is not used, it may result in equipment failure, delay in production, or worse, life risks may occur. This risk is countered by transformers, which regulate the voltage and also provide a steady supply to the control circuits of the equipment.
Why Safety Matters?
One of the main purposes of a control transformer is to provide safety. Unpredictable power fluctuations in any electrical setup can lead to equipment damage, appliance overheating, and even fire hazards. However, a simple regulation of voltage can help prevent this scenario.
For example, a spot spike in equipment that must operate in known and precise conditions might cause an error in the control circuitry controlling the entire equipment. The use of transformers is not just important for the productivity of the operators, it is also essential for safety. The role that stable power plays in delicate equipment cannot be overstated, and transformers provide just that—security for the equipment and its operators.
Boosting Performance Through Stability
Stability is the key factor, especially in performance areas such as industrial complexes, workshops, and factories, among others. Do you often observe that some machines run slowly or variably? Probably, they are not obtaining the power they require. Voltage-controlling transformers protect machinery and systems from disruptive energy fluctuations, thereby improving efficiency.
From operating automatic machinery, belts, and even assembly line robots, transformers are indispensable as they ensure the continuity of a smooth operation from behind the scenes. The more consistent the power, the better your equipment will serve you in the long run. This is like making sure your car gets a type of fuel that will help it run well—transformers give a proper “fuel” in terms of voltage for your equipment.
How do They work?
How do the transformers strike this balance between performance and safety? It all comes down to how they are built to handle incoming electricity. A control transformer reduces the voltage that is needed by control circuits to make it manageable.
But it’s not just that. They are made to withstand small voltage fluctuations without letting them impact the output voltage since they are engineered with greater control in mind. This ensures that your machines’ control circuits operate effectively even with slight power fluctuations in the main electrical system.
Choosing the Right Control Transformer for Your Needs
Choosing the right control transformer may be overwhelming if you’re new to the electronic industry. However, it’s very useful to know what you need in terms of power requirements and precisely where you would use the transformer. Here are some of the considerations:
- Voltage Requirements: Voltage requirements can vary depending on the control circuit. It is crucial to choose a control transformer that is compatible with your apparatus’s input and output voltage specifications.
- Power Rating: This is a transformer’s capability in terms of the amount of power it can support. It is always best to select a transformer with a sufficient rating to handle the load of your equipment.
- Environmental Considerations: Will the transformer be exposed to extreme temperature, dust, or moisture? Make sure that the transformer you choose is built to meet the conditions it will encounter in service.
Benefits of Transformers
Now that you have a better understanding of transformers, let’s summarize the key benefits:
- Enhanced Safety: Transformers reduce the chances of equipment damage and electrical shocks thereby reducing the dangers associated with working with high voltage currents.
- Improved Performance: A stable power supply also means your machinery will be in optimum condition, thereby reducing breakdowns and keeping your production line going.
- Longer Equipment Lifespan: This means your machinery will not be subjected to lots of sudden breakdowns due to fluctuations in the power and supply, making your equipment last longer.
- Cost Savings: The protection of equipment and improvement of performance means less frequent maintenance problems, less downtime, and fewer repairs on equipment.
Maintaining Your Transformers
Like any other part of your electrical system, transformers should be well-maintained to continue working properly; fortunately, these are not complicated transformers,s and they can help avoid an expensive fix or replacement down the road.
- Visual Inspections: Check your transformers periodically for any visible signs of wear and tear, overheating, or damage. Look for forms of discoloration, unusual noises, or leaks.
- Check Connections: All connections shall be tight and corrosion-free. Connections that are loose or corroded can lead to irregularities in voltage and resultant system failure.
- Monitor the equipment’s performance: If your equipment is not performing as it usually does, do not just ignore it. Maybe these changes are early warnings that mean something is wrong with your control transformer. Do not let a small problem become a big and expensive one.
- Schedule regular servicing: Any electrical system needs regular servicing by a specialist. Scheduled check-ups can identify transformer problems before they turn into critical issues.
Final Thoughts
Control transformers may not be treated as prominent as other components in an electrical system, but their role is crucial. From safety to performance, they are one of the most important factors in optimizing business efficiency. From the factory floor to specialized sectors, transformers are a robust investment in the stability and protection of electrical systems.
So, next time you flip a switch or start a machine, remember that a control transformer is likely working quietly in the background, keeping everything running smoothly and safely.
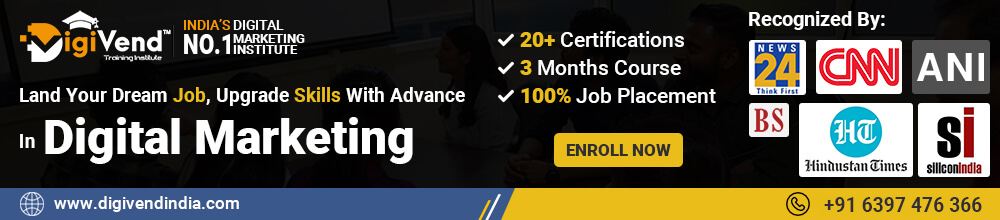