How Equipment Management Software Reduces Equipment Failures
In industries like construction, equipment reliability is not just a luxury—it’s a necessity. The heavy machinery and tools used in these sectors are the backbone of every project, making their smooth operation crucial for maintaining productivity and meeting deadlines.
However, equipment failures and unplanned downtime are common challenges that can severely impact project timelines and budgets. Enter equipment management software, a game-changing solution designed to minimize these issues by enhancing equipment reliability and efficiency.
This blog explores how equipment management software can drastically reduce equipment failures, ensuring that your machinery performs at its best and contributes to a more productive and cost-effective operation.
1. Real-Time Monitoring for Early Detection
One of the most significant benefits of construction equipment management software is its ability to provide real-time monitoring of equipment. This continuous tracking of usage, performance, and health offers a critical advantage: early detection of potential failures.
By analyzing data from sensors and performance metrics, the software can identify anomalies that may signal an impending malfunction. For example, if a piece of machinery shows signs of excessive wear or unusual operating temperatures, the software can alert maintenance teams before a minor issue escalates into a major breakdown.
This proactive approach not only helps in scheduling timely repairs but also in avoiding costly downtime. Real-time monitoring transforms how industries manage their equipment, making it possible to address issues before they disrupt operations.
2. Predictive Maintenance Scheduling
Predictive maintenance is a leap forward from traditional maintenance practices, and equipment management software is at the forefront of this transformation.
By analyzing historical data and usage patterns, the software can forecast when equipment is likely to need maintenance. This data-driven approach allows businesses to plan maintenance activities in advance, based on actual wear and tear rather than arbitrary schedules.
For instance, if the software detects a trend indicating that a certain component usually fails after a specific number of operating hours, it can schedule maintenance just before this threshold is reached.
This not only prevents unexpected breakdowns but also extends the equipment’s lifespan, making predictive maintenance an essential feature of modern construction equipment management software.
3. Centralized Maintenance Records
A centralized platform for tracking maintenance activities is another crucial feature of equipment management software. With all maintenance records stored in one place, it becomes easier to manage and review the history of repairs and servicing.
This centralized approach ensures that no maintenance task is overlooked, reducing the risk of equipment failures due to missed services.
For example, if a piece of machinery requires routine inspections every six months, having a centralized record helps ensure that this schedule is followed diligently. The software provides a clear overview of all maintenance activities, making it simple to keep track of upcoming tasks and ensure that all required services are completed on time.
4. Automated Alerts and Notifications
Automated alerts and notifications are indispensable features of equipment management software. These alerts can be configured for various scenarios, such as scheduled services, inspections, and parts replacements.
By receiving timely reminders, maintenance teams can ensure that equipment remains in optimal condition and prevent failures caused by overdue maintenance.
Imagine a situation where a critical component needs replacement at regular intervals. The software can send automated notifications well in advance, allowing for proactive part replacement and reducing the risk of equipment malfunctions. This level of automation streamlines maintenance processes and contributes to a more reliable operation.
5. Inventory and Parts Management
Effective inventory and parts management is crucial for minimizing equipment downtime. Equipment management software helps track spare parts inventory, ensuring that necessary components are available when needed.
By maintaining a comprehensive inventory record, the software can alert you when stock levels are low and predict future needs based on maintenance schedules and equipment usage.
For example, if a certain part is frequently required for repairs, the software can monitor its usage and ensure that replacements are ordered before stock runs out.
This capability prevents delays in repairs due to unavailable parts, helping to maintain continuous equipment operation and prevent failures caused by part shortages.
6. Data-Driven Decision Making
Data-driven decision-making is a hallmark of modern equipment management. With comprehensive performance data at your fingertips, you can make informed decisions about equipment repair or replacement.
The software analyzes data from various sources, including usage statistics and maintenance history, to provide insights into the health of your equipment.
For instance, if the software identifies a trend indicating that an older piece of equipment is increasingly prone to breakdowns, you can use this information to decide whether a replacement is more cost-effective than continued repairs. By making decisions based on detailed data, businesses can prevent frequent failures and ensure that their equipment fleet remains in optimal condition.
7. Remote Diagnostics and Troubleshooting
Remote diagnostics is a revolutionary feature of equipment management software that allows for troubleshooting without being physically present.
Through remote access, maintenance teams can diagnose issues and perform troubleshooting tasks from anywhere, which significantly reduces response times and minimizes the risk of equipment failures.
For example, if an equipment malfunction is detected, technicians can use remote diagnostics to identify the problem and determine the necessary repairs. This capability not only speeds up the resolution process but also reduces the need for on-site visits, making it easier to manage equipment issues efficiently.
8. Improved Operator Accountability and Training
Equipment management software also plays a role in enhancing operator accountability and training. By monitoring operator performance and usage patterns, the software can identify instances of improper use that may lead to equipment strain or failures.
For example, if an operator frequently exceeds recommended operating conditions, the software can flag these incidents and provide insights into how they might be impacting equipment health.
This information can be used to provide targeted training, helping operators understand best practices and reduce the risk of equipment damage. Proper training based on software insights not only improves equipment longevity but also enhances overall operational efficiency.
9. Compliance with Safety and Regulatory Standards
Compliance with safety and regulatory standards is essential for maintaining equipment reliability and avoiding legal issues. Equipment management software helps ensure that all equipment meets safety and maintenance regulations by keeping track of inspection schedules and compliance requirements.
For instance, the software can generate reports and reminders for compliance checks, ensuring that all necessary inspections and certifications are completed on time. By adhering to these standards, businesses can prevent failures linked to regulatory lapses and ensure that their equipment operates safely and efficiently.
Conclusion
In conclusion, equipment management software is a vital tool for reducing equipment failures and enhancing operational efficiency. By leveraging features such as real-time monitoring, predictive maintenance, centralized records, automated alerts, and data-driven decision-making, businesses can significantly minimize the risk of equipment malfunctions and downtime.
Investing in construction equipment management software not only improves equipment reliability but also contributes to a more streamlined and cost-effective operation. Embracing this technology is a proactive step towards achieving greater equipment longevity and operational success.
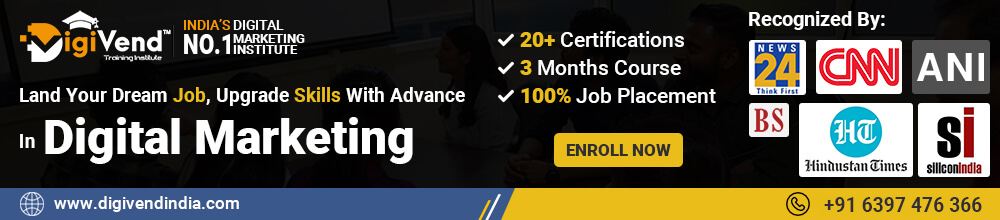