The Advancements in Resistance Welding Technology and Its Impact on Modern Manufacturing

Resistance welding has long been a critical process in various manufacturing industries, offering a reliable and efficient way to join metals. Over the years, advancements in resistance welding technology have significantly improved the precision, speed, and versatility of this process. Taylor-Winfield Technologies, a leader among resistance welding machine manufacturers, has been instrumental in developing state-of-the-art solutions that meet the evolving demands of modern manufacturing. This article explores the advancements in resistance welding technology and their profound impact on the industry.
What is Resistance Welding?
Resistance welding is a process in which two or more metal surfaces are joined together by applying heat and pressure through an electrical current. The heat generated at the contact point between the metals melts them, and the pressure applied helps forge a strong bond as the metals cool and solidify. This process is commonly used in industries such as automotive, aerospace, and electronics due to its ability to produce high-strength welds with minimal material waste.
The key benefit of resistance welding is its efficiency. Unlike traditional welding methods, resistance welding does not require filler materials or consumables, making it a cost-effective option for high-volume production. Additionally, the process can be highly automated, allowing manufacturers to complete large quantities of work in a short time while maintaining consistent weld quality.
Key Advancements in Resistance Welding Technology
Improved Precision Controls:
One of the most significant advancements in resistance welding technology is the development of advanced control systems. Modern machines are equipped with precision controls that allow operators to fine-tune welding parameters, including current, force, and time, with exceptional accuracy. This ensures more consistent welds and reduces the risk of defects or errors in production. Improved control systems also enable manufacturers to work with a wider variety of materials, from thin sheets to thicker metals, with confidence in weld quality.
Automation and Robotics Integration:
The integration of robotics and automation into resistance welding processes has revolutionized the industry. Automated systems can handle complex welding tasks with minimal human intervention, increasing production efficiency and reducing the risk of errors. Robotics have made it possible to weld components in hard-to-reach areas and perform intricate welding patterns with ease. Taylor-Winfield’s advanced resistance welding machines incorporate cutting-edge robotics technology to deliver faster, more precise results while reducing labor costs.
Electrode and Material Innovations:
The electrodes used in resistance welding play a critical role in the quality and efficiency of the process. Recent innovations in electrode materials and designs have extended electrode life, reduced maintenance requirements, and improved weld consistency. These advancements have made it possible to weld advanced materials, such as high-strength steels and aluminum alloys, which are becoming increasingly common in modern manufacturing, particularly in the automotive and aerospace industries.
Energy Efficiency and Sustainability:
As manufacturers seek to reduce their environmental impact, energy-efficient resistance welding machines manufacturing have become more important. New technologies are being developed to minimize energy consumption during the welding process, making it more sustainable. Additionally, resistance welding produces minimal waste compared to other welding methods, as it does not require filler materials. This makes it a greener alternative for manufacturers looking to meet sustainability goals while also maintaining high production standards.
The Role of Taylor-Winfield in Resistance Welding Innovations
Taylor-Winfield Technologies has been at the forefront of resistance welding innovation, providing solutions that meet the evolving needs of manufacturers. Their machines are designed to deliver reliable, high-quality welds in even the most demanding production environments. Taylor-Winfield’s commitment to innovation is evident in their incorporation of advanced control systems, robotics, and energy-efficient technologies in their resistance welding solutions.
Whether it’s a fully automated system for high-volume automotive production or a specialized solution for the electronics industry, Taylor-Winfield’s resistance welding machines offer flexibility, precision, and durability. Their expert team works closely with manufacturers to develop customized solutions that meet specific production requirements and also help improve overall efficiency.
Conclusion
Advancements in resistance welding technology have transformed the manufacturing landscape, offering greater precision, efficiency, and sustainability. Taylor-Winfield Technologies continues to lead the industry with innovative solutions that help manufacturers stay competitive in a fast-changing market. With cutting-edge control systems, robotics integration, and sustainable practices, resistance welding has evolved into a more versatile and essential tool for modern manufacturing. As technology also continues to advance, manufacturers can expect even greater improvements in weld quality, speed, and cost-effectiveness, ensuring the future success of the industry.
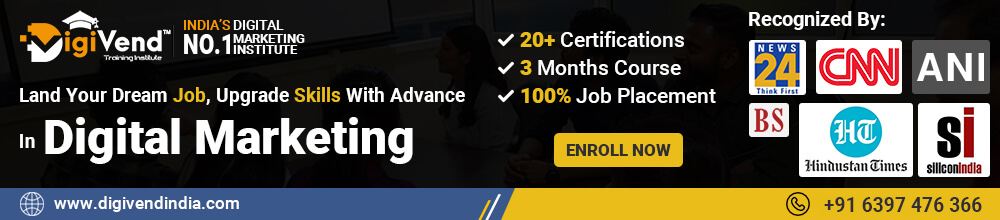