Cutting Laser CO2: A Comprehensive Guide
cutting laser co2 technology, an indispensable tool in modern manufacturing, revolutionizes the way materials are cut with precision and efficiency. This article delves into the intricacies of CO2 laser cutting, exploring its applications, advantages, and technical aspects. If you’re looking to understand why cutting laser CO2 is a game-changer in various industries, read on for a detailed exploration.
Introduction to CO2 Laser Cutting
CO2 lasers, developed in the 1960s, have become a cornerstone in industrial cutting processes. These lasers operate using a gas mixture primarily consisting of carbon dioxide, nitrogen, and helium. When electrically stimulated, this mixture produces a high-powered beam of infrared light, capable of cutting through a wide range of materials with unparalleled precision.
How CO2 Laser Cutting Works
Basic Principles
At its core, CO2 laser cutting involves directing a high-intensity laser beam onto the surface of the material. The laser’s energy is absorbed by the material, causing it to melt, burn, or vaporize. The process is controlled by a computer-aided design (CAD) system, ensuring precise and accurate cuts.
Components of a CO2 Laser Cutter
- Laser Resonator: Generates the laser beam through the excitation of the CO2 gas mixture.
- Beam Delivery System: Guides the laser beam from the resonator to the cutting head, often using mirrors.
- Cutting Head: Focuses the laser beam onto the material’s surface. It includes a focusing lens and a nozzle for directing assist gases.
- Assist Gases: Typically oxygen or nitrogen, these gases help in the cutting process by blowing away molten material and preventing oxidation.
Applications of CO2 Laser Cutting
Industrial Manufacturing
CO2 laser cutting is widely used in various manufacturing sectors, including automotive, aerospace, and electronics. It is ideal for cutting metals, plastics, wood, glass, and textiles, providing clean and precise cuts that minimize material waste.
Medical Devices
In the medical field, CO2 lasers are used to manufacture intricate components of medical devices. The precision of laser cutting ensures that components meet the stringent standards required for medical applications.
Signage and Advertising
The advertising industry benefits from CO2 laser cutting by creating detailed and custom-designed signs. Materials like acrylic, wood, and metals are commonly used, and the precision of laser cutting allows for intricate and high-quality designs.
Jewelry Making
Jewelry designers use CO2 laser cutting to create intricate patterns and designs in metals and gemstones. The precision of the laser ensures that each piece meets exacting standards.
Advantages of CO2 Laser Cutting
Precision and Accuracy
One of the primary advantages of CO2 laser cutting is its precision. The focused laser beam can achieve extremely fine cuts with tolerances in the micrometer range, making it ideal for detailed and complex designs.
Versatility
CO2 lasers can cut through a wide range of materials, including metals, plastics, wood, glass, and fabrics. This versatility makes them suitable for various industries and applications.
Speed and Efficiency
CO2 laser cutters operate at high speeds, significantly reducing production time. The automation of the process through CAD systems ensures consistent and repeatable results, enhancing overall efficiency.
Minimal Material Waste
Laser cutting is a non-contact process, meaning there is minimal mechanical stress on the material. This results in less material waste compared to traditional cutting methods, which is both cost-effective and environmentally friendly.
High-Quality Finishes
The precision of CO2 laser cutting ensures smooth and clean edges, often eliminating the need for secondary finishing processes. This results in high-quality products with aesthetically pleasing finishes.
Technical Aspects of CO2 Laser Cutting
Laser Power and Intensity
The power of the laser, measured in watts, determines its cutting capability. Higher power lasers can cut through thicker materials, while lower power lasers are suitable for finer, detailed work. The intensity of the laser beam is controlled by adjusting the power and the speed at which the cutting head moves.
Focus and Beam Quality
The quality of the laser beam, known as beam quality, affects the precision of the cut. A high-quality beam with a small focal spot size can produce finer cuts. The focus of the laser beam is adjusted using lenses in the cutting head, ensuring that the energy is concentrated on the material’s surface.
Assist Gases
The choice of assist gas depends on the material being cut. Oxygen is typically used for cutting metals, as it promotes combustion and enhances cutting speed. Nitrogen, on the other hand, is used for cutting non-metals and metals where oxidation needs to be minimized.
Cutting Speed and Feed Rate
The cutting speed and feed rate are crucial parameters that influence the quality of the cut. Higher speeds are suitable for thinner materials, while thicker materials require slower speeds to ensure complete penetration of the laser beam.
Computer-Aided Design (CAD) Integration
Modern CO2 laser cutters are integrated with CAD systems, allowing for precise control of the cutting process. CAD software is used to create detailed designs and patterns, which are then translated into instructions for the laser cutter. This integration ensures accuracy and repeatability in the cutting process.
Safety Considerations
Laser Safety
CO2 lasers emit high-intensity infrared light, which can be harmful to the eyes and skin. Proper safety measures, including protective eyewear and shielding, are essential to prevent accidental exposure.
Ventilation and Fume Extraction
The cutting process can produce fumes and particulates, especially when cutting plastics and other non-metals. Adequate ventilation and fume extraction systems are necessary to maintain a safe working environment and prevent respiratory issues.
Material Handling
Proper handling of materials is crucial to avoid accidents and ensure the quality of the cuts. This includes securing the material on the cutting bed and ensuring it is free from contaminants that could affect the cutting process.
Future Trends in CO2 Laser Cutting
Advancements in Laser Technology
Ongoing advancements in laser technology are continually improving the efficiency and capabilities of CO2 laser cutters. Developments in laser power, beam quality, and automation are expected to enhance cutting precision and expand the range of materials that can be processed.
Integration with Smart Manufacturing
The integration of CO2 laser cutting with smart manufacturing systems, including IoT and AI, is poised to revolutionize the industry. These technologies enable real-time monitoring and optimization of the cutting process, resulting in improved efficiency and reduced downtime.
Sustainable Practices
As industries move towards more sustainable practices, CO2 laser cutting is expected to play a significant role. The precision and efficiency of laser cutting reduce material waste, and advancements in laser technology are leading to more energy-efficient systems.
Conclusion
Cutting laser CO2 technology is a versatile and efficient tool that has transformed various industries. Its precision, speed, and ability to cut a wide range of materials make it indispensable in modern manufacturing. As technology advances, the capabilities and applications of CO2 laser cutting continue to expand, promising even greater contributions to industrial and commercial processes. Whether you are in manufacturing, medical device production, signage, or jewelry making, understanding the benefits and technical aspects of CO2 laser cutting can provide a competitive edge in your industry.
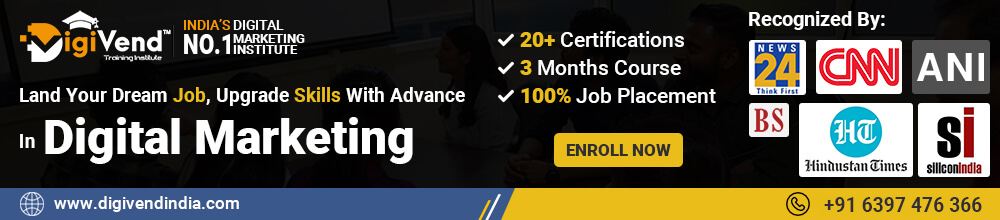